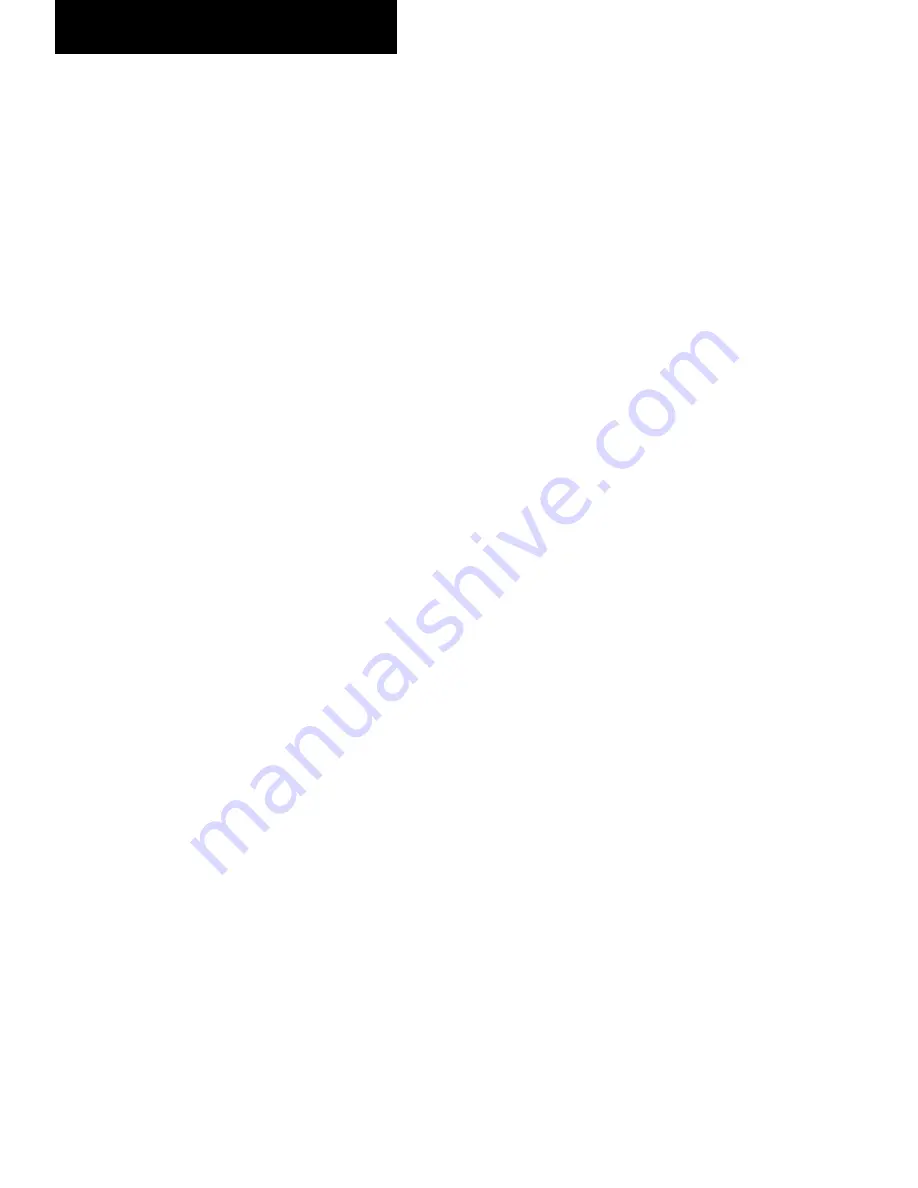
14
JOHNSON CONTROLS
FORM 201.21-NM4 (616)
14
JOHNSON CONTROLS
PRODUCT DESCRIPTION
Motor cooling is provided by suction gas from the
evaporator flowing across the motor. Redundant over
-
load protection is provided using both internal thermistor
and current overload protection on all three phases.
The MTS compressor is lubricated by removing oil from
the refrigerant using an external oil separator. The pres-
surized oil is then cooled in the condenser coils and piped
back to the compressor through a removable 0.005”
mesh screen oil filter to provide compressor lubrication.
The cast iron compressor housing design working pres-
sure is 450 PSIG (31 bar). Each chiller receives a 300
PSIG (21 bar) low side and a 450 PSIG (31 bar) high side
factory test. A 350 Watt (115-1-60 Hz) cartridge heater
is located in the compressor. The heater is temperature
activated to prevent refrigerant condensation.
The following items are also included:
• Acoustically tuned, external discharge muffler to
minimize noise, while optimizing flow for maxi
-
mum performance.
• Discharge shutoff valve.
• Rain-tight terminal box.
• Suction gas screen within the compressor hous
-
ing.
Evaporator
The system uses a high-efficiency Shell and Tube type
Direct Expansion Evaporator. Each of the three or four
refrigerant circuits consists of two (2) passes with the
chilled liquid circulating back and forth across the tubes
from one end to the other.
The design working pressure of the cooler on the shell
side is 150 PSIG (10 bar), and 235 PSIG (16 bar) for
the tube (refrigerant) side. The evaporator is constructed
and tested in accordance with applicable sections of the
ASME Pressure Vessel Code, Section VII, Division (1).
Waterside exempt per paragraph U-1, c, (6).
The water baffles are fabricated from galvanized steel
to resist corrosion. Removable heads are provided for
access to internally enhanced, seamless, copper tubes.
Water vent and drain connections are included.
The cooler is equipped with a thermostatically con-
trolled heater for protection to -20°F (-29°C) ambient
and insulated with 3/4” (19 mm) flexible closed-cell
insulation.
The water nozzles are provided with grooves for
mechanical couplings and should be insulated by the
contractor after pipe installation.
A 300 PSIG (20.7 bar) waterside design working pres-
sure option is available.
3 and 4 compressor chillers utilize a single pass “J”
type evaporator with liquid inlets at one end and suction
outlets at the opposite end. Entering chilled liquid is
split and half flow enters at each end of the evaporator
with leaving chilled liquid exiting in the center of the
evaporator. “J” type evaporators have fewer, longer
tubes than a comparable “E” type. This results in a
smaller diameter, longer shell. Water flow rate internally
in the evaporator is ½ of the total loop flow rate since
the flow is split between two inlets. This results in a
low evaporator water pressure drop.
Condenser
The fin and tube condenser coils are manufactured
from seamless, internally enhanced, high-condensing
coefficient, corrosion-resistant copper tubes arranged
in staggered rows and mechanically expanded into cor-
rosion resistant aluminum alloy fins with full height fin
collars. The condensor has a design working pressure
of 450 PSIG (31 bar).
Multiple, standard low sound, high efficiency, TEAO
motor driven fans move air through the coils. They are
dynamically and statically balanced, direct drive with
corrosion-resistant glass fiber reinforced composite
blades molded into low-noise, full airfoil cross sec-
tions, providing vertical air discharge from extended
orifices for efficiency and low sound. Fans or pairs of
fans are located in a separate compartments separated
by "V" panels to prevent cross flow during fan cycling.
Guards of heavy-gauge, PVC-coated galvanized steel
are provided.
The standard fan motors are high-efficiency, direct drive,
6-pole, 3-phase, Class- “F,” current overload protected,
totally enclosed (TEAO) type with double-sealed, per-
manently lubricated ball bearings.
Содержание York YCAV1039-1909
Страница 43: ...43 JOHNSON CONTROLS FORM 201 21 NM4 616 43 JOHNSON CONTROLS 6 This page intentionally left blank ...
Страница 55: ...55 JOHNSON CONTROLS FORM 201 21 NM4 616 55 JOHNSON CONTROLS 6 This page intentionally left blank ...
Страница 67: ...67 JOHNSON CONTROLS FORM 201 21 NM4 616 67 JOHNSON CONTROLS 6 This page intentionally left blank ...
Страница 83: ...83 JOHNSON CONTROLS FORM 201 21 NM4 616 83 JOHNSON CONTROLS 6 035 20890 009 REV LOCATION LABEL CON T LD11141 ...
Страница 229: ...229 JOHNSON CONTROLS FORM 201 21 NM4 616 229 JOHNSON CONTROLS 8 This page intentionally left blank ...
Страница 249: ...249 JOHNSON CONTROLS FORM 201 21 NM4 616 249 JOHNSON CONTROLS 8 This Page intentionally left blank ...
Страница 277: ...277 JOHNSON CONTROLS FORM 201 21 NM4 616 277 JOHNSON CONTROLS 8 This page intentionally left blank ...
Страница 308: ...308 JOHNSON CONTROLS FORM 201 21 NM4 616 308 JOHNSON CONTROLS MAINTENANCE NOTES ...
Страница 309: ...309 JOHNSON CONTROLS FORM 201 21 NM4 616 309 JOHNSON CONTROLS 9 NOTES ...