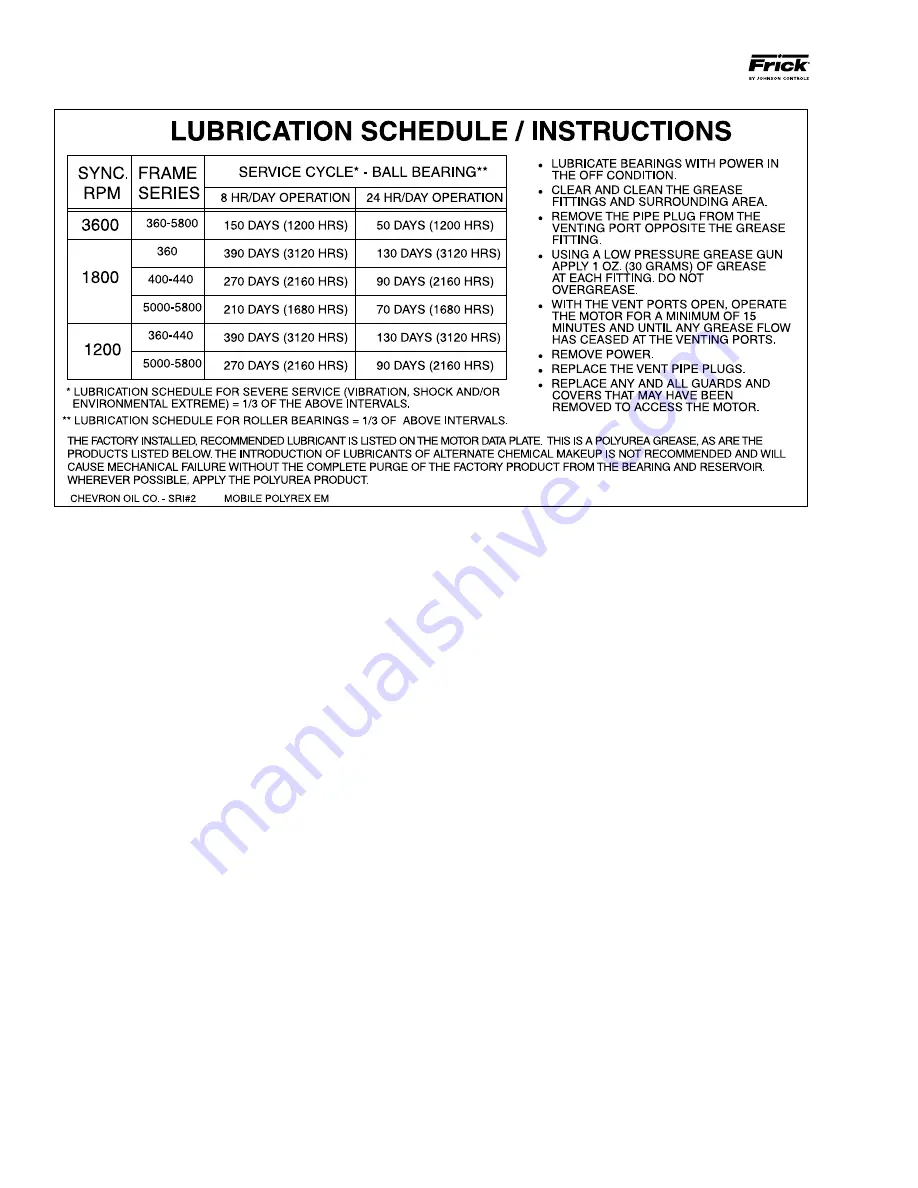
RWH ROTARY SCREW COMPRESSOR UNITS
MAINTENANCE
070.620-IOM (DEC 12)
Page 32
Figure 33 - For Schneider Electric Motors Only. For other manufacturers, follow their schedule.
TROUBLESHOOTING GUIDE
Successful problem solving requires an organized ap proach to
define the problem, identify the cause, and make the proper
correction. Sometimes it is possible that two relatively obvi
ous problems combine to provide a set of symptoms that
can mislead the troubleshooter. Be aware of this possibility
and avoid solving the “wrong problem”.
ABNORMAL OPERATION
ANALYSIS and CORRECTION
Four logical steps are required to analyze an opera tional
problem effectively and make the necessary correc tions:
1.
Define the problem and its limits.
2.
Identify all possible causes.
3.
Test each cause until the source of the problem is found.
4.
Make the necessary corrections.
The first step in effective problem solving is to define the
limits of the problem. If, for example, the compressor pe
riodically experiences high oil tempera tures, do not rely on
this observation alone to help identify the problem. On the
basis of this information the apparent corrective measure
would appear to be a readjustment of the liquid injection
system. Lowering the equalizing pres sure on the thermal
expansion valve would increase the refriger ant feed and the
oil temperature should drop.
If the high oil temperature was the result of high suction
superheat, however, and not just a matter of improper liquid
injection adjustment, increasing the liquid feed could lead
to other problems. Under low load conditions the liquid in
jection system may have a tendency to overfeed. The high
suction superheat condition, moreover, may only be tem
porary. When system conditions return to normal the unit’s
liquid injection will overfeed and oil temperature will drop.
In solving the wrong problem a new problem was created.
When an operating problem develops, compare all operat ing
information on the MAIN OPERATING SCREEN with normal
operating conditions. If an Operating Log has been main
tained the log can help determine what constitutes normal
operation for the compressor unit in that particular system.
The following list of abnormal system conditions can cause
abnormal operation of the RWF II compressor unit:
1.
Insufficient or excessive refrigeration load.
2.
Excessively high suction pressure.
3.
Excessively high suction superheat.
4.
Excessively high discharge pressure.
5.
Inadequate refrigerant charge or low receiver level.
6.
Excessively high or low temperature coolant to the oil
cooler.
7.
Liquid return from system (slugging).
8.
Refrigerant underfeed or overfeed to evaporators.
9.
Blocked tubes in watercooled oil cooler from high min
eral content of water.
10.
Insufficient evaporator or condenser sizing.
11.
Incorrect refrigerant line sizing.
12.
Improper system piping.
13.
Problems in electrical service to compressor unit.
14.
Air and moisture present in the system.
Содержание Frick 1179
Страница 36: ...RWH ROTARY SCREW COMPRESSOR UNITS MAINTENANCE 070 620 IOM DEC 12 Page 36 Figure 37 OIL LEVEL TRANSMITTER ...
Страница 41: ...RWH ROTARY SCREW COMPRESSOR UNITS MAINTENANCE 070 620 IOM DEC 12 Page 41 COMPRESSOR PORT LOCATIONS 408 MM ...
Страница 51: ...RWH ROTARY SCREW COMPRESSOR UNITS MAINTENANCE 070 620 IOM DEC 12 Page 51 OPERATING LOG SHEET ...
Страница 62: ...RWH ROTARY SCREW COMPRESSOR UNITS NOTES 070 620 IOM DEC 12 Page 62 ...
Страница 63: ...RWH ROTARY SCREW COMPRESSOR UNITS NOTES 070 620 IOM DEC 12 Page 63 ...