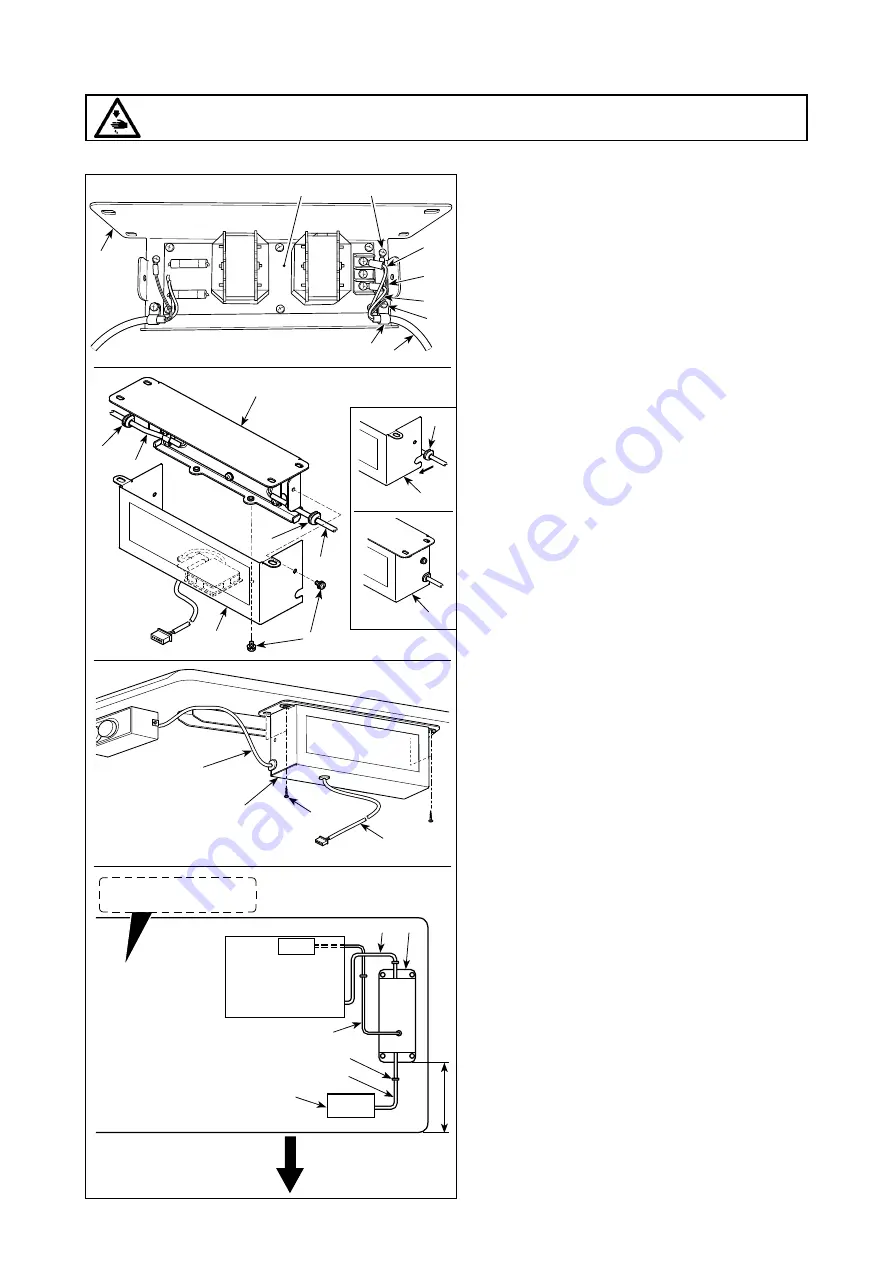
– 2 –
[How to install the reactor box]
WARNING :
Be sure to install the reactor box after turning the power OFF.
* For the EU-type models, install the reactor box that is supplied with the sewing machine.
❽
❸
❶
A
B
C
❷
❹
❻
❺
❼
❽
❽
❶
❾
❸
1) Connect the terminals of power cord
❶
of the
SC-921 to reactor-box PCB asm.
❷
and to
reactor box mounting plate
❸
.
Connect brown wire
A
to the first connector
and blue wire
B
to the third connector respec-
tively from the top of terminal block on the
reactor box PCB asm. using screws. Connect
green/yellow wire
C
to reactor box mounting
plate
❸
with earth setscrew
❹
.
2) Attach cable clip
❺
to the power cord of SC-
921. Attach the power cord together with the
cable clip to reactor box mounting plate
❸
with cable clip setscrew
❻
.
3) Attach cord bushes
❽
to input/output cables
❶
and
❼
of the reactor box.
4) Attach reactor box cover
to reactor box
mounting plate
❸
with four reactor-box cover
setscrews
❾
.
At this time, fix cord bushes
❽
attached to
input/output cables
❶
and
❼
in the concave
section on reactor box cover
to eliminate a
gap between reactor box
and cover
.
5
)
Install reactor box
on the table stand with
four accessory wood screws
at the posi-
tion that is approximately 200 mm away from
the front end of table stand.
Adjust the installing position according to
the size of table stand so that the reactor
box does not protrude from the edge of table
stand.
6) Insert the connector of FAN cord
to CN62
of the SC-921. (Refer to
.)
7) Fix input/output cables
❶
and
❼
of reactor
box
on the table stand using accessory
cord staple
.
At this time, take care not to cross the input-
and output-cables.
Operator's side
Power box
200 mm
❼
SC-921
CN62
❶
Undersurface of table
❼
SC-921 : CN62
←
Содержание SC-921
Страница 1: ...SC 921 INSTRUCTION MANUAL ...