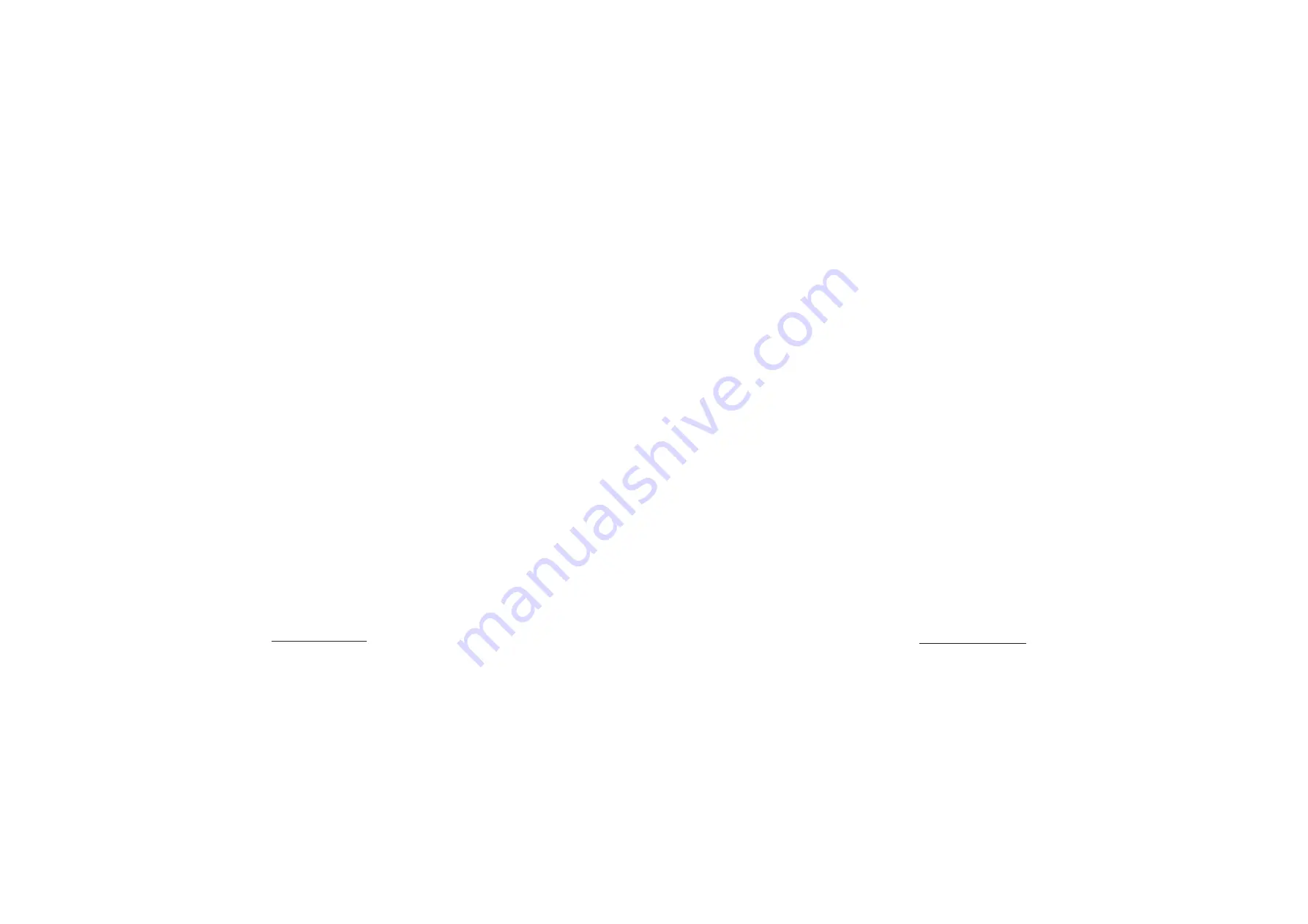
ZZ757/9
5
6.3
CONDENSATE
6.3.1
When firing at low rate, the unit will produce condensate which must be drained away. A JDT1 kit, which
externally drains the condensate away from the flue terminal is available for horizontal flued applications. Vertical
flued applications require the fitment of an in-line condensate trap within 0.5 m of the unit, in the first vertical
flue run, and before any bends in the flue run. Such a trap, with a 32 mm male drainage connection, is available for
this purpose.
6.3.2
Condensate from vertical flued applications must be drained away using 32 mm or 20 mm internal diameter, rigid
plastic pipe, connected to the condensate drain using KUTERLITE 700 or similar straight coupling. The pipe
should be installed in such a manner, that it forms a continuous downward slope away from the unit at a minimum
3
o
angle (6 mm per 100 mm, or, 0.75 in per foot run), and that the risk of mechanical damage and interior
interference is minimised. The pipe is to be protected against frost damage.
6.4
ELECTRICAL
6.4.1
Mains:
The heater is supplied with mains cable (PVC sheathed, high temperature resistant, 3 core [Brown-
Blue-Green/Yellow], 6A, 0.75mm
2
), connected to a terminal block and exiting from the heater at the bottom right
hand rear. The cable is suitable for a 230V 50Hz single phase supply and must be protected by a 5A fuse, and an
earth wire must be connected. A double pole switch or fused spur box should also be used. All wiring conform to
I.E.E. regulations, (current edition).
6.4.2
Thermista-stat:
A Thermista-stat is provided with the appliance; this acts as a room thermostat, and also as a
summer air flow switch. The Thermista-stat wiring is to be connected to terminals 3 and 4 on the air heater
control panel, (marked ‘THERMISTA-STAT’), polarity being unimportant. It should be located where there is free
air circulation, and approximately 1.5m (5ft) from the floor. The following locations should be avoided.
a.
In a room where temperature is greatly affected by the sun or any other heat source (e.g. radiant fire, wall
light fitting or TV set).
b.
Near an outside door or windows, or on an outside wall.
c.
Where it can be affected by warm air ducts, diffusers, waste pipes or the heater itself.
d.
Where it can be subject to vibration.
6.4.3
Time Control:
If an external time control (not supplied) is to be fitted, connect the live supply to terminal 7,
the neutral to terminal 6, and the time-switch output to terminal 5. If no time control is fitted, link terminal 5
and 7.
6.5
GAS (see BS 5864 and BS 6891)
6.5.1
An independent gas supply pipe from the gas meter is to be preferred wherever possible. However, when this is
not possible, the pipe must be capable of taking the complete input of the heater and all other gas appliances being
served by this same pipe. This supply should be suitably sized to conform to British Standards requirements of no
more than 1.0 mbar (0.4 in. wg.) pressure drop (see table of discharge in BS 6891).
6.5.2
The
1
/
2
in union gas cock (supplied) must be fitted externally in the gas inlet of the heater for easy isolation during
servicing. The gas pipe should be fitted and installed as to be durable, substantial and gas tight. Gas entry to the air
heater may be through the left hand side, right hand side front, or rear, to an Rc
1
/
2
(
1
/
2
in B.S.P. internal (taper)
thread).
7.
COMMISSIONING
7.1
Ensure the following:
7.1.1
Gas and Electrical supplies are
OFF.
7.1.2
Filter, fan and fan compartments are free from obstructions.
7.1.3
All registers or grilles are open and conform to design specifications.
7.1.4
Return, relief and ventilation air installations are adequate.
7.1.5
Adhesive label is removed from the centre of the combustion air fan to expose the motor cooling slots.
7.2
Turn ON the gas supply to the heater.
7.3
Test for gas soundness at supply, Multifunctional control, Pilot and Main burners using proprietary detection fluid,
sealing any leaks found, and purge the whole gas pipe as described in BS 6891.
7.4
Set the Thermista-stat to maximum setting (9).
7.5
Ensure that the remote time control (if fitted) is in the
ON
mode.
7.6
Switch on the electrical supply to the heater. The combustion air fan will start up immediately; after a minimum of 30
seconds, the burner will automatically ignite and the green ‘
BURNER ON
’ indicator will illuminate.
ZZ757/9
10
9.13
FAN DELAY/OVERHEAT (LIMIT) CONTROL (FDC) REMOVAL:
9.13.1 Ensure that the electrical supply is switched off.
9.13.2 Remove the heater front cover.
9.13.3 Remove the 2 x screws securing the heater front door, and open front door.
9.13.4 Disconnect the five conductors in the FDC lead from the control panel terminal strip, having first noted their
positions.
9.13.5 Release 2 x screws securing FDC to the bulkhead, and withdraw the FDC from the heater.
9.13.6 Refitting or replacement is in reverse order.
9.14
OVERHEAT CUTOUT (THERMAL SWITCH) REMOVAL:
9.14.1 Ensure that the electrical supply is switched off.
9.14.2 Remove the heater front cover.
9.14.3 Remove the 2 x screws securing the heater front door, and open front door.
9.14.4 Disconnect the two conductors from the thermal switch.
9.14.5 Release the two securing screws and withdraw the switch.
9.14.6 Refitting or replacement is in reverse order.
9.15
MAINS FILTER REMOVAL:
9.14.1 Ensure that the electrical supply is switched off.
9.14.2 Remove the heater front cover.
9.14.3 Remove the 2 x screws securing the heater front door, and open front door.
9.14.4 Disconnect the two conductors from the thermal switch.
9.14.5 Release the two securing screws and withdraw the switch.
9.14.6 Refitting or replacement is in reverse order.
9.16
HEAT EXCHANGER REMOVAL:
9.15.1 Referring to 9.3, remove the burner assembly.
9.15.2 Referring to 9.9, remove the Ignition/detection electrode.
9.15.3 Referring to 9.12, remove the combustion air fan, including complete removal of the two upper securing screws.
9.15.4 Referring to 9.13, remove the fan delay/overheat (limit) control.
9.15.6 Disconnect the base plenum from its associated duct work, and remove it form the appliance by releasing the two
screws from inside the plenum, and one hexagonal screw from the appliance floor.
9.15.7 Release the two hexagonal screws securing the heat exchanger at the burner aperture, and withdraw the heat
exchanger from the appliance through the base aperture.
9.15.8 Refitting or replacement is in reverse order, ensuring that the two upper combustion fan securing screws are fitted
before fully tightening the heat exchanger securing screws at the burner aperture.
10.
DEFECT DIAGNOSIS
10.1
IMPORTANT: If an electrical fault occurs after installation of the appliance, preliminary earth continuity,
polarity and resistance to earth checks should be carried out with a multimeter. On completion of any service/
defect rectification tasks which have required the breaking and remaking of electrical connections, then
continuity, polarity and resistance to earth checks should be repeated.
10.2
Note:
When purging or checking gas supplies, ensure that there is adequate ventilation to the room or cupboard, and all
naked lights are extinguished.
10.3
Care must be taken during replacement and handling of electronic assemblies, i.e. printed circuit board module,
fan delay/overheat (limit) control and Thermista-stat. It is not practical to rectify defects in these assemblies
except in the factory, and any attempt to do so may render any guarantee or factory replacement arrangement
invalid.