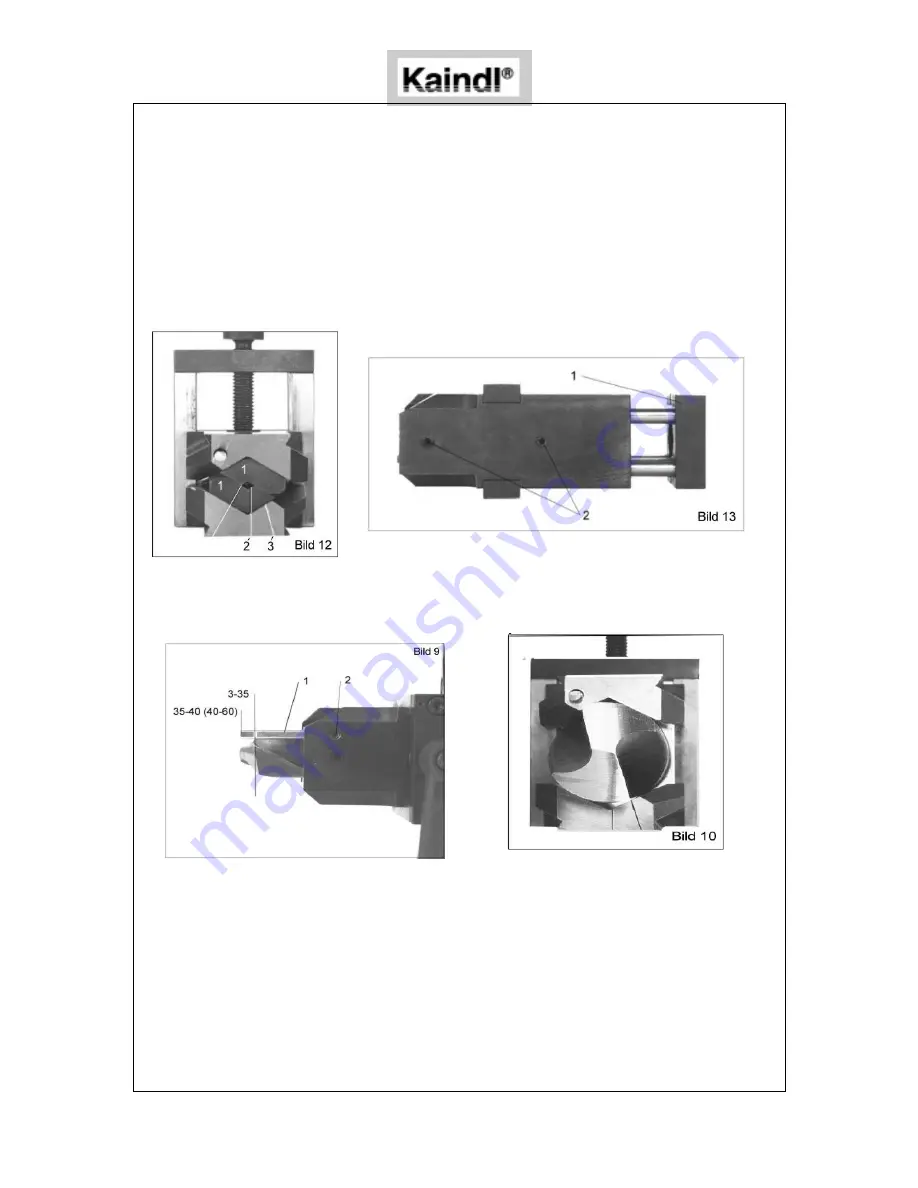
10
Operation
For drills from 3-20 mm use the prism including the inner jaws. For drills from 20 – 40 mm
remove the inner jaws.
Removing of the inner jaws:
Loosen the 4 pcs socket head cap screws with a suitable
key SW 2,5 mm
Mounting of the inner jaws:
Place the inner jaws inside the prism in the way that the graduation marks are in line
with the outer marks (Pic. 12) The numers on the jaws shall not be visible.
Softly tighten the fixation screws (Pic 13). Do not tighten too strong.
Clamping and alignment of right hand helix drills
Loosen clamping screw 2 and pull out the pin 1 to the stop dog and fix again
Depending on the diameter, let the drill project outside the prism (Pic. 9)
Drills from 3 – 35 mm cutting edge to graduation notch.
Drills from 35 – 40 mm cutting edge to total lengh of the pin.
Then align the cutting edge parallel to the slantwise graduation line. (Pic. 10).
For getting a parallel clamping of small drills, we propose to clamp a second drill of same
diameter on the back of the prism.
For drills with bigger diameter also use the prism elongation for the cylindrical part (Pic.13
item 1) Move back pin 1 and fix with the screw.
Brocken drills, first pre-sharpen till they are flat.
Содержание BSG 60
Страница 3: ......