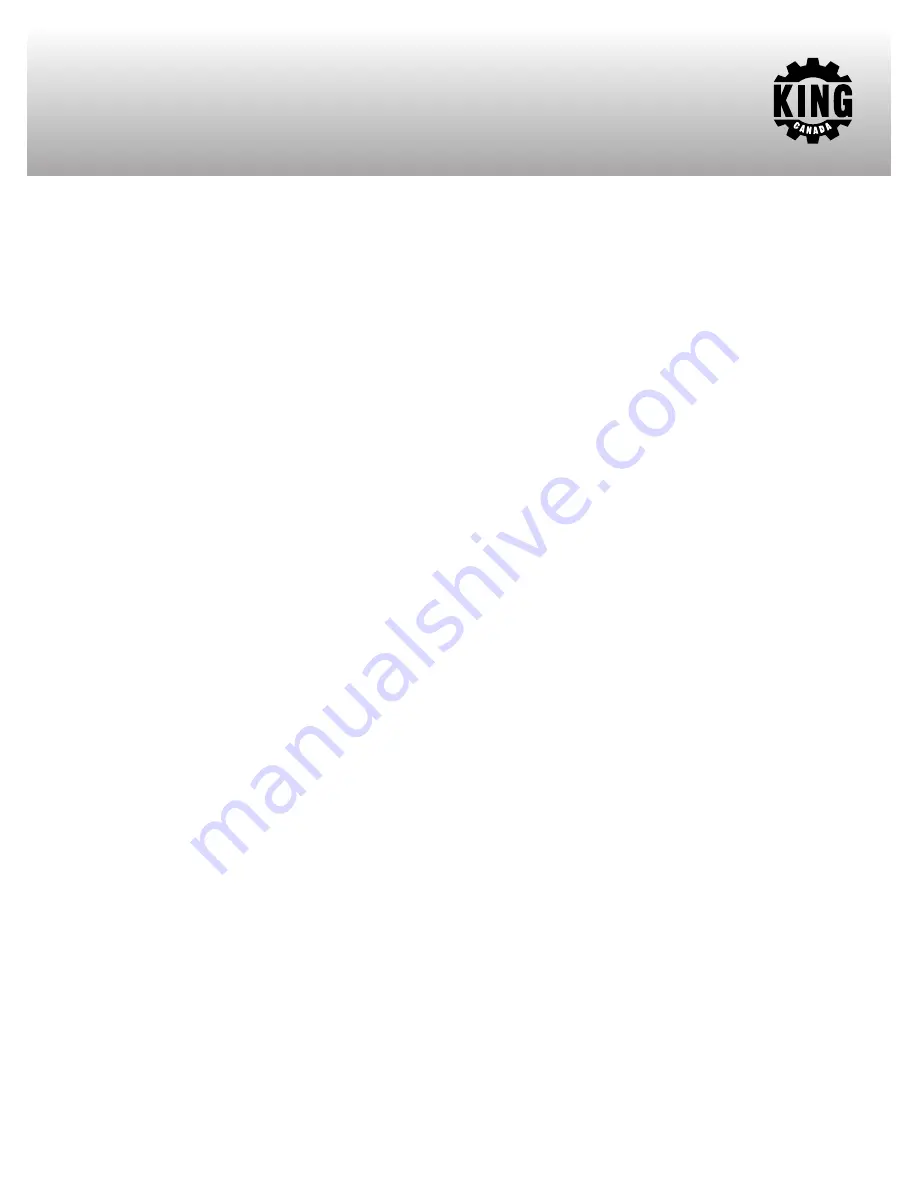
BREAK-IN PROCEDURES & OPERATION
ASSEMBLY AND LOCATION OF THE AIR COMPRESSOR
Your compressor comes almost completely assembled. The muffler part# 78 (refer to parts diagram) must be screwed to the cylinder cover #3.
The oil breather cap #20 must be screwed to the crankcase cover #24. It may be necessary to install the pressure gauges #’s 50, place teflon
tape around the pressure gauge threaded shaft and fix them in their respective places. Assemble both 8” rubber wheels to the wheel shaft, then
the wheel shaft to the wheel shaft brackets on the base of the tank. Finally, lock carry handle into place with the 2 supplied lock knobs #81, make
sure to tighten the 2 lock knobs into both holes in the carry handle for a secure installation.
Operate the air compressor in a dry, clean, cool, well ventilated area. the air compressor pump and case are designed to allow for proper
cooling. Clean or blow off dust or dirt that collects on the air compressor. A clean air compressor runs cooler and provides longer service. The
ventilation openings on your air compressor are necessary to maintain proper operating temperature. Do not place rags or other containers on
or near these openings.
ADDITIONAL REGULATORS AND CONTROLS
Since the air tank pressure is usually greater than that which is needed, a regulator is employed to control the air pressure ahead of any
individual driven device. Seperate air transformers which combine the function of air regulation, moisture and dirt removal should be used where
applicable.
BREAK-IN PROCEDURES
NOTE: MAKE SURE THAT YOU HAVE FILLED THE CRANKCASE WITH COMPRESSOR OIL UP TO THE CENTER DOT OF THE OIL LEVEL
AS DESCRIBED IN “MAINTENANCE SECTION” AND THAT ALL ASSEMBLY INSTRUCTIONS ABOVE HAVE BEEN FOLLOWED BEFORE
DOING THE FOLLOWING “BREAK-IN PROCEDURES (MUFFLER, OIL BREATHER CAP AND PRESSURE GAUGES). SERIOUS DAMAGE
MAY RESULT IF THE FOLLOWING BREAK-IN INSTRUCTIONS ARE NOT CLOSELY FOLLOWED. THIS PROCEDURE IS REQUIRED
BEFORE THE AIR COMPRESSOR IS PUT INTO SERVICE, OR AFTER REPLACING THE CHECK VALVE, AND WHEN THE PISTON OR
THE CYLINDER SLEEVE IS REPLACED.
A. Set the pressure switch to the “OFF” position.
B. Plug the power cord into the correct branch circuit receptacle.
C. Turn the drain valve (B) Fig. 4, opening it fully, to prevent air pressure build-up in the tank.
D. Move the pressure switch to “ON/AUTO”. The compressor will start.
E. Run the compressor for 15 minutes. Make sure the drain valve is open and there is no tank pressure build-up.
F. After 15 minutes, close the drain valve by turning the knob. The air receiver will fill to cut-out pressure and the motor will stop. The air
compressor is now ready for use.
OPERATING PROCEDURES
Preparation for use:
1. Before attaching air hose or accessories, make sure the OFF/AUTO is set to “OFF” and the air regulator is closed.
2. Attach hose and accessories.
WARNING
: Too much air pressure causes a hazardous risk of bursting. Check the manufacturer's maximum pressure rating for air tools and
accessories. The regulator outlet pressure must never exceed the maximum pressure rating of the tool being used.
3. Turn the “OFF/AUTO” to “ON” and allow tank pressure to build. Motor will stop when tank pressure reaches “cut-out” pressure.
4. Open the regulator by lifting it and then turning it clockwise. Adjust the regulator to the correct pressure setting. The compressor is ready for use.
5. Always operate the air compressor in well ventilated areas; free of gasoline or other solvent vapors. Do not operate the compressor near the
spray area.
After Use:
6. Set the switch to “OFF”.
7. Lift then turn the regulator button counterclockwise to set the outlet pressure to zero and finaly push the button down again to lock in place.
8. Remove the air tool or accessory.
9. Pull ring on safety valve (H) Fig. 5, allowing air to bleed from the tank until tank pressure is approximately 20 psi. Release safety valve ring.
10. Drain water from air tank. Turn drain valve (B) Fig. 4, counterclockwise to open.
WARNING!: WATER WILL CONDENSE IN THE AIR TANK. IF NOT DRAINED WATER WILL CORRODE AND WEAKEN THE AIR TANK
CAUSING A RISK OF AIR TANK RUPTURE.
NOTE: If drain valve is plugged, pull ring on safety valve (H) Fig. 5, and hold until air pressure has been released. The valve can then be removed,
cleaned, and reinstalled.