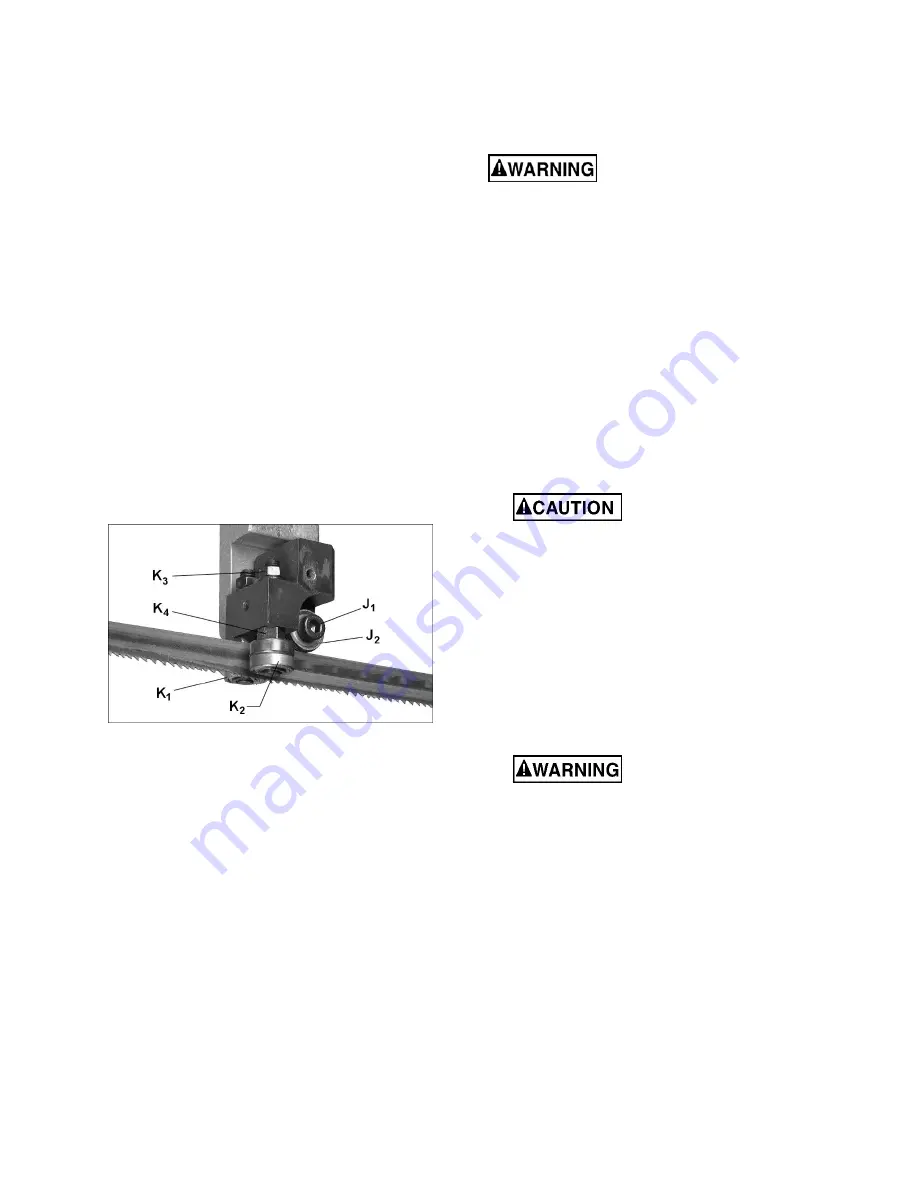
12
8. Install red blade guards.
9. Tension
blade
fully
(see
sect. 7.7)
10. Place two to three drops of lightweight oil on
blade.
11. Adjust blade guide bearings (see
sect. 7.6
).
12. Connect machine to power source and operate
it to make sure blade is tracking properly (
sect
7.7.2).
13. Follow blade break-in procedures
(sect. 8.2).
7.6
Blade guide bearings
1. Disconnect machine from power source.
2. Loosen screw (J
1
, Figure 7-7) and adjust back
bearing (J
2
) to approximately 0.002 to 0.003
inches from back edge of blade. Tighten screw
(J
1
).
3. Inside bearing (K
1
) is fixed. Outside bearing (K
2
)
rotates on an eccentric shaft. Loosen nut (K
3
)
and rotate lower nut (K
4
) to adjust eccentric
bearing to a clearance of 0.001 inches from
blade. Retighten nut (K
3
).
4. Repeat above steps for opposite blade guide
assembly.
Figure 7-7: blade guide bearings
7.7
Blade tension and tracking
Refer to Figure 7-8.
7.7.1
Tension
1. Disconnect machine from power source.
2. Loosen movable blade guide arm and slide it
away from the other arm as far as possible.
3. Turn blade tension handle (P, Figure 7-8)
clockwise to tighten blade. Pluck the blade with
your finger; a tensioned blade will emit a
“twang” sound. As experience with the saw is
gained, operator may develop a better feel for
how tight to set a particular blade.
For precise measurement, use a blade tension
gauge (not provided). Hard-back blades are
generally tensioned at about 25,000 PSI (1757
kg/cm
2
); bi-metal blades at about 35,000 PSI
(2460 kg/cm
2
).
4. Return blade guide arm to operating position.
Note: A new blade should be re-checked for proper
tension after a few minutes’ operation.
7.7.2
Tracking
Blade tracking adjustment
requires operating saw with wheel guards open.
This adjustment must be completed by qualified
persons only. Failure to comply may cause
serious injury.
Blade tracking has been set by manufacturer.
Adjustment is rarely required when blade is used
properly and is correctly welded.
Tracking is set properly when blade runs without
shifting on the wheels, and back of blade lightly
touches shoulder of wheels.
If adjustment is required:
1. Confirm that blade tension is properly set.
2. Set belt position to slowest speed.
3. Raise bow to convenient position and open
wheel guards.
While performing the
following steps, keep blade from rubbing
excessively on wheel shoulder. Excessive
rubbing will damage wheel and/or blade.
4. Run saw and observe blade – it should run next
to, but not tightly against, wheel shoulder.
5. If blade is not tracking properly, loosen either of
two hex nuts (N
1
, Figure 7-8).
6. Turn set screw (N
2
) with hex wrench, while
observing blade tracking on wheel.
NOTE:
This
adjustment is sensitive; start with 1/4-turns on
set screw and allow blade to respond to
changes.
Keep fingers clear of blade
and wheel to avoid injury.
7. Test the setting by placing a six-inch length of
paper between blade and wheel. The paper
should not be cut as it passes between wheel
shoulder and blade.
8. Turn set screw (N
2
) a small amount. Repeat
insertion of paper between the shoulder and the
blade until paper is cut into two pieces.
NOTE: You may have to repeat the check with
the paper several times before blade and
shoulder cut the paper into two pieces. Do not
hurry the adjustment. Patience and accuracy
here will pay off with better, more accurate,
quieter cutting and longer machine and blade
life.
Содержание HVBS-10-DMW
Страница 20: ...20 11 1 1 HVBS 8 DMW Bow Assembly Exploded View Figure 11 1...
Страница 21: ...21 11 1 2 HVBS 8 DMW Table Assembly Exploded View Figure 11 2...
Страница 22: ...22 11 1 3 HVBS 8 DMW Motor and Support Arm Assembly Exploded View Figure 11 3...
Страница 28: ...28 11 2 1 HVBS 10 DMW DMWC Bow Assembly Exploded View Figure 11 6...
Страница 29: ...29 11 2 2 HVBS 10 DMW DMWC Table Assembly Exploded View Figure 11 7...
Страница 30: ...30 11 2 3 HVBS 10 DMW DMWC Motor and Support Arm Assembly Exploded View Figure 11 8...
Страница 31: ...31 11 2 4 HVBS 10 DMW DMWC Vise and Table Assembly Exploded View Figure 11 9...
Страница 32: ...32 11 2 5 HVBS 10 DMW DMWC Base Assembly Exploded View Figure 11 10...
Страница 37: ...37 12 0 Electrical Connections for HVBS DMW Band Saws Figure 12 1...
Страница 39: ...39 This page intentionally left blank...
Страница 40: ...40 427 New Sanford Road LaVergne Tennessee 37086 Phone 800 274 6848 www jettools com...