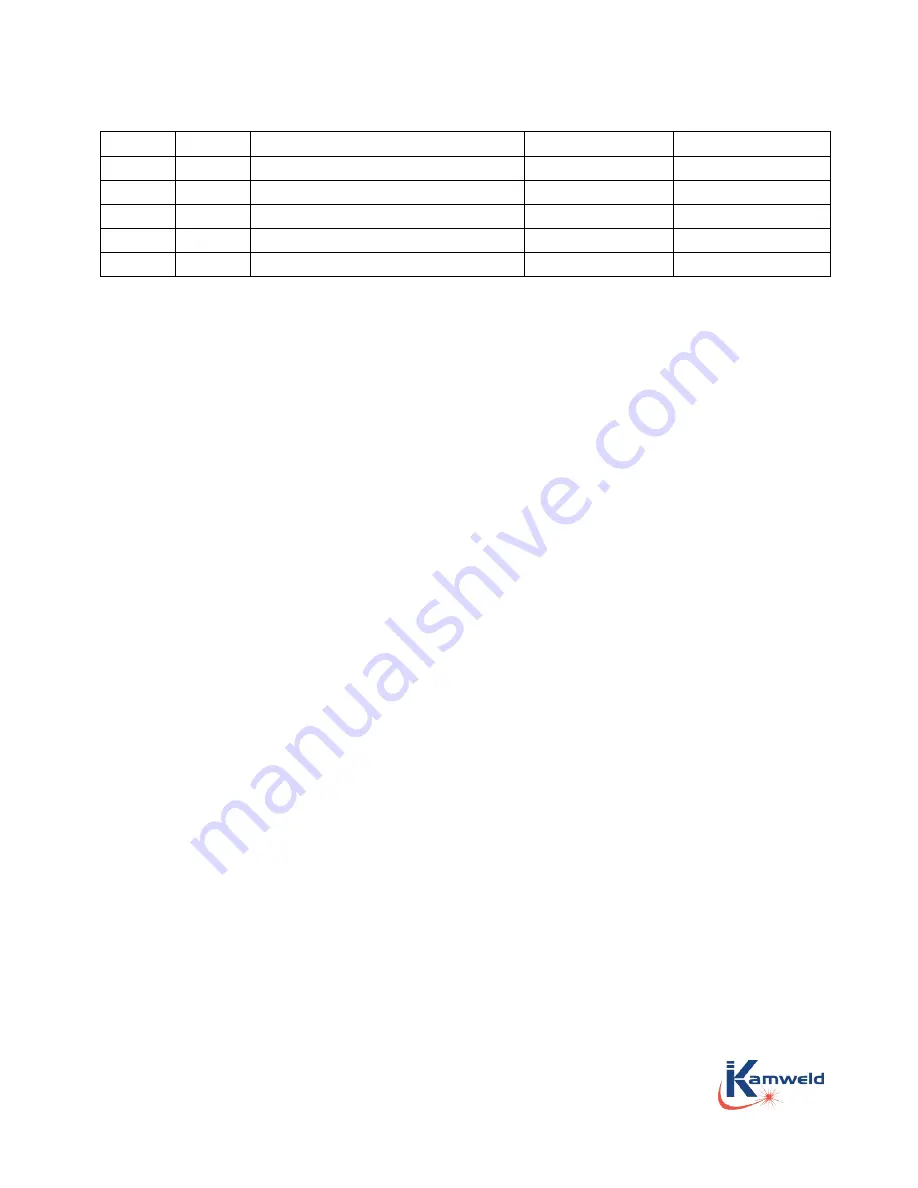
9
Table 2. List of control parameters and its initial settings under code 166.
Symbol Display
Description
Range
Initial
P
P
Proportional Band
0-9999
7
I
I
Integral Const. (Sec.)
0-9999
600
d
d
Derivative Const. (Sec.)
0-9999
150
AT
AT
Auto-tune
0=off, 1=on
0
t
T
Cycle Rate (Sec.)
2-9999
2
Details about each parameter
•
P
, Proportional band. It is in 1 degree units. This parameter controls the output of the
controller based on the difference between the measured and set temperatures. The
larger the P number means the weaker the action (lower gain). For example, if P=7, the
proportional band is 7 degrees. When the sensor temperature is 7 degrees below the
proportional band (7 degrees below the setting), the controller will have 100% output.
When the temperature is 5 degrees below the set point, the output is 71%. When the
temperature is equal to the setting, the controller will have 0% output (assuming integral
and derivative functions are turned off). This constant also affects both integral and
derivative action. Smaller P values will make both integral and derivative action stronger.
Please note the value of the P is temperature unit sensitive. If you found an optimized P
value when operating the controller in Fahrenheit, you need to divide the P by 1.8 when
changing the temperature unit to Celsius.
ON/OFF mode
. If P is set to 0, the control mode will be changed from PID mode to
ON/OFF mode. ON/OFF mode should be used for controlling an external relay, a
solenoid valve, or a compressor of freezer. You also need to set the hysteresis band
(dead band) for the on/off mode. In the on/off mode, Integral and Derivative parameters
are not valid.
•
I
, Integral time. The unit is in seconds. This parameter controls the output of controller
based on the difference between the measured and set temperature integrated with time.
Integral action is used to eliminate temperature offset. Larger number means slower
action. e. g. assuming the difference between the measured and set temperature is 2
degrees and remain unchanged, the output will increase continuously with time until it
reaches 100%. When temperature fluctuate regularly (system oscillating), increase the
integral time. Decrease it if the controller is taking too long to eliminate the temperature
offset. When I=0, the system becomes a PD controller. For very slow response system
set I = 0 will significantly reduce
the temperature overshoot.
•
d
, Derivative time. The unit is in seconds. Derivative action contributes the output power
based on the rate of temperature change. Derivative action can be used to minimize the