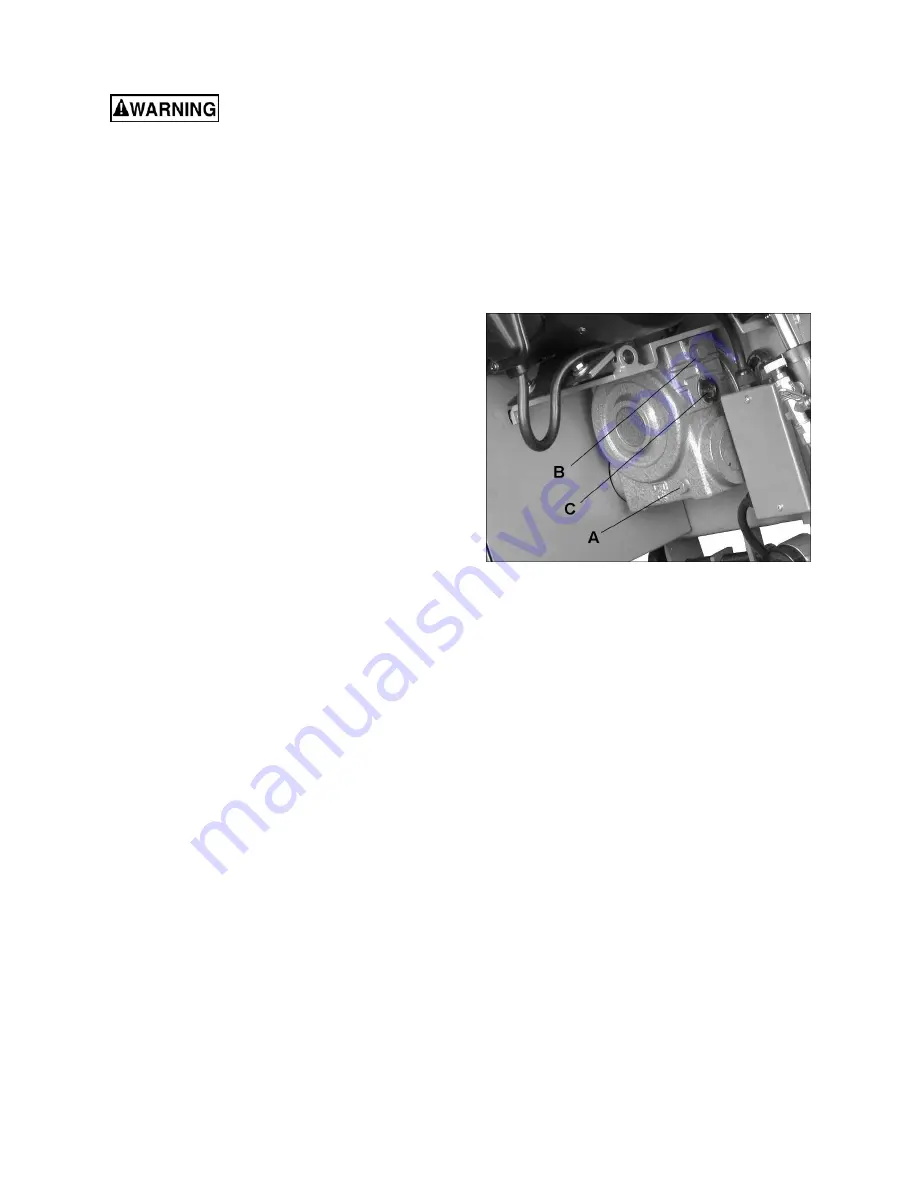
17
9.0
User-maintenance
Always disconnect power to
machine before performing maintenance.
Failure to do this may result in serious personal
injury.
Keep all surfaces clean and free of rust, slag, chips,
and coolant build-up.
Clear away metal particles with small paint brush or
parts cleaning brush. Do not use compressed air, as
it may force chips into the guide bearings and other
critical areas of saw.
Clean chip screen as needed.
Make frequent inspections of motor fan, and blow
out (with low pressure air hose) or vacuum any
accumulation of foreign material to maintain normal
motor ventilation.
Wipe saw down with a clean, dry cloth, and oil all
unpainted surfaces with light machine oil.
Check guide bearings frequently to make sure that
they are properly adjusted and turning freely, and
are free from metal particles.
Periodically inspect drive belt for wear or fraying.
Replace if needed.
To prevent corrosion of machined surfaces when a
soluble oil is used as coolant, pay particular
attention to wiping dry the surfaces where fluid
accumulates and does not evaporate quickly, such
as between table and vise.
Place a thin coat of oil on table surface on which vise
jaw slides.
If the power cord is worn, cut, or damaged in any
way, have it replaced immediately.
9.1
Lubrication
All ball bearings are permanently lubricated and
sealed. They require no further lubrication.
Drain and refill gear box oil after first 50 hours of
operation. Thereafter, change every six months.
Use an industrial gear oil.
To change gear box oil:
1. Disconnect machine from power source.
2. Place bow in horizontal position and allow a few
moments for oil to settle.
3. Remove drain plug (A, Figure 9-1) and drain oil
into suitable container. Reinstall drain plug.
4. Remove fill plug (B) and fill gear box until oil is
level with mid-point of sight window (C). Do not
overfill.
5. Install
fill
plug.
Periodically inspect sight window and maintain fluid
level.
Figure 9-1: gearbox
9.2
Coolant level
(HVBS-10DMW-C)
Maintain coolant level. Low coolant level can cause
foaming and high blade temperatures. Replace dirty
coolant; dirty or weak coolant can clog the pump,
cause crooked cuts, a low cutting rate and/or
permanent blade damage. Follow coolant
manufacturer’s instructions for proper use and
disposal.
9.3
Additional servicing
Any additional servicing on the band saw should be
performed by an authorized service representative.
Содержание HVBS-10-DMW
Страница 20: ...20 11 1 1 HVBS 8 DMW Bow Assembly Exploded View Figure 11 1...
Страница 21: ...21 11 1 2 HVBS 8 DMW Table Assembly Exploded View Figure 11 2...
Страница 22: ...22 11 1 3 HVBS 8 DMW Motor and Support Arm Assembly Exploded View Figure 11 3...
Страница 28: ...28 11 2 1 HVBS 10 DMW DMWC Bow Assembly Exploded View Figure 11 6...
Страница 29: ...29 11 2 2 HVBS 10 DMW DMWC Table Assembly Exploded View Figure 11 7...
Страница 30: ...30 11 2 3 HVBS 10 DMW DMWC Motor and Support Arm Assembly Exploded View Figure 11 8...
Страница 31: ...31 11 2 4 HVBS 10 DMW DMWC Vise and Table Assembly Exploded View Figure 11 9...
Страница 32: ...32 11 2 5 HVBS 10 DMW DMWC Base Assembly Exploded View Figure 11 10...
Страница 37: ...37 12 0 Electrical Connections for HVBS DMW Band Saws Figure 12 1...
Страница 39: ...39 This page intentionally left blank...
Страница 40: ...40 427 New Sanford Road LaVergne Tennessee 37086 Phone 800 274 6848 www jettools com...