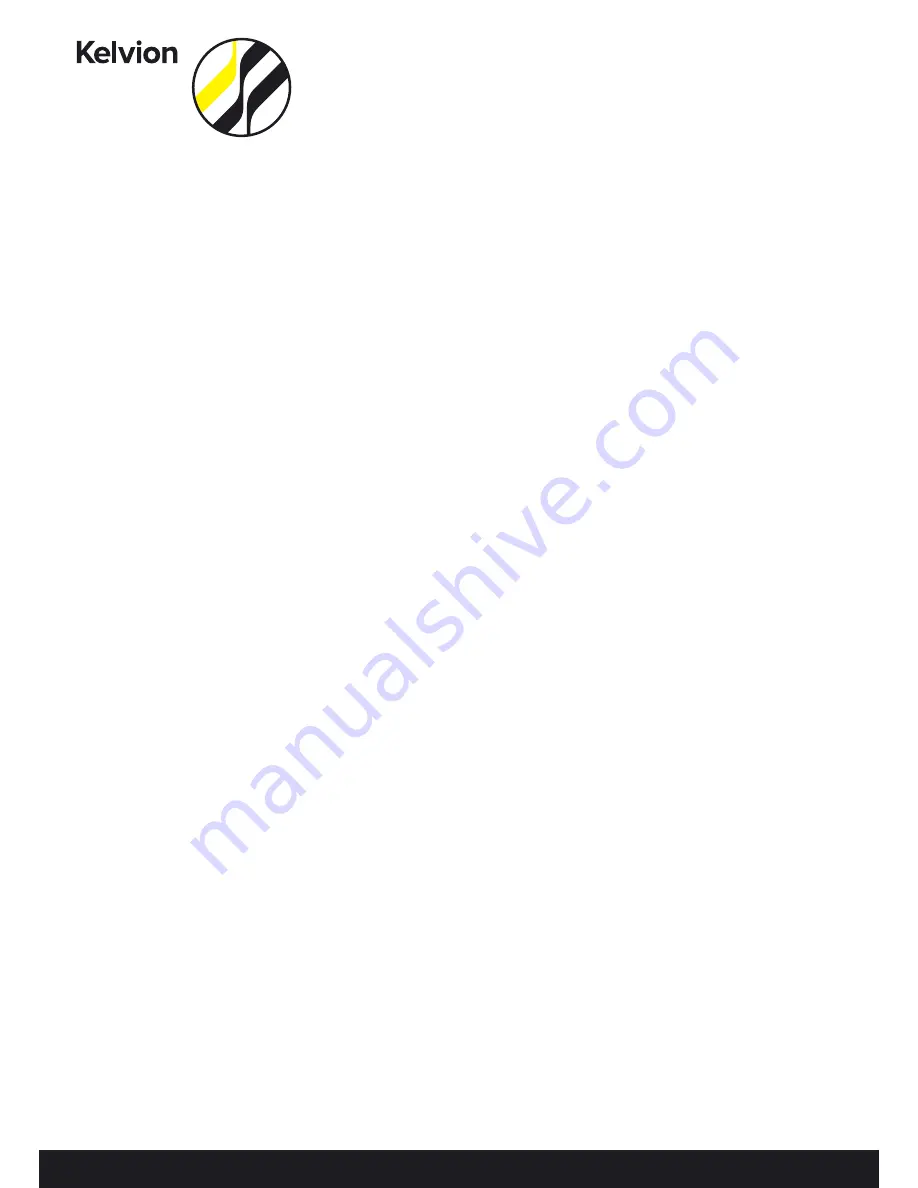
Searle Air Cooler
15. DEFROST
Air cooling evaporators whose surface temperature is lower than the dew point of the air they are cooling will accumulate
moisture from the air. When the surface temperature is below freezing, this moisture will be deposited in the form of frost and
eventually, if left, will restrict heat transfer and air flow.
Various methods are used for the removal of frost. When the air inlet temperature is at 3°C or higher it is possible to use nat-
ural defrost by just switching off the refrigeration flow for a period. At lower temperatures heat needs to be added and the
fans switched off to prevent the heat being blown into the store. The heat can be from electrical elements passing through or
adjacent to the fin, hot/warm refrigerant gas passing through the tubes or, less commonly, water cascaded over the fins or a
warm glycol solution in a secondary system of tubes.
Defrost options
Hot-gas defrost can be the quickest and most efficient common method of defrost. The fact that heat is applied to all the
same surfaces that provided the cooling means that frost is melted quickly and evenly. The low temperature of the heat,
compared to electric defrost, results in less heat, in the form of steaming condensate, escaping from the cooler into the
coldstore.
HG(E)A, HG(E)B – Reverse Cycle
Generally used on systems with one or two evaporators. During defrost the condenser is used as an evaporator and the
refrigeration system acts as a heat pump. During defrost the flow is in the reverse direction as it is usually most convenient to
redirect flow close to the compressor. As the evaporator acts as a condenser in this regime the hot gas is at high pressure/
high temperature giving a superior performance in comparison to a hot gas system.
HG(E)C, HG(E)D
Where there are two or more evaporators on a refrigeration system it is possible to defrost one using the hot-gas generated
in the operating of the other. This arrangement allows defrost flow to be in the same direction as cooling flow. Although this
arrangement can operate on a two evaporator system the quantity of low pressure, super heated gas is minimal, therefore it
is recommended that this arrangement is used on systems with three or more evaporators, with one evaporator on defrost
whilst the other evaporators are operational, generating the defrost heat.
Defrost Header - HG(E)B, HG(E)C
Without a defrost header the distribution system causes a restriction reducing the flow rate of hot-gas. This reduces the rate
of defrost and can result in condensed refrigerant logging in the coil and preventing even defrosting. This problem is more
likely the less superheat the hot-gas has.
Drain Pan Defrosting – HGE
Hot gas can be used for drain pan defrost but the lower heating temperature makes it difficult for heat to reach the extremes
of the drain-pan. Also, the drain-pan is more exposed to the room temperature and will quickly drop to room temperature
when the defrost is terminated, with the possibility of condensate still running of the coil to freeze in the pan. Using electric
defrost in the pan overcomes these disadvantages, particularly as it can be controlled to operate for a short time before and
after the main defrost.
The best configuration of hot gas coil and tray defrost is to ensure that the hot gas enters the tray matrix first then enters the
coil, this is arranged via the valve station supplied and fitted by the refrigeration contractor.
Initial Defrost Termination Settings
Time/Time defrost system
KMe, KEC, TEC, DSR , LSR, FM, SM: 30 minutes
Time/Temperature termination system
TEC, KEC, KMe - Electric defrost: minimum setting 4.5°C
DSR, LSR, SM, FM - Electric defrost: minimum setting 11°C