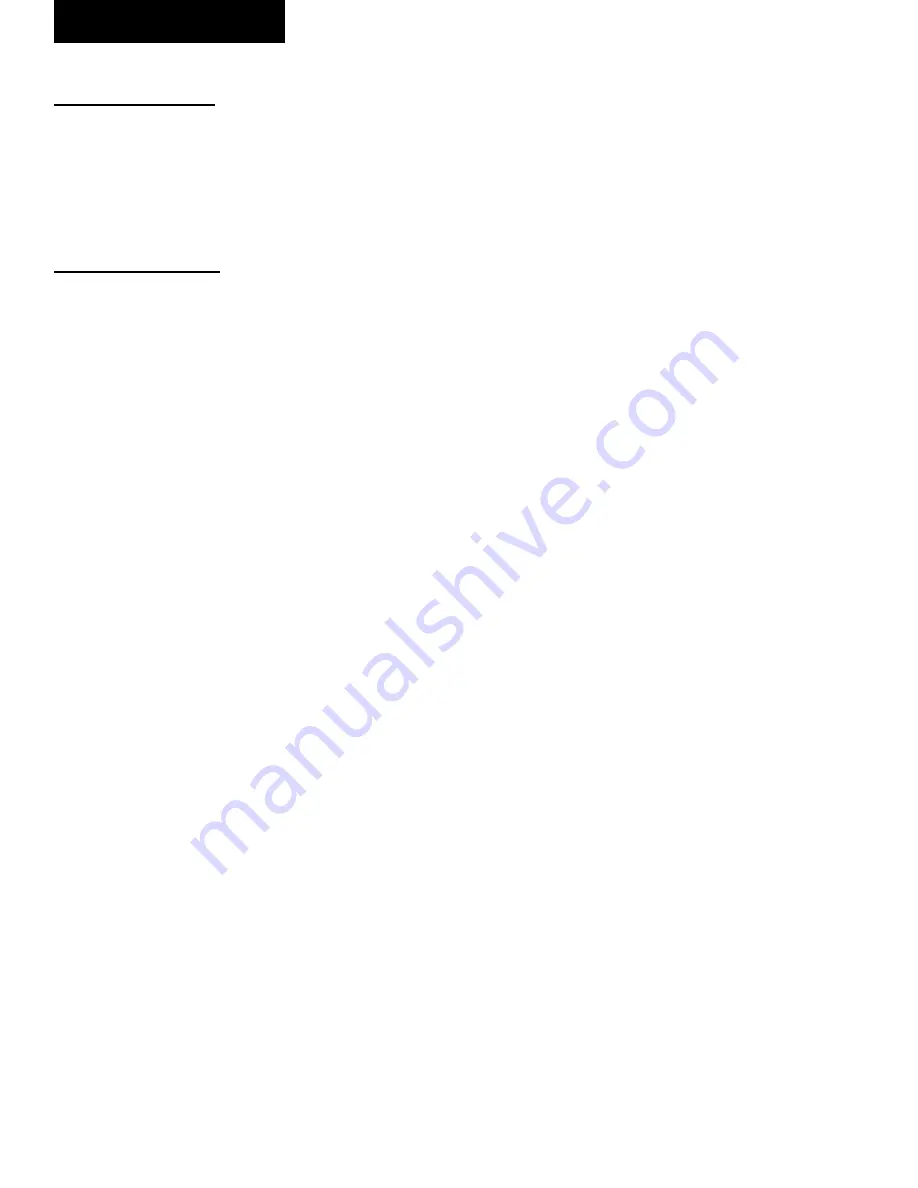
54
JOHNSON CONTROLS
FORM 145.05-NOM1 (708)
Lead Lag Operation
Two Compressor Units
A start output for compressor B will initiate a binary
output at DO-2 – terminals 3 and 4 of the I/O Expansion
Control Board after a one second delay; and a start
output for compressor A will initiate a binary output at
DO-1 – terminals 1 and 2 of the I/O Expansion Control
Board after a one second delay.
Four Compressor Units
During the initial system start up, a start output for
compressor B will initiate a binary output at DO-2
– terminals 3 and 4 of the I/O Expansion Control Board
after a one second delay. A start output for compressor
A will initiate a binary output at DO-1 – terminals 1 and
2 of the I/O Expansion Control Board after a one second
delay. A start output for compressor D will initiate a
binary output at DO-4 – terminals 7 and 8 of the I/O
Expansion Control Board after a one second delay.
A start output for compressor C will initiate a binary
output at DO-3 – terminals 5 and 6 of the I/O Expansion
Control Board after a one second delay.
When the control starts up, compressors B and A are
the lead compressors (compressor B for start output,
compressor B and compressor A for start output
compressor A) and compressors C and D are the lag
compressors (compressor D for start output, compressor
D and compressor C for start output compressor C).
The control records the operating time whenever either
compressor B or A is operating. After 13 hours of run
time the control will switch lead lag operation.
Compressors D and C become the lead compressors
(compressor D for start output compressor B and
compressor C for start output compressor A) and
compressors B and A are the lag compressors (compressor
B for start output compressor C and compressor A for
start output compressor D). The control records the
operating time whenever either compressor D or C is
operating and after 13 hours of operation switch the
lead lag sequence.
FLEXSYS BYPASS DAMPER CONTROL
If the unit is programmed to control the Slab Temperature
in either the DX cooling or economizer mode the unit
will also employ a return air bypass damper. The
purpose of the return air damper is to bypass return air
around the cooling coil in order to temper the supply
air leaving the coil to prevent the supply air entering the
conditioned space from being too cool. The control tries
to maintain the supply air temperature no lower then 2.0°
F below the
“AC / ECON / S/A SP”
set point.
The control also measures the pressure drop across the
evaporator coil. The control will also modulate the by
pass damper to prevent the pressure drop across the
evaporator coil from dropping below the
“MIN DX
PRS DROP”
The following parameters must be programmed through
the
“Setpoints”
section of the Keypad / Display or by
a communicated input.
“MIN DX PRS DROP”
– The control will modulate
the by pass damper to keep the pressure drop across the
evaporator coil above this set point. The default value
is 0.5 inches WC.
“AC-S/A DEW EN”
– This input instructs the control to
use the slab dew point temperature in determining the
DX cooling set point. The default value is ON
Sequence of Operation
The control modulates the by pass damper to keep the
supply air temperature entering the condition space
above the
“AC / ECON / S/A SP”
set point minus 2.0°
F. As the supply air temperature drops below this value
the control will open the damper to by pass additional
return air around the evaporator coil, resulting in an
increase in the supply air temperature. The maximum
allowable damper by pass is 70%.
The control also monitors the pressure drop across
the evaporator coil. This is done to verify that there
is always an adequate amount of return air across the
evaporator coil. As the pressure drop across the coil
decreases below the
“MIN DX PRS DROP”
set point
the control will over ride and close the by pass damper
to maintain adequate airflow across the evaporator coil.
This could result in a temporary decrease in the mixed
supply air temperature.
COMPRESSOR SAFETY CONTROL OPERATION
The unit has the following compressor safety devices
installed:
Compressor High Pressure (Fault / Alarm)
The control monitors the high pressure input from the
discharge pressure transducer for each compressor.
Refer to the
“Faults and Alarms”
section of this manual
for a description of how the control identifies and
responds to a Compressor High Pressure situation.
Sequence of Operation
Содержание York VERSECON YSWD 012
Страница 12: ...12 JOHNSON CONTROLS FORM 145 05 NOM1 708 THIS PAGE INTENTIONALLY LEFT BLANK ...
Страница 58: ...58 JOHNSON CONTROLS FORM 145 05 NOM1 708 THIS PAGE INTENTIONALLY LEFT BLANK ...
Страница 106: ...106 JOHNSON CONTROLS FORM 145 05 NOM1 708 THIS PAGE INTENTIONALLY LEFT BLANK ...
Страница 112: ...112 JOHNSON CONTROLS FORM 145 05 NOM1 708 THIS PAGE INTENTIONALLY LEFT BLANK ...
Страница 125: ...125 JOHNSON CONTROLS FORM 145 05 NOM1 708 FIG 12 ELEMENTARY CONTROL WIRING DIAGRAM YSWU LD13132 CV VAV FlexSys 8 ...
Страница 126: ...126 JOHNSON CONTROLS FORM 145 05 NOM1 708 FIG 13 ELEMENTARY POWER WIRING DIAGRAM YSWU LD13133 CV VAV FlexSys Service ...
Страница 127: ...127 JOHNSON CONTROLS FORM 145 05 NOM1 708 FIG 14 ELEMENTARY CONTROL WIRING DIAGRAM YSWU DOWNFLOW FlexSys LD13142 8 ...