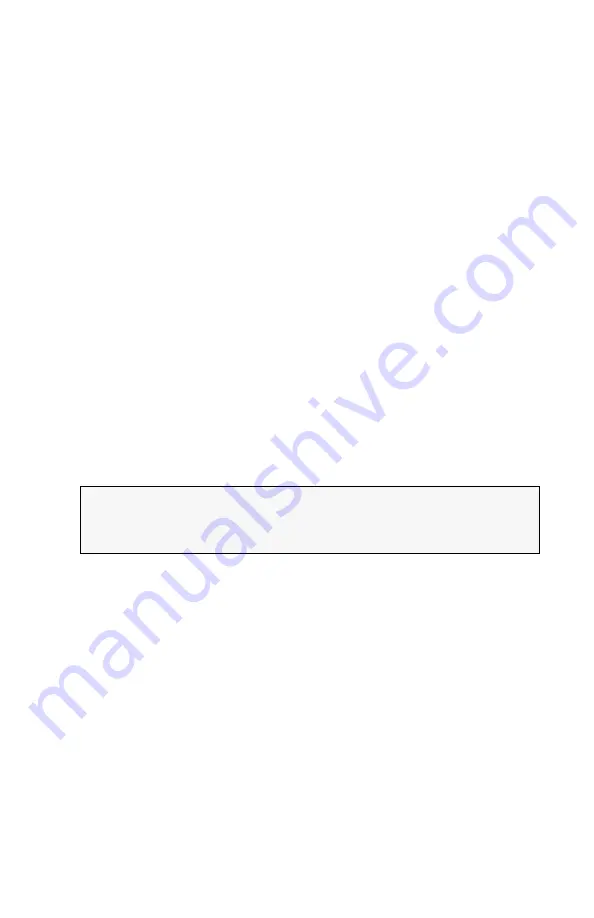
Optional accessories include On/Off AC Line Switch, FWD-BRK-REV Switch, Run-Stop-Jog
Switch, Signal Isolator, and Anti-Plug Reversing Module. Quick-connect terminals are pro-
vided for easy installation of all optional accessories. The control is available in black finish
(P/N 8401) and FDA approved white finish (P/N 8402).
STANDARD FEATURES
•
Short Circuit Protection –
Protects control from a short circuit at motor connections.
•
Electronic Motor Burnout Protection –
Shuts down the control if a prolonged overload con-
dition exists.
•
Active Bridge –
Limits the AC line inrush current when power is turned on and also prevents
high speed runaway if the power transistor shorts.
•
Heat Spreader –
Allows power transistor to operate safely during momentary overload con-
ditions.
•
Auto AC Line Select –
Control automatically adjusts for 115 or 208/230 Volt AC line input.
•
Start/Stop Switch –
Provides electronic start and stop functions.
•
Diagnostic LEDs –
For power on (ON), stop (STOP) and motor overload (OL).
•
Trimpots –
Provide adjustment for acceleration (ACCEL), deceleration (DECEL), maximum
speed (MAX), minimum speed (MIN), jog speed (JOG), current limit (CL), timed current limit
(TCL), and IR compensation (IR).
•
Selectable Jumpers –
Provide settings for armature voltage or tach-generator feedback
(J1), motor current (J2), timed or non-timed current limit (J3), tach-generator voltage (J4), and
run relay output (J5).
•
Barrier Terminal Blocks –
Facilitate wiring of AC line, motor armature and field, tach-gen-
erator, and run relay output.
•
Quick-Connect Terminals –
Facilitate connecting Start/Stop switch, Run-Stop-Jog switch,
FWD-BRK-REV switch, and Inhibit switch.
II.
SIMPLIFIED OPERATING INSTRUCTIONS
A. Power Connection –
Connect the AC line to L1 and L2 terminals of TB1 and the ground
wire (Earth) to the green ground screw as shown in Figure 3, on page 6 and as described
in Section IIIA, on page 6 and Section IIIB, on page 6.
B. Permanent Magnet (PM) Motor Connection (Two-Wire Type) –
Connect the motor
armature to A1 (+) and A2 (-) terminals of TB1 as shown in Figure 3, on page 6 and as
described in Section IIIC, on page 6. Be sure that jumper J3 is set to the corresponding
motor voltage position as described in Section IVA, on page 9.
Do not use F1 and F2
terminals of TB2 for any purpose other than to power the field of a shunt wound
motor. Do not use F1 and F2 terminals for PM motors.
Note:
Motor performance and efficiency, including brush life, may be adversely affected
when operating the control in stepdown mode (208/230 Volt AC line with 90/130 Volt DC
motors).
C. Shunt Wound Motors (Four-Wire Type) –
Connect the motor armature as described in
Section IIIC, on page 6. Connect full voltage field wires (90 Volt DC motors with 100 Volt
DC field and 180 Volt DC motors with 200 Volt DC field) to F1 (+) and F2 (-) terminals of
TB2 as described in Section IIID, on page 7. Connect half voltage field wires (90 Volt DC
motors with 50 Volt DC field and 180 Volt DC motors with 100 Volt DC field) to F1 (+) ter-
minal of TB2 and L1 (-) terminal of TB1 as described in Section IIIE, on page 7.
Note:
Do not connect motor armature leads to F1 and F2 terminals.
2
IMPORTANT
– You must read these simplified operating instructions before proceeding.
These instructions are to be used as a reference only and are not intended to replace the
detailed instructions provided herein. You must read the Safety Warning, on page 1,
before proceeding.