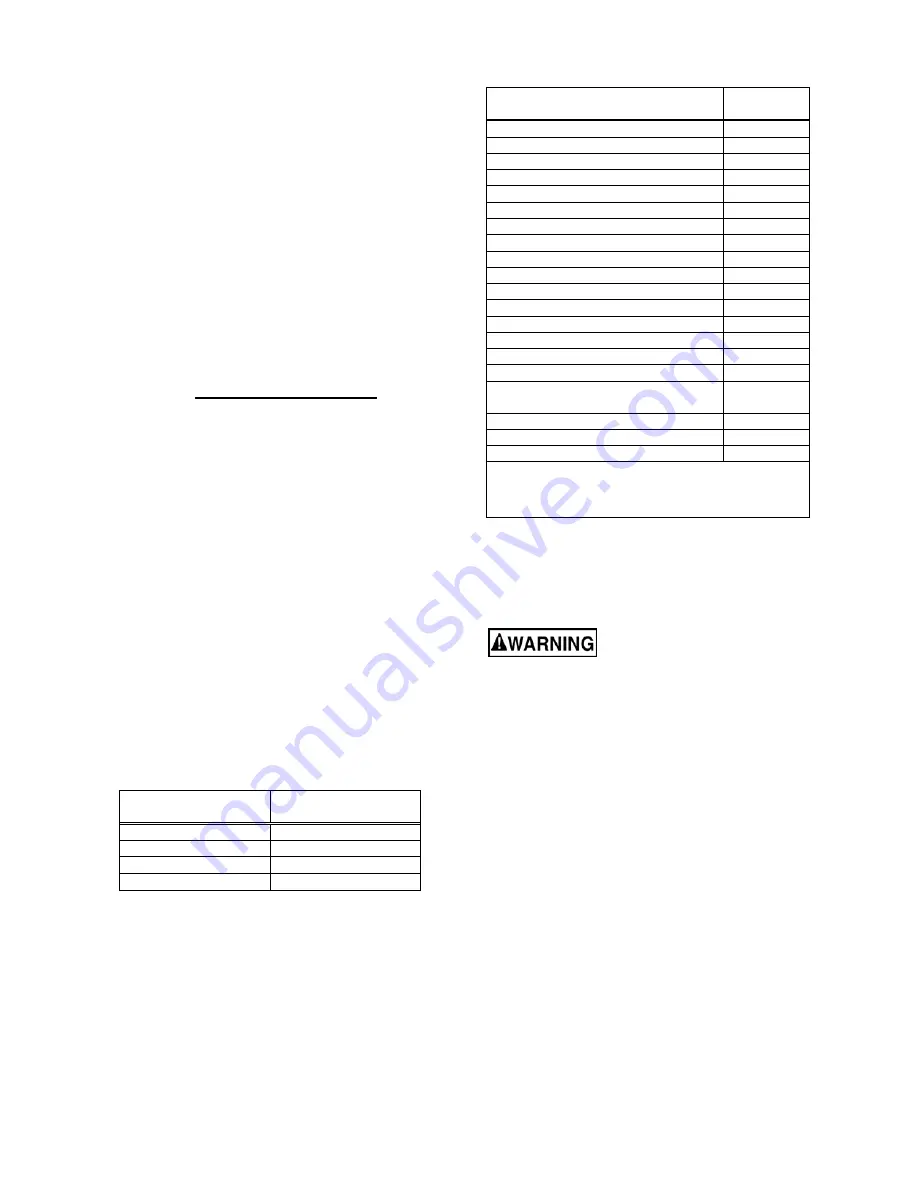
12
5. Pull downfeed handle (J) away from head to
engage powerfeed.
6. When set depth is reached, downfeed handle
will disengage and spindle will retract. Spindle
will continue to rotate.
9.6
Drilling recommendations
9.6.1
Drilling speeds
The speed of a drill is usually measured in terms of
the rate at which the outer periphery of the tool
moves in relation to the work being drilled. The
common term for this is Surface Feet per Minute
(SFM). The relationship of SFM is expressed in the
following formulas:
SFM = 0.26 X rpm X Drill Diameter (in inches)
RPM = 3.8 x ________SFM__________
Drill diameter (in inches)
In general, the higher the speed the shorter the drill
life. Operating at the low end of the speed range for
a particular material will result in longer life. The
most efficient speed for drill operation depends
upon many variables:
1.
Composition and hardness of material.
2.
Depth of hole.
3.
Efficiency of cutting fluid.
4.
Type and condition of drilling machine.
5.
Desired quality of hole.
6.
Difficulty of set-up.
9.6.2
Drilling feed
The feed of a drill is governed by size of tool and the
material drilled. Because feed rate partially
determines rate of production and also is a factor in
tool life, it should be chosen carefully for each job.
In general, the most effective feeds will be found in
the following ranges:
Diameter of Drill
(inches)
Feed per Revolution
(inches)
Under 1/8
0.001 to 0.002
1/8 to 1/4
0.002 to 0.004
1/4 to 1/2
0.004 to 0.007
1/2 to 5/8
0.007 to 0.015
Table 2
9.6.3
Excessive speed/feed indicators
A drill that splits up the web is evidence of too much
feed or insufficient tip clearance at the center as a
result of improper grinding. The rapid wearing away
of the extreme outer corners of cutting edges
indicates that speed is too high. A drill chipping or
breaking out at the cutting edges indicates that
either feed is too heavy or drill has been ground with
too much tip clearance.
9.6.4
Speeds for high speed steel drills
Material
Speed
(SFPM)
Alloy Steel — 300 to 400 Brinell
20-30
Stainless Steel
30-40
Automotive Steel Forgings
40-50
Tool Steel, 1.2C
50-60
Steel, .4C to .5C
70-80
Mild Machinery Steel, .2C to .3C
80-110
Hard Chilled Cast Iron
30-40
Medium Hard Cast Iron
70-100
Soft Cast Iron
100-150
Malleable Iron
80-90
High Nickel Steel or Monel
40-50
High Tensile Bronze
70-150
Ordinary Brass and Bronze
200-300
Aluminum and its Alloys
200-300
Magnesium and its Alloys
250-400
Slate, Marble, and Stone
15-25
Plastics and similar materials
(Bakelite)
100-150
Wood
300-400
Titanium Alloys
10-25
Titanium Alloy Sheet
50–60
Note: In cases where carbon steel drills are applicable, the
drill should be run at speeds of 40 to 50 percent of those
given above.
Table 3
10.0
User-maintenance
10.1
Drive belt replacement
Disconnect electrical power to
drill press to avoid possibility of inadvertent
operation and exposure to potentially lethal
voltage levels.
1. Disconnect machine from power source.
2. Loosen set screw and remove speed range
handle.
3. Remove screws and take off pulley cover.
4. Disconnect electrical wiring from motor junction
box, and remove motor.
5. Remove used belt. Install replacement belt.
6. Install motor and connect electrical wiring (refer
to
sect. 13.0
for wiring details).
7. Install pulley cover and secure with screws.
8. Connect drill press to power and run machine to
verify correct operation.
Содержание JDP20EVST-230-PDF
Страница 15: ...15 12 1 1 JDP20EVST 230 460 PDF Top Head Assembly Exploded View ...
Страница 18: ...18 12 2 1 JDP20EVST 230 460 PDF Spindle Components Exploded View ...
Страница 23: ...23 12 4 1 JDP20EVST 230 460 PDF Table and Base Assembly Exploded View ...
Страница 26: ...26 12 5 1 JDP20EVST 230 460 PDF Electrical Cabinet Assembly Exploded View ...
Страница 30: ...30 13 2 JDP20EVST 460 PDF wiring diagram ...
Страница 32: ...32 427 New Sanford Road LaVergne Tennessee 37086 Phone 800 274 6848 www jettools com ...