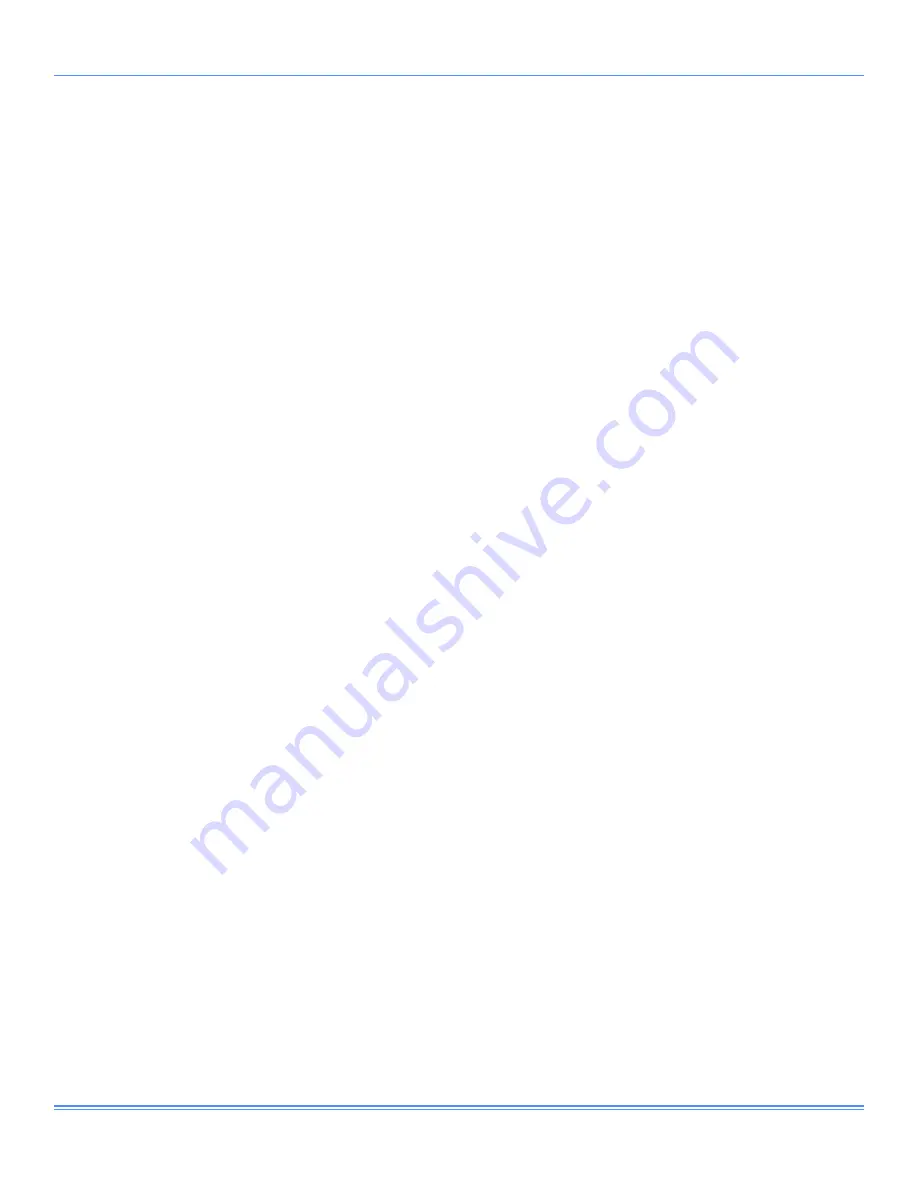
Johnson Controls
5513350-JTG-1018
115
Guide Specifications (Continued)
11.
The wheel drive motor shall be a UL Recognized
Component and shall be mounted in the cassette
frame and supplied with a service connector or junc
-
tion box. Three-phase motors shall be suitable for
use in both standard and inverter rated applications.
12.
The unit shall have 2-inch MERV 8 filters for the out
-
side air and exhaust air to help keep the wheel clean
and reduce maintenance. The ERW shall be ener-
gized briefly for cleaning and blocking protection if it
has not been operated for extended periods.
13. The ERW shall have a bypass damper. The bypass
damper shall be two position (ON/OFF) [modulated]
according to heating/cooling demand.
14. The rooftop unit shall provide frost protection for the
ERW. The controller shall start/stop [vary the speed
of] the wheel to prevent frost condition.
Building Pressure Control
Note:
Select one of the following types of building pressure
control.
1.
No Building Exhaust/Relief -
The unit has no provi-
sions to exhaust building return air.
2.
Barometric Relief Damper -
Building air exhaust
shall be accomplished through barometric relief
dampers installed in the return air (RA) plenum. The
dampers shall open relative to the building pressure.
The opening pressure shall be adjustable.
3.
Powered Exhaust with Modulating DA Damper -
A double width, double inlet (DWDI) forward-curved
centrifugal exhaust fan shall be provided to exhaust
building return air to relieve building static pres-
sure. The fans shall operate at a constant volume
and based on building static pressure. Exhaust air-
flow shall be modulated via a parallel-acting control
damper. The EA dampers shall be sized for 100% of
the exhaust airflow. An access door shall be provided
on at least one side of the unit for fan/motor access.
4.
Powered Exhaust with Variable Frequency Drive
(VFD) -
A DWDI forward-curved centrifugal exhaust
fan shall be provided to exhaust building return air to
relieve building static pressure. Exhaust airflow shall
be modulated via a factory-installed and commis-
sioned variable frequency drive (VFD) with the same
nameplate horsepower as the exhaust fan motor. An
access door shall be provided on at least one side of
the unit for fan/motor access.
5.
Power Return Fan with VFD and Exhaust -
A SWSI
plenum fan shall be provided to draw return air from
the building to the rooftop unit. An access door shall
be provided on at least one side of the unit for fan/
motor access. The return fan shall operate to main-
tain a constant pressure within the RA plenum. An EA
damper shall be provided to modulate building ex-
haust. The damper shall be controlled via building pres-
sure. The RA damper and OA damper shall indepen-
dently modulate volumes of return and outside airflows.
6.
Return [Exhaust] Fan VFD Manual Bypass [Op-
tional] -
A two contactor manual bypass shall be pro
-
vided to permit fan operation in the event of a fan failure.
7.
Return [Exhaust] Fan VFD Reactor [Optional] -
A
3% impedance AC line reactor shall be provided for
return [exhaust] fan VFD.
8.
Airflow Measurement Station [Optional]
shall be
installed on the return fan. Return fan airflow shall be
viewable on the control panel and able to be communi
-
cated across the Building Automation System (BAS).
9.
Belt Guards [Optional]
shall be provided to enclose
the drive and sheave package in return [exhaust] fan.
10.
All VFDs shall be factory tested and matched with
each unit.
For powered exhaust or return fan options above, use the
following:
1.
Exhaust Fan Motor [Return Fan Motor] -
Fan mo-
tors shall be National Electrical Manufacturers Asso-
ciation (NEMA) design ball-bearing types with elec
-
trical characteristics and horsepower as specified.
[Shaft grounding rings on motors shall be provided
to prevent electrical bearing fluting damage by safely
diverting harmful shaft voltages and bearing currents
to ground, increasing the motor longevity.] Motors
shall be nominal 1,800 RPM, open drip-proof (ODP)
type [total enclosed fan-cooled (TEFC) type]. The motor
shall be located within the unit on an adjustable base.
2.
Mountings -
Fan and fan motor shall be internally
mounted and isolated on a full width isolator support
channel using 1-inch [2-inch] springs [and seismic
restraint]. The fan discharge shall be connected to
the fan cabinet using a flexible connection to insure
vibration-free operation.
3.
Bearings and Drives -
Fan bearings shall be self-
aligning, pillow block, or flanged type regreaseable
ball bearings and shall be designed for an average
life L50 of at least 200,000 hours. All bearings shall
be factory lubricated and equipped with standard hy
-