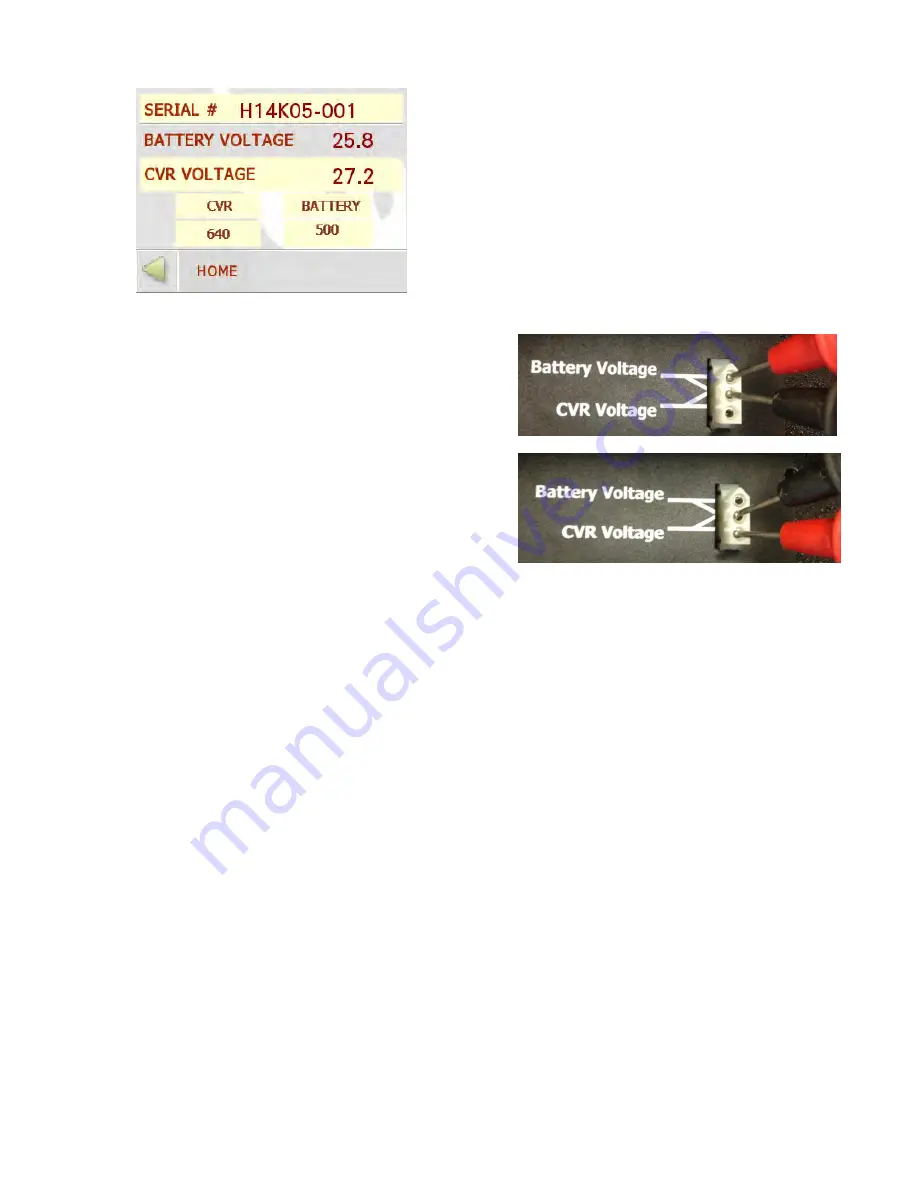
43
Using the screen to the left, press on the Voltage
you want to adjust; the buttons will become
enabled and an adjustment reference number will
appear.
To adjust the voltage meters accurately you
must have a dependable voltmeter. Locate
the three-pin plug above the fuse bank.
Put the voltmeter probes in the appropriate
pins then add or subtract using the buttons
at the bottom of the screen until the Voltage
on the screen matches the correct Voltage
from the external voltmeter.
Содержание IKON Lane Machine
Страница 1: ...IKON Lane Machines ...
Страница 2: ...KEGEL LLC 1951 Longleaf Blvd Lake Wales FL 33859 863 734 0200 I 800 280 2695 ...
Страница 3: ......
Страница 5: ......
Страница 13: ......
Страница 17: ...4 ...
Страница 32: ...19 ...
Страница 47: ...34 ...
Страница 103: ...90 CHAPTER 9 Miscellaneous Parts Stickers and Decals ...
Страница 104: ...91 164 0014o 714C 164 0015o 714C 164 0024 Part Number for the K only 164 0023o 714C Part Number for the ION only ...
Страница 107: ...94 ...
Страница 110: ...1 2 3 4 5 7 8 6 9 10 11 13 14 12 ...
Страница 112: ...5 4 1 2 3 ...
Страница 114: ...DETAIL A DETAIL B A B 7 8 9 1 4 3 2 5 6 ...
Страница 116: ...6 3 5 4 7 1 2 ...
Страница 118: ...5 3 4 1 2 ...
Страница 120: ...DETAIL A A 1 4 3 2 8 9 10 11 6 7 5 ...
Страница 122: ...3 4 5 6 7 1 2 ...
Страница 124: ...9 8 7 6 10 14 15 11 12 13 5 17 18 1 2 3 4 16 ...
Страница 126: ...12 11 1 1 13 14 15 10 6 7 9 8 1 2 3 4 5 6 ...
Страница 128: ...DETAIL A A 8 3 7 6 5 4 11 10 9 12 1 2 13 ...
Страница 130: ...1 9 5 11 4 10 7 2 8 3 6 17 16 13 12 14 ...
Страница 132: ...DETAIL A A 6 2 3 1 7 8 5 4 9 ...
Страница 134: ...DETAIL A A 1 1 1 2 1 3 14 13 12 11 10 9 4 2 4 1 8 4 4 4 3 7 6 1 4 1 5 2 3 4 ...
Страница 136: ...1 6 3 8 10 1 9 6 7 8 10 5 2 1 4 2 1 5 4 2 ...
Страница 138: ...8 4 3 7 6 5 9 1 2 ...
Страница 140: ...3 1 1 1 5 6 7 8 4 2 ...
Страница 141: ...127 ...
Страница 143: ......
Страница 144: ......
Страница 145: ......
Страница 146: ......
Страница 147: ......
Страница 148: ......
Страница 149: ......
Страница 150: ......
Страница 151: ......
Страница 152: ......
Страница 153: ......
Страница 154: ......
Страница 155: ......
Страница 156: ......
Страница 157: ......
Страница 158: ......
Страница 159: ......
Страница 160: ......
Страница 161: ......
Страница 162: ......
Страница 163: ......
Страница 164: ......
Страница 165: ......
Страница 166: ...151 ...
Страница 167: ...152 ...