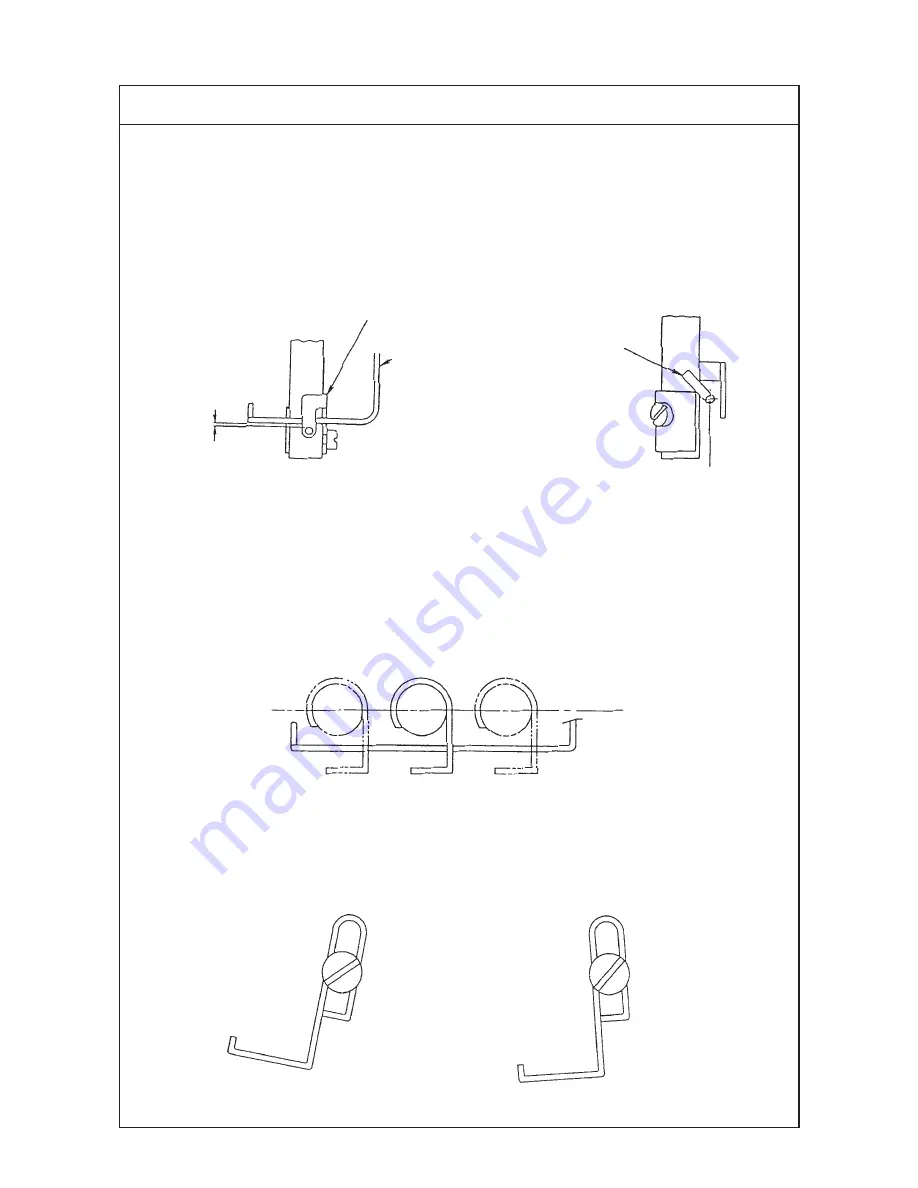
−
22
−
(15) Auxiliary thread take-up lever
Standard Adjustment
™
Vertical position
When the needle bar is in the lowest position of its stroke, the distance from the top end of the
eyelet in the needle bar thread holder to the bottom end of the auxiliary thread take-up lever
should be 0 to 1 mm.
™
Longitudinal position
The auxiliary thread take-up lever, as observed sideways, moves the center of the needle bar and
needle bar thread holder while keeping in parallel to the needle rocking stroke.
0 to 1 mm
Needle bar thread
holder
Auxiliary thread
take-up lever
Auxiliary thread
take-up lever
Center
Needle bar thread holder
In parallel to the needle rocking stroke
Auxiliary thread
take-up lever
Even when the auxiliary thread take-up
lever is positioned with its left-hand side
raised, no problem will result. (
○
)
The position of the auxiliary thread take-up
lever is not acceptable when it is positioned
with its left-hand side lowered. (X)