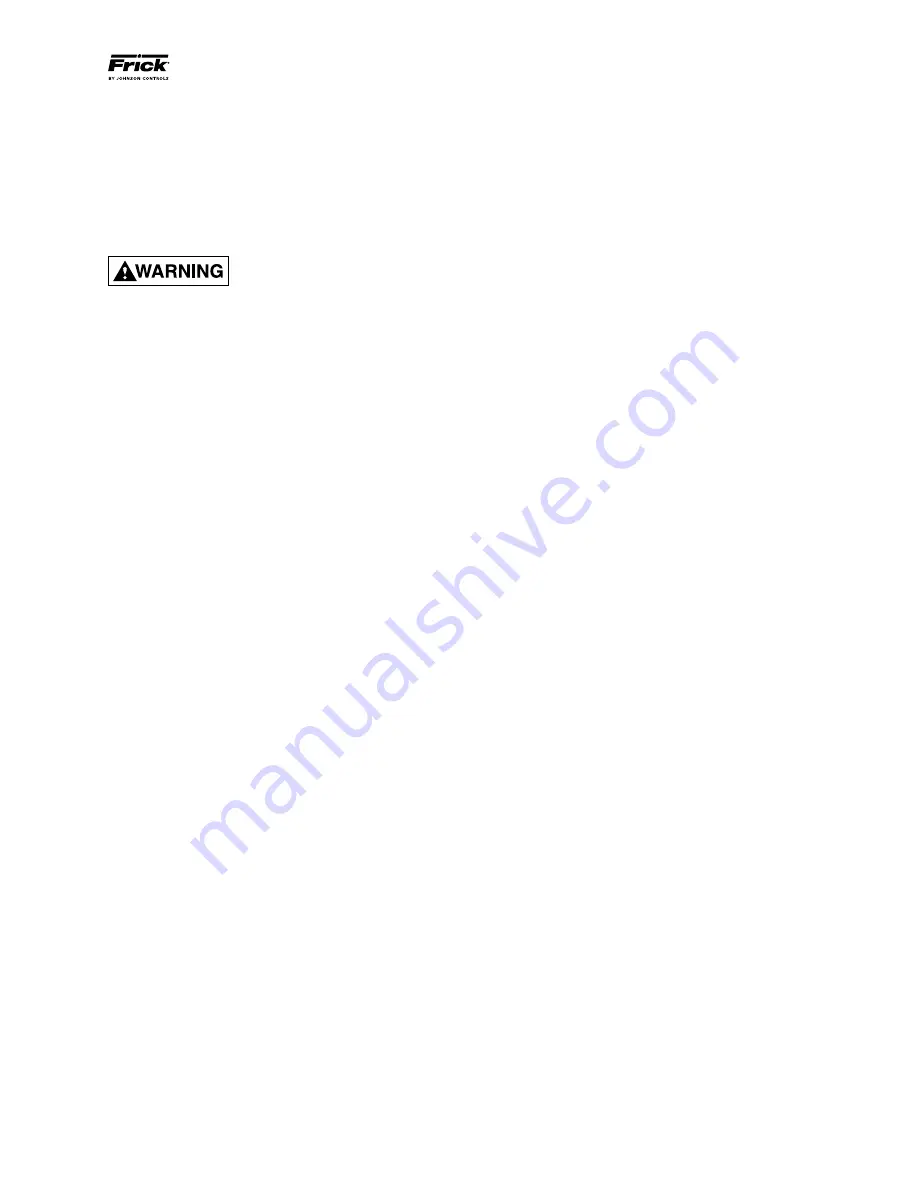
FRICK
®
POWERPAC
™
INSTALLATION
170.600-IOM (JUN 11)
Page 9
HOLDING CHARGE AND STORAGE
Each PowerPac
™
chiller is pressure and leak tested at the
factory and then thoroughly evacuated and charged with dry
nitrogen to ensure the integrity of the unit during shipping
and short term storage prior to installation.
NOTE: Care must be taken when entering the unit to
ensure that the nitrogen charge is safely released.
Holding-charge shipping gauges on
separator and external oil cooler are
rated for 30 PSIG and are for check-
ing the shipping charge only. They must be removed
before pressure testing the system and before charging
the system with refrigerant. Failure to remove these
gauges may result in catastrophic failure of the gauge and
uncontrolled release of refrigerant resulting in serious
injury or death.
All units must be kept in a clean, dry location to prevent
corrosion damage. Reasonable consideration must be given
to proper care for the components of the microprocessor
panel and related instrumentation.
Units which will be stored for more than two months must
have the nitrogen charge checked periodically.
Packaged equipment and all vessels should be visually in-
spected to verify that all components are intact, undamaged
and that the configuration is consistent with the sales order
requirements. Temporary coverings such as tarps or shrink-
wrap should be inspected to ensure that they are not trapping
water in contact with the equipment. Enclosures should be
checked for accumulated water and drained as applicable.
The packaged equipment and all vessels should be visually
inspected for rust, paint fade, paint blisters and surface im-
perfections that may have occurred as a result of handling
and storage damage. The paint may indicate some visual,
not functional, deterioration, especially epoxy paint coatings.
Water spots and chalking are typical flaws of exposed epoxy
(Amerlock 385) paint systems, and some minor rust staining
will occur at locations such as casing splits, flanges, and tags.
We recommend touching-up these areas. Touch-up paint can
be purchased from the Baltimore Parts Center.
Packaged equipment and all vessels are purged and placed
under a regulated dry nitrogen purge pressure of 5 to 15 psig.
Gauges are installed in the appropriate locations to confirm
that the nitrogen pressure is being maintained. Gauges
should be checked every two weeks. If within the first three
months of storage, inspection records indicate a repetitive
loss of nitrogen charge, then the Frick Service department
should be contacted.
To prevent damage to the shaft seals and false brinelling of
the antifriction bearings, the drive shafts for the compressor,
drive motor, oil pump and motor should be rotated every
two weeks. The drive shafts should be rotated 90 degrees
beyond one full rotation.
All drive motors shipped from the factory have prelubricated
bearings to sustain the motor over the short term. Care must
be taken to keep the bearings dry and moisture free. Water
and/or condensation will cause the bearing cages to rust and
cause premature failure.