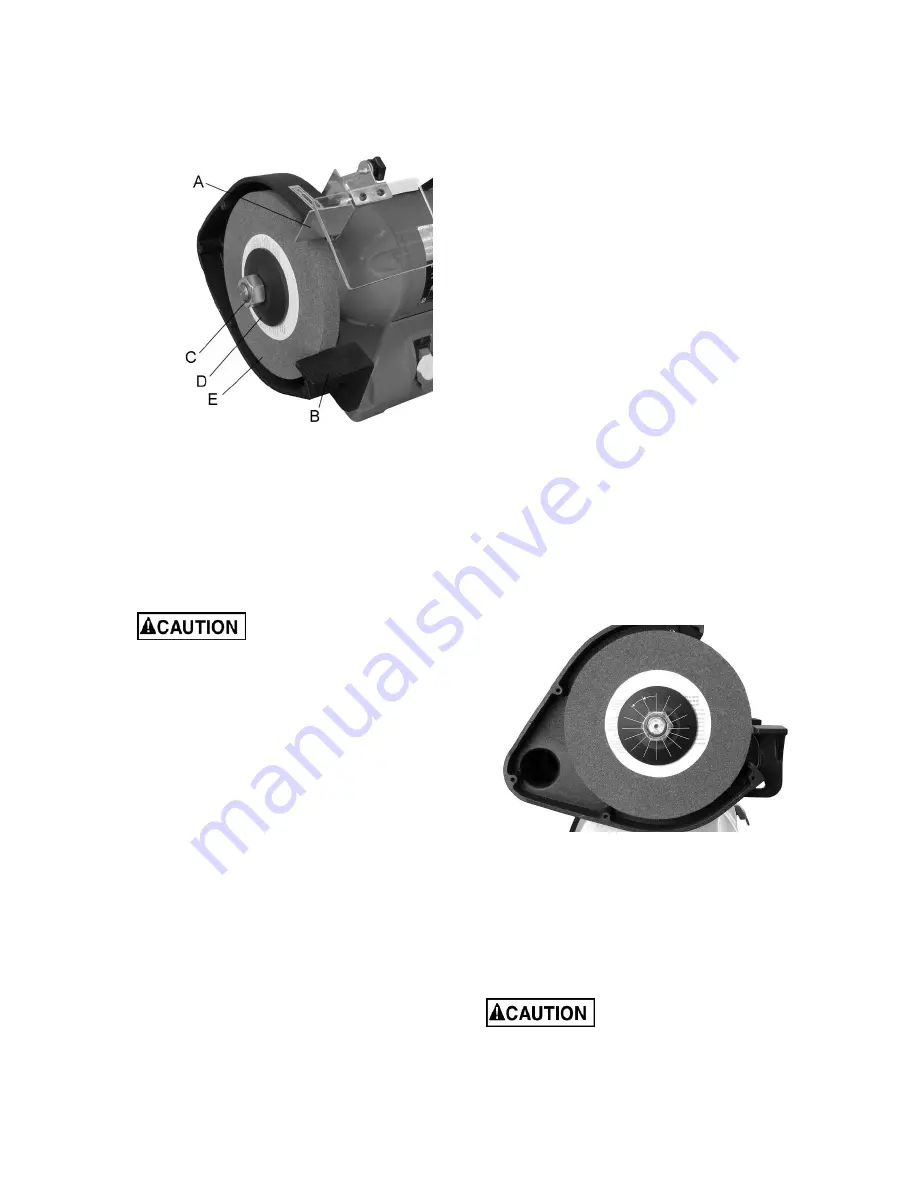
14
5. Unscrew arbor nut (C) with wrench.
NOTE
:
Left-hand threads; turn nut
clockwise
to
loosen.
6. Remove outer flange (D), wheel (E), and inner
flange.
Figure 9-1: wheel replacement
7. Clean flanges. Check the flanges to make sure
they are flat. Wheel flanges that are not flat will
cause the wheel to wobble.
8. Inspect the new grinding wheel and perform a
“ring test” (
sect. 9.1
). Do not install a damaged
wheel.
9. Install inner flange, wheel (E), outer flange (D)
and nut (C) on the shaft. Tighten nut.
Do not overtighten nut;
this may cause wheel to crack. Maximum
safe torque on nut is 20 lbf•ft (270 kgf•cm).
10. Reinstall guard cover. Adjust spark guard and
tool rest to 1/16" clearance from wheel.
9.4
Wheel balancing
With the grinder
unplugged from the power
source
, and the arbor nut snugged down, rotate
wheel by hand and observe its motion.
A grinding wheel has proper balance when:
1. The wheel’s outside face spins true and round;
that is, its circumference rotates concentric to
the arbor.
2. There is no side-to-side wobble.
The operator who takes time to patiently perform
needed adjustments will be rewarded by a wheel
running true, and accurate grinding of work pieces.
9.4.1
Adjusting concentricity
If the outside face is not rotating concentric to
arbor, try shifting the wheel closer to arbor
centerline before tightening the nut.
Another method of achieving concentricity is the
use of a wheel dresser. “Dressing” is the removal
of the current layer of abrasive to expose a fresh
surface. A wheel dresser is also used to “true” a
wheel; that is, to make the grinding surface parallel
to the tool rest, so the entire wheel face presents
an even surface to the work piece. Proper use of a
wheel dresser will eliminate high spots and result in
concentric rotation about the arbor, as well as
minimize vibration. See
sect. 9.5
.
9.4.2
Correcting side-to-side wobble
The JIGM Grinder has large, machined flanges,
making wobble unlikely if a good quality grinding
wheel is used. Should a wheel exhibit need for
adjustment:
1. Loosen nut and rotate outer flange a small
amount. Snug the nut and spin the wheel by
hand to check.
2. If wobble still exists, continue repeating step 1,
rotating outer flange incrementally in the same
direction. See Figure 9-2. Make sure to keep
the wheel in same position each time.
3. If complete rotation of outer flange has proved
ineffective, remove nut, outer flange, and
wheel (keep wheel in same orientation by
placing a pencil mark somewhere on it for
reference). Then rotate inner flange about 90°
and repeat the above steps for outer flange.
4.
Continue this combination of flange
movements until the wobble is eliminated.
If required, a shim made of paper or card stock
may be placed between flange and wheel side.
Figure 9-2: wheel balancing
NOTE: Very slight wobble may still exist at spin-up
and spin-down, but will not affect normal speed
operation.
9.5
Dressing the wheel
Below is a general procedure for dressing a
grinding wheel.
Use safety glasses or face
shield during dressing operations.
1. Back off the tool rest enough to allow the
dresser to hook over its inside edge (Figure 9-
3). Tighten tool rest in position.