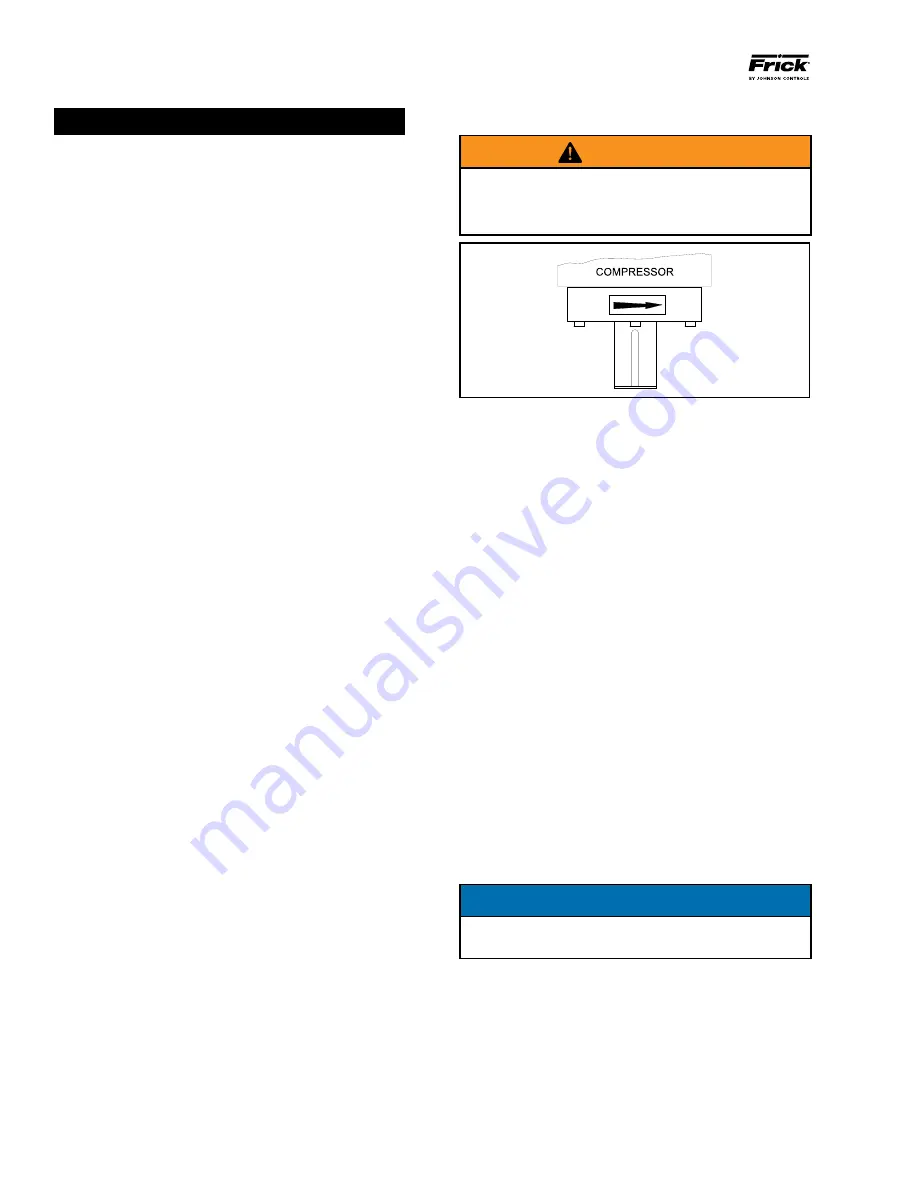
RWH ROTARY SCREW COMPRESSOR UNITS
OPERATION
070.620-IOM (DEC 12)
Page 16
Operation
OPERATION and START-UP INSTRUCTIONS
The Frick
®
RWH Rotary Screw Compressor Unit is an inte
grated system consisting of seven major subsystems:
1. Quantum
™
LX Control Panel
(See publications 090.022O, 090.020M & CS)
2. Compressor
3. Compressor Lubrication System
4. Compressor Oil Separation System
5. Compressor Hydraulic System
6. Compressor Oil Cooling System
7. Compressor EasyStart System
The information in this section of the manual provides the
logical stepbystep instructions to properly start up and
operate the RWH Rotary Screw Compressor Unit.
THE FOLLOWING SUBSECTIONS MUST BE READ AND
UNDERSTOOD BEFORE ATTEMPTING TO START OR OP-
ERATE THE UNIT.
TDSH COMPRESSOR
The Frick
®
RWH rotary screw compressor utilizes mating
asymmetrical profile helical rotors to provide a continuous
flow of refriger ant vapor and is designed for both high
pressure and lowpressure applica tions. The compressor
incorpor ates the following features:
1.
Highcapacity roller bearings to carry radial loads at both
the inlet and outlet ends of the compres sor.
2.
Heavyduty, fourpoint angularcontact ball bearings to
carry axial loads are mounted at the discharge end of com
pressor.
3.
Balance pistons located in the inlet end of the compres sor
to reduce axial loads on the axial load bearings and increase
bearing life.
4.
Movable slide valve to provide fully modulating capacity
control from 100% to approximately 10% of full load capacity.
5.
Volume ratio control to allow infinite ly variable volume
ratio from 2.2 to 5.0 during compres sor operation for all
models. Optional low Vi range is available.
6.
A hydraulic unloader cylinder to operate the slide stop
and slide valve.
7.
Bearing and casing design for 400 PSI discharge pres
sure for cast ductile iron casing 600 PSI for optional steel
casing. This PSI rating applies only to the compressor and
does not reflect the design pressure of the various system
components.
8.
All bearing and control oil vented to closed thread in the
compressor instead of suction port to avoid performance
penalties from superheating suction gas.
9.
Shaft seal design to maintain operating pressure on seal
well below discharge pressure, for increased seal life.
10.
Oil injected into the rotors to maintain good volumetric
and adiabatic efficiency even at very high compression ratios.
11.
Shaft rotation clockwise facing compressor, suitable for
all types of drives.
SEE FOLLOWING WARNING
.
WARNING
Compressor rotation is clockwise when facing the
compressor drive shaft. See Figure 20. The compressor
should never be operated in reverse rotation as bearing
damage will result.
Figure 20 - Shaft Rotation Direction
12.
Dual compressor casing design for very low airborne noise
transmission.
13.
Suction flange is 300 psig ANSI type (except RWH 852 is
CL 400 PLC).
COMPRESSOR LUBRICATION SYSTEM
The lubrication system on an RWH screw com pres sor unit
performs several functions:
1.
Provides lubrication to bearings and seal.
2.
Provides a cushion between the rotors to minimize noise
and vibrations.
3.
Helps keep the compressor cool and prevents overheat ing.
4.
Provides an oil supply to hydraulically actuate the slide
valve and slide stop.
5.
Provides oil pressure to the balance pistons to help in
crease bearing life.
6.
Provides an oil seal between the rotors to prevent rotor
contact or gas bypassing.
The compressor unit is equipped with either a full lube oil
pump or a prelube/control oil pump lubrication system.
Additionally, either system may contain dual oil filters and
liquid injection, watercooled, or thermosyphon oil cooler
for compressor oil cooling.
NOTICE
For alarm descriptions and shutdown or cutout param-
eters, see publication 090.022-O.
CONTROL PUMP OIL SYSTEM
The control oil pump is required to facilitate proper capac
ity control operation of the slide valve. It maintains control
(solenoid)oil pressure 30 to 50 PSI above discharge pressure.
It runs continuously and stops at time of shutdown. The
control oil pump works in conjunction with the discharge
butterfly valve control. System pressure differential provides
for lubrication and cooling oil flow.
Содержание Frick 1179
Страница 36: ...RWH ROTARY SCREW COMPRESSOR UNITS MAINTENANCE 070 620 IOM DEC 12 Page 36 Figure 37 OIL LEVEL TRANSMITTER ...
Страница 41: ...RWH ROTARY SCREW COMPRESSOR UNITS MAINTENANCE 070 620 IOM DEC 12 Page 41 COMPRESSOR PORT LOCATIONS 408 MM ...
Страница 51: ...RWH ROTARY SCREW COMPRESSOR UNITS MAINTENANCE 070 620 IOM DEC 12 Page 51 OPERATING LOG SHEET ...
Страница 62: ...RWH ROTARY SCREW COMPRESSOR UNITS NOTES 070 620 IOM DEC 12 Page 62 ...
Страница 63: ...RWH ROTARY SCREW COMPRESSOR UNITS NOTES 070 620 IOM DEC 12 Page 63 ...