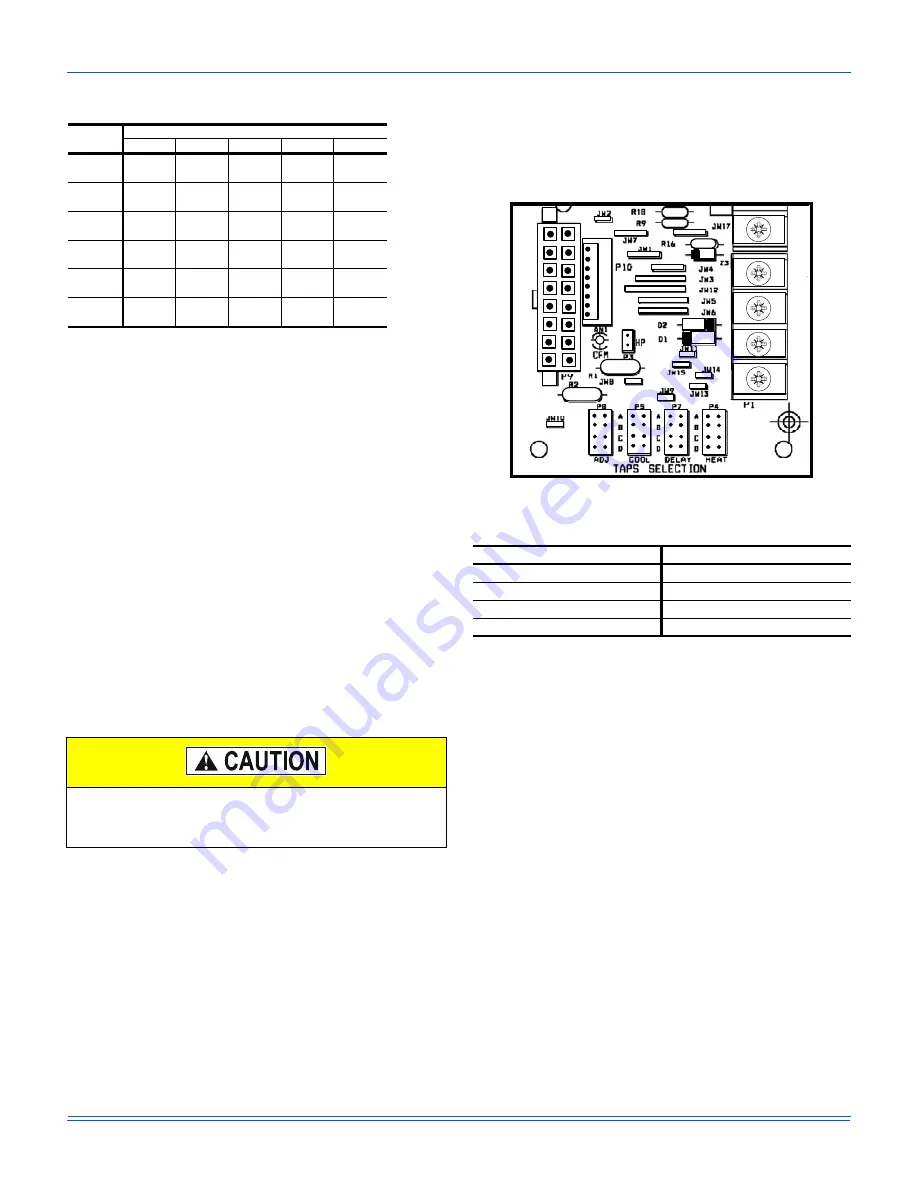
437758-YIM-A-0409
Johnson Controls Unitary Products
25
Blower Speed Selection
The variable speed blowers are designed to deliver constant
CFM regardless of the external static pressure (ESP) in the
ductwork. Therefore, if too many supply registers are closed, a
filter becomes clogged, or there is a restriction in the ductwork,
the motor will automatically operate at a higher speed to
compensate for the higher ESP. This may result in a higher
operating sound level.
These units have variable speed motors that automatically adjust
to provide constant CFM from 0.2" to 0.6" w.c. static pressure.
From 0.6" to 1.0" static pressure, CFM is reduced by 2% per 0.1"
increase in static. Operation on duct systems with greater than
1.0" w.c. external static pressure is not recommended.
To Set Cooling CFM for DNQ Units:
Refer to Airflow Performance Tables 15 and 16 for the possible
cooling speed CFM selections.
Set “COOL” and “ADJ” Jumpers on the CFM selection board as
indicated in Tables 15, 16 and Figure 13.
NOTE:
CFM indicator light flashes once for every 100 CFM
(i.e. 12 flashes = 1200 CFM).
To Set Delay Profile:
Every unit has multiple cooling “blower off delay” profiles to
optimize system performance and efficiency. Refer to Table 19
for the regional climate in your area. Place the “DELAY” jumper
tap on the CFM selection board on the appropriate pin setting.
Factory Set Gas Heat CFM:
The blower speed required for gas heat is different than for
cooling. The heating CFM is factory set, but is adjustable.
The “Heat” Jumper on the CFM selection board should be
set to “A” from the factory.
Fan Only CFM:
When the connection is made from “R” to “G”, the fan only
mode is activated. In this mode, the blower will deliver 75% of
the cooling system CFM. This connection is factory set from the
manufacturer, but can be field adjusted.
Figure 13: Control Board Speed Tap Location
Operation
The unit is controlled by a conventional heating/cooling
thermostat common to this class of equipment.
Heating Sequence Of Operation
Heat
The control board begins a call for heat when W1 is energized
(connected to R). The control ignores W2 until pilot ignition has
been established.
The control checks to see if the pressure switch is open. If the
pressure switch is closed, the control board flashes “3” on the LED
and waits indefinitely for it to open. When the pressure switch is
sensed as open, the control begins pressure switch proving
period. If the call for heat is lost, the control goes back to Standby.
Pressure Switch Proving
The control board energizes the induced draft motor (High speed
for 2 stage model) and waits for the low pressure switch to close.
When the low pressure switch closes, the control begins Pre-
purge period. If the call for heat is lost, the control de-energizes
the inducer without post-purge and returns to standby.
Table 18: Indoor Blower Specifications
Size
(Tons)
Motor
HP
RPM
Eff.
SF
Frame
024
(2.0)
1/2
1050
0.8
1.0
48
030
(2.5)
3/4
1050
0.8
1.0
48
036
(3.0)
3/4
1050
0.8
1.0
48
042
(3.5)
3/4
1050
0.8
1.0
48
048
(4.0)
1
1050
0.8
1.0
48
060
(5.0)
1
1050
0.8
1.0
48
Do not change the “ADJ” tab position on the CFM
selection board as this will change your cooling CFM
previously selected.
Table 19: Delay Profile
Delay Tap
Regional Climate Type
Jumper at “A”
Standard Setting
Jumper at “B”
Humid Climate
Jumper at “C”
Dry Climate
Jumper at “D”
Temperate Climate
W2
W1
R
Y1
Y/Y2