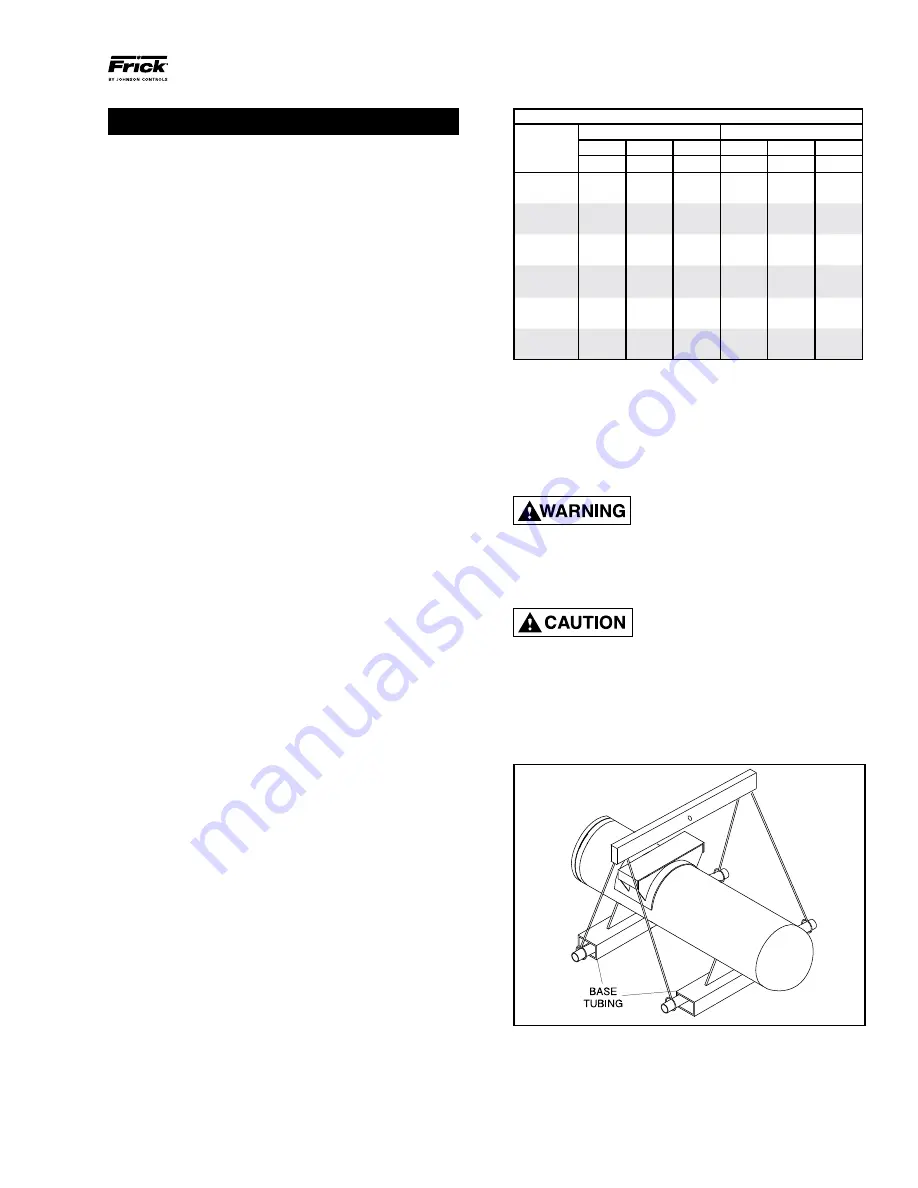
RXF ROTARY SCREW COMPRESSOR UNITS
INSTALLATION
070.410-IOM (JAN 12)
Page 5
Installation
FOUNDATION
NOTE: Allow space for servicing both ends of the unit. A
minimum of 24 inches is recommended.
The first requirement of the compressor foundation is that
it must be able to support the weight of the compressor
package including coolers, oil, and refrigerant charge. Screw
compressors are capable of converting large quantities of
shaft power into gas compression in a relatively small space
and a mass is required to effectively dampen these relatively
high frequency vibrations.
Firmly anchoring the compressor package to a suitable
foundation by proper application of grout and elimination of
piping stress imposed on the compressor is the best insur-
ance for a trouble free installation. Use only the certified
general arrangement drawings from Frick
®
to determine the
mounting foot locations and to allow for recommended clear-
ances around the unit for ease of operation and servicing.
Foundations must be in compliance with local building codes
and materials should be of industrial quality.
The floor shall be a minimum of 6 inches of reinforced con-
crete and housekeeping pads are recommended. Anchor
bolts are required to firmly tie the unit to the floor. Once the
unit is rigged into place (See
HANDLING and MOVING
), the
feet must then be shimmed in order to level the unit. The
shims should be placed to position the feet roughly one inch
above the housekeeping pad to allow room for grouting. An
expansion-type epoxy grout must be worked under all areas
of the base with no voids and be allowed to settle with a
slight outward slope so oil and water can run off of the base.
When installing on a steel base, the following guidelines
should be implemented to properly design the system base:
1. Use I-beams in the skid where the screw compressor will
be attached to the system base. They shall run parallel to
the package feet and support the feet for their full length.
2. The compressor unit feet shall be continuously welded to
the system base at all points of contact.
3. The compressor unit shall not be mounted on vibration
isolators in order to hold down package vibration levels.
4. The customer’s foundation for the system base shall fully
support the system base under all areas, but most certainly
under the I-beams that support the compressor package.
When installing on the upper floors of buildings, extra precau-
tions should be taken to prevent normal package vibration
from being transferred to the building structure. It may be
necessary to use rubber or spring isolators, or a combination
of both, to prevent the transmission of compressor vibration
directly to the structure. However, this may increase package
vibration levels because the compressor is not in contact with
any damping mass. The mounting and support of suction
and discharge lines is also very important. Rubber or spring
pipe supports may be required to avoid exciting the build-
ing structure at any pipe supports close to the compressor
package. It is best to employ a vibration expert in the design
of a proper mounting arrangement.
In any screw compressor installation, suction and discharge
lines shall be supported in pipe hangers (preferably within
2 feet of vertical pipe run) so that the lines won’t move if
disconnected from the compressor. See table for Allowable
Flange Loads.
ALLOWABLE fLANGE LOADS
NOZ.
MOMENTS (ft-lbf)
LOAD (lbf)
SIZE
AXIAL VERT.
LAT. AXIAL VERT.
LAT.
NpS
M
R
M
C
M
L
p
V
C
V
L
1
25
25
25
50
50
50
1.25
25
25
25
50
50
50
1.5
50
40
40
100
75
75
2
100
70
70
150
125
125
3
250
175
175
225
250
250
4
400
200
200
300
400
400
5
425
400
400
400
450
450
6
1,000
750
750
650
650
650
8
1,500 1,000 1,000 1,500
900
900
10
1,500 1,200 1,200 1,500 1,200 1,200
12
1,500 1,500 1,500 1,500 1,500 1,500
14
2,000 1,800 1,800 1,700 2,000 2,000
Proper foundations and proper installation methods are vital;
and even then, sound attenuation or noise curtains may be
required to reduce noise to desired levels.
For more detailed information on Screw Compressor Founda-
tions, please request Frick publication S70-210 IB.
HANDLING and MOVING
This screw compressor package may
be top-heavy. Use caution in rigging
and handling.
RXF 12–50 units can be moved with a forklift or with rigging
and a crane. The recommended method is to insert lengths
of 2" pipe through the base tubing (see Figure 1 below).
Spreader bars should be used on
both the length and width of the
package to prevent bending oil lines
and damage to the package. CAUTION must also be used
in locating the lifting ring. Appropriate adjust ment in the
lifting point should be made to compensate for motor
weight. Adjustment of the lifting point must also be made
for any additions to the standard package such as an
external oil cooler, etc., as the center of balance will be
effected.
Figure 1 - RXF 12 – 50
The unit can be moved with a forklift by forking through
the base tubing.
NEVER MOVE THE UNIT BY PUSHING
OR FORKING AGAINST THE SEPARATOR SHELL OR ITS
MOUNT ING SUPPORTS.