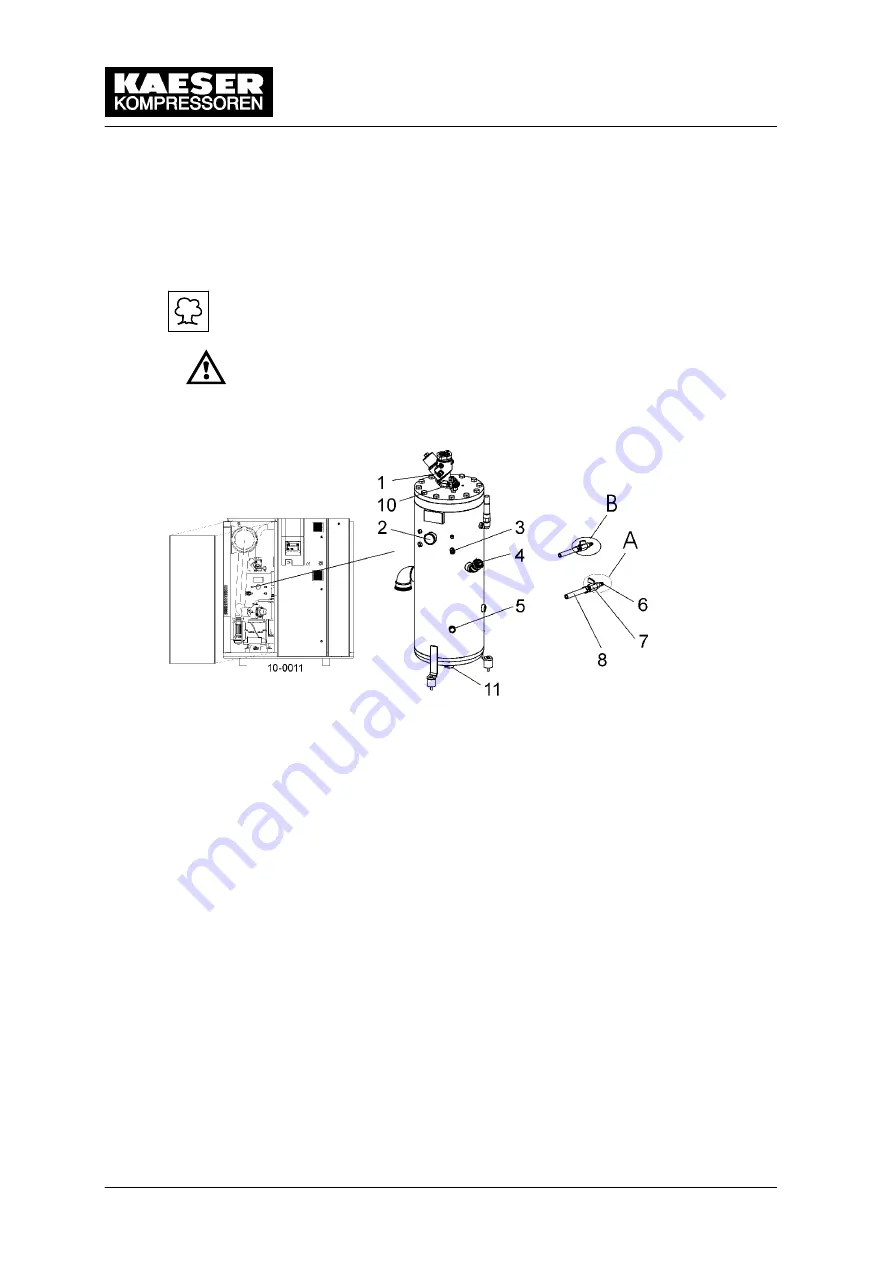
Maintenance
10 --- 60
10.11
Changing the Cooling Oil
Material:
Cooling oil
Have the oil container ready.
Thoroughly drain the oil from the separator tank, the cooler and the heat recovery system if
fitted.
Dispose of the old oil in accordance with local environment protection
regulations.
Danger of burning from hot components and oil.
Wear long ---arm clothing and gloves.
Work carefully.
Fig. 26
Changing the Cooling Oil, Oil Separator Tank
1
Hose coupling (air cooler venting)
6
Male hose coupling/fitting
2
Pressure gauge
7
Shut ---off valve
A: closed
B: open
3
Hose coupling (oil separator tank ven-
ting)
8
Maintenance hose
4
Oil filling port with plug
9
Hose coupling (oil drain)
5
Oil level indicator
10
Shut ---off valve (venting line)
11
Shut ---off valve (oil drain)
Compressed air helps to expel the oil.
This pressure can be generated by the machine itself.
Alternatively, an external source of compressed can be used.
External air is necessary when:
the machine is not operational
the machine is to be restarted after a long standstill period.
Oil changing with help from internal pressure
Pre --- condition: Machine has been running at least five minutes under LOAD.
Machine is switched off.
Machine fully vented (no pressure).
Pressure gauge on the oil separator tank indicates zero.
CAUTION
Содержание CSD 82
Страница 2: ......
Страница 77: ......
Страница 78: ......
Страница 79: ......
Страница 80: ......
Страница 81: ......
Страница 82: ......
Страница 86: ......
Страница 87: ......
Страница 88: ......
Страница 89: ......
Страница 90: ......
Страница 91: ...Appendix 13 83 13 2 2 Pipeline and instrument flow diagram option C1...
Страница 92: ......
Страница 93: ......
Страница 94: ......
Страница 95: ......
Страница 96: ......
Страница 97: ...Appendix 13 89 13 2 3 Dimensional drawing 13 2 3 1 Air cooling option K1...
Страница 98: ......
Страница 99: ......
Страница 100: ...Appendix 13 92 13 2 3 2 Water cooling option K2...
Страница 101: ......
Страница 102: ......
Страница 103: ...Appendix 13 95 13 2 4 Electrical diagram...
Страница 104: ......
Страница 105: ......
Страница 106: ......
Страница 107: ......
Страница 108: ......
Страница 109: ......
Страница 110: ......
Страница 111: ......
Страница 112: ......
Страница 113: ......
Страница 114: ......
Страница 115: ......
Страница 116: ......
Страница 117: ......
Страница 118: ......
Страница 119: ......
Страница 120: ......
Страница 121: ......
Страница 122: ......
Страница 123: ......
Страница 124: ......
Страница 125: ......
Страница 126: ......