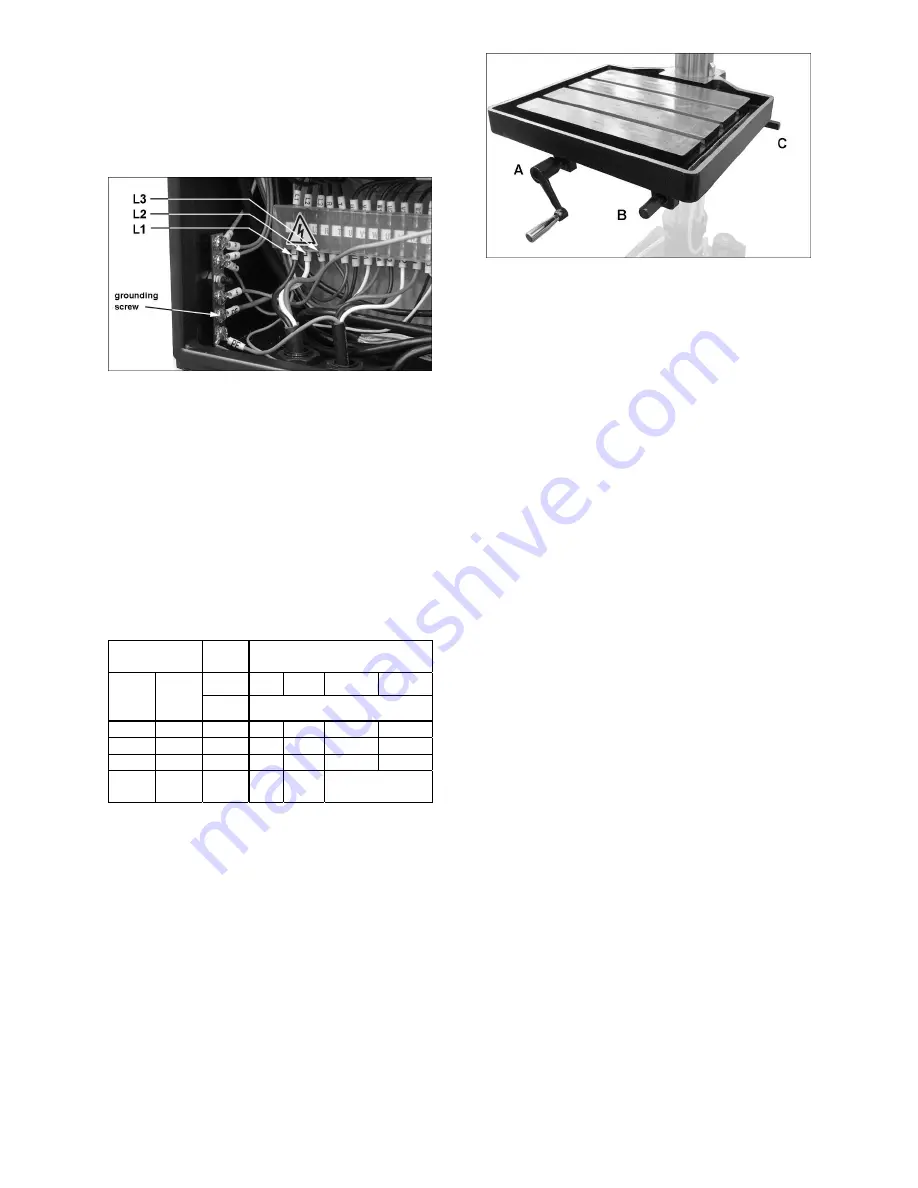
9
Make sure incoming current matches power
requirements of the drill. When machine is
connected properly, spindle turns clockwise in a
conventional drilling rotation. If spindle does not turn
clockwise, disconnect drill from power supply and
reverse any two of the three power leads (except
green ground wire).
Figure 6-1: three-phase connection shown
6.3
Extension cords
The use of extension cords is discouraged; try to
position equipment within reach of the power
source. If an extension cord becomes necessary, be
sure it is heavy enough to carry the current your
product will draw. An undersized cord will cause a
drop in line voltage resulting in loss of power and
overheating.
Table 1 shows recommended size to use depending
on cord length and nameplate ampere rating. If in
doubt, use the next heavier gauge. The smaller the
gauge number, the heavier the cord.
Ampere
Rating
Volts
Total length of
cord in feet
More
Than
Not
More
Than
240 50 100
200 300
AWG
0 6
18
16
16 14
6 10
18
16
14 12
10 12
16
16
14 12
12 16
14
12
Not
Recommended
Table 1: extension cord recommendations
7.0
Adjustments
7.1
Table adjustment
The table can be raised or lowered to accommodate
workpiece height. Place hand crank on shaft (A,
Figure 8-1) and turn counterclockwise to loosen
table lock. Then use hand crank on shaft B or C to
raise or lower table. Lock table in position using
shaft A.
If drill press base is to be used for securing
workpiece, loosen table (A) and swing it around
column and out of the way. Retighten table.
Figure 7-1: table adjustments
7.2
Tool installation and removal
1. Disconnect machine from power source.
2. Thoroughly clean inside of spindle with a soft
dry cloth. Also clean any taper or arbor to be
used in the spindle. If these are not kept clean,
taper or arbor will not “seat” properly in spindle
and may drop out unexpectedly.
3. Place protective piece of scrap wood on table.
4. Raise table to approximately 8-to-10 inches
below spindle.
5. Insert MT-4 tool into spindle.
6. Lower spindle using downfeed handle, and seat
tool against the wood.
7. If installing a drill chuck, retract the jaws then
use rubber mallet (or steel face hammer against
a block of wood) to sharply tap bottom of chuck
two or three times to seat it. NOTE: Never use
a steel face hammer directly against the chuck.
To remove a tool:
1. Disconnect machine from power source.
2. Lower spindle to expose slots in spindle wall.
3. Insert drift key into spindle slots and tap gently
until drill bit or chuck arbor loosens. Hold tool
with one hand (use glove or rag if needed) while
tapping to prevent tool from falling and being
damaged.
7.3
Speed pickup adjustment
Speed pickup has been set correctly by the
manufacturer. If the speed readout display should
lose accuracy, adjustment can be made as follows.
Refer to index numbers on exploded view,
sect.
12.1.1.
1. Loosen screws securing speed pickup (ref. #68)
to plate (#69A).
2. Adjust speed pickup gap to approximately 1/8-
inch. Retighten screws.
3. Operate drill press to verify that speed readout
is operating correctly.
Содержание JDP20EVST-230-PDF
Страница 15: ...15 12 1 1 JDP20EVST 230 460 PDF Top Head Assembly Exploded View ...
Страница 18: ...18 12 2 1 JDP20EVST 230 460 PDF Spindle Components Exploded View ...
Страница 23: ...23 12 4 1 JDP20EVST 230 460 PDF Table and Base Assembly Exploded View ...
Страница 26: ...26 12 5 1 JDP20EVST 230 460 PDF Electrical Cabinet Assembly Exploded View ...
Страница 30: ...30 13 2 JDP20EVST 460 PDF wiring diagram ...
Страница 32: ...32 427 New Sanford Road LaVergne Tennessee 37086 Phone 800 274 6848 www jettools com ...