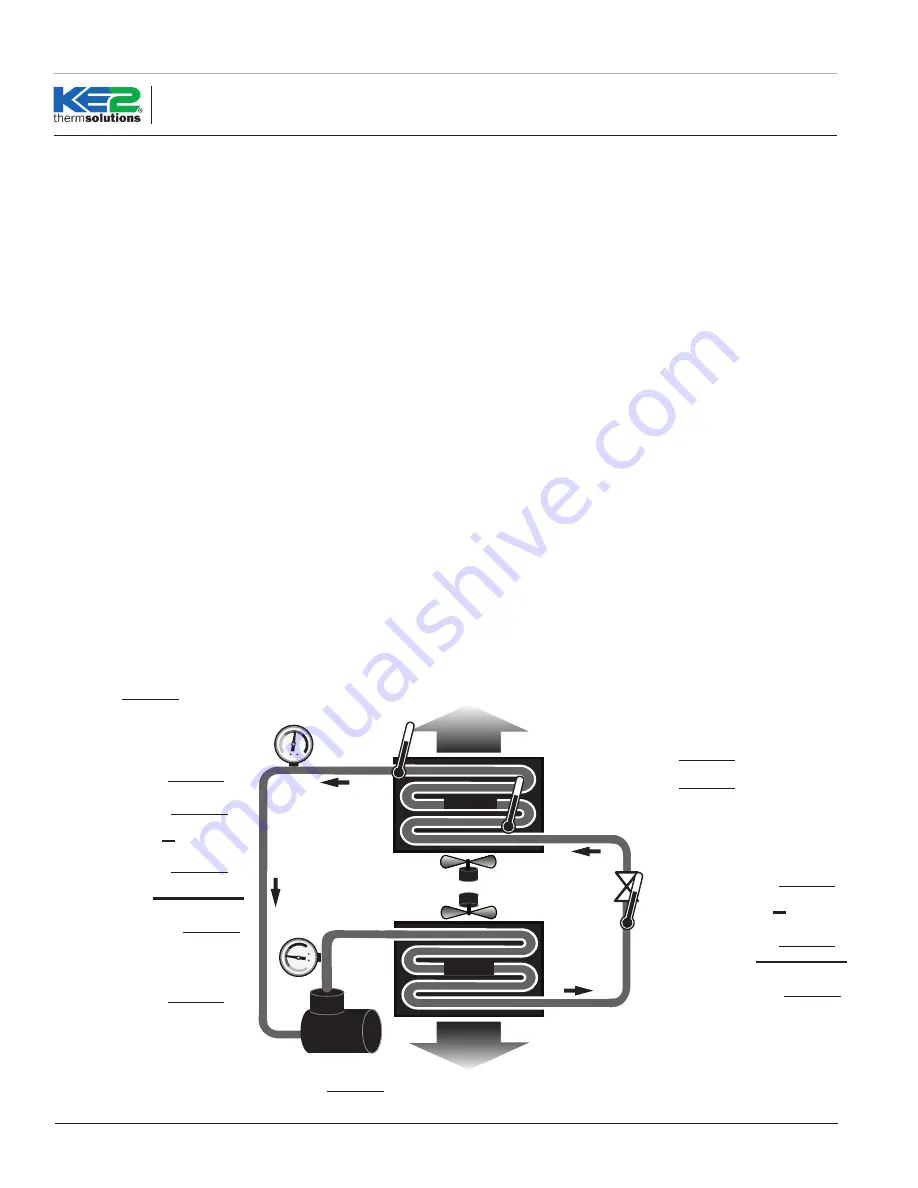
© Copyright 2016 KE2 Therm Solutions, Inc., Washington, Missouri 63090
Q.1.35 January 2016
Page 2
KE2 Adaptive
Control
Quick Start Guide
for low temperature applications, and 8-10 degrees for medium
temperature.
Subcooling - There should be a solid column of liquid at the inlet of
the valve. This can be verified by looking at the sight glass, however,
the proper method requires measuring the subcooling of the liquid
entering the valve.
Verify Temperature Difference
A typical Temperature Difference (TD) between the coil temperature
and the air temperature is between 5 and 15°F. An insufficient TD,
between the coil and air temperature, indicates a system issue that
needs to be addressed before installing the KE2 Adaptive Control.
Understanding Frost
The air exiting side of the evaporator is often the coldest spot on
the coil. As air travels through the fins of the evaporator, the Relative
Humidity will reach 100%. Moisture will begin to drop out of the air
and deposit on the coil surfaces to form frost. Although frost typi-
cally has a negative connotation when discussed in refrigeration,
initial frost formation has a positive effect. Some may even say “frost
is our friend.” It is not uncommon to see a small amount of frost on
the coils that have KE2 Adaptive Control controllers installed. The KE2
Adaptive Control is continually measuring, monitoring, and manag-
ing the frost to assist in maximum energy efficiency. When the ef-
ficiency of the coil is reduced due to excessive frost, the KE2 Adaptive
Control will initiate a defrost.
Liquid/Vapor Mix
Restrictor,
TEV or EEV
Warm Liquid
Cold Vapor
Hot Vapor
Warm Air
Cold Air
Evaporator
Compressor
Condenser
Saturation Temp
°F
(from receiver pressure)
Liquid Temp at Valve
°F
Subcooling °
Suction Pressure
PSI
Suction Temp
°F
(evaporator outlet)
Saturation Temp
°F
(calculated from Suct. Pressure)
Superheat
°
Temp Difference (TD)
°F
(return air minus coil temp)
Coldest point in evap
°F
AMPS
Trouble Shooting Diagram
Discharge Pressure
PSI
Refrigerant
Arriving at the Jobsite
When arriving at any jobsite, it is good practice to verify the correct
operation of the system. Even systems running for a considerable
amount of time without requiring a service call may not be running
properly.
Inspect the coil to see the current frost pattern. If the unit has not
recently performed a defrost, look for the heaviest area of frost. This
will be used to locate the coil sensor.
Installers should account for a full system diagnostic in the installa-
tion estimate for the controller.
Although it may seem unnecessary, identifying system issues before
the controller is installed will save time overall. It will also allow the
controller to provide the highest energy savings.
Verify the system is running correctly. Taking several measurements
will help determine the current health of the system. Using the dia-
gram below, fill in the necessary information.
Two of the most critical indicators of system health are the super-
heat and subcooling.
Superheat - Superheat is the most overlooked inefficiency in exist-
ing systems. Typically the superheat on a TEV is set when there is not
product in the controlled space, if it is set at all.
When applying the controller to an existing system with a mechani-
cal expansion valve, the superheat should be between 6-8 degrees