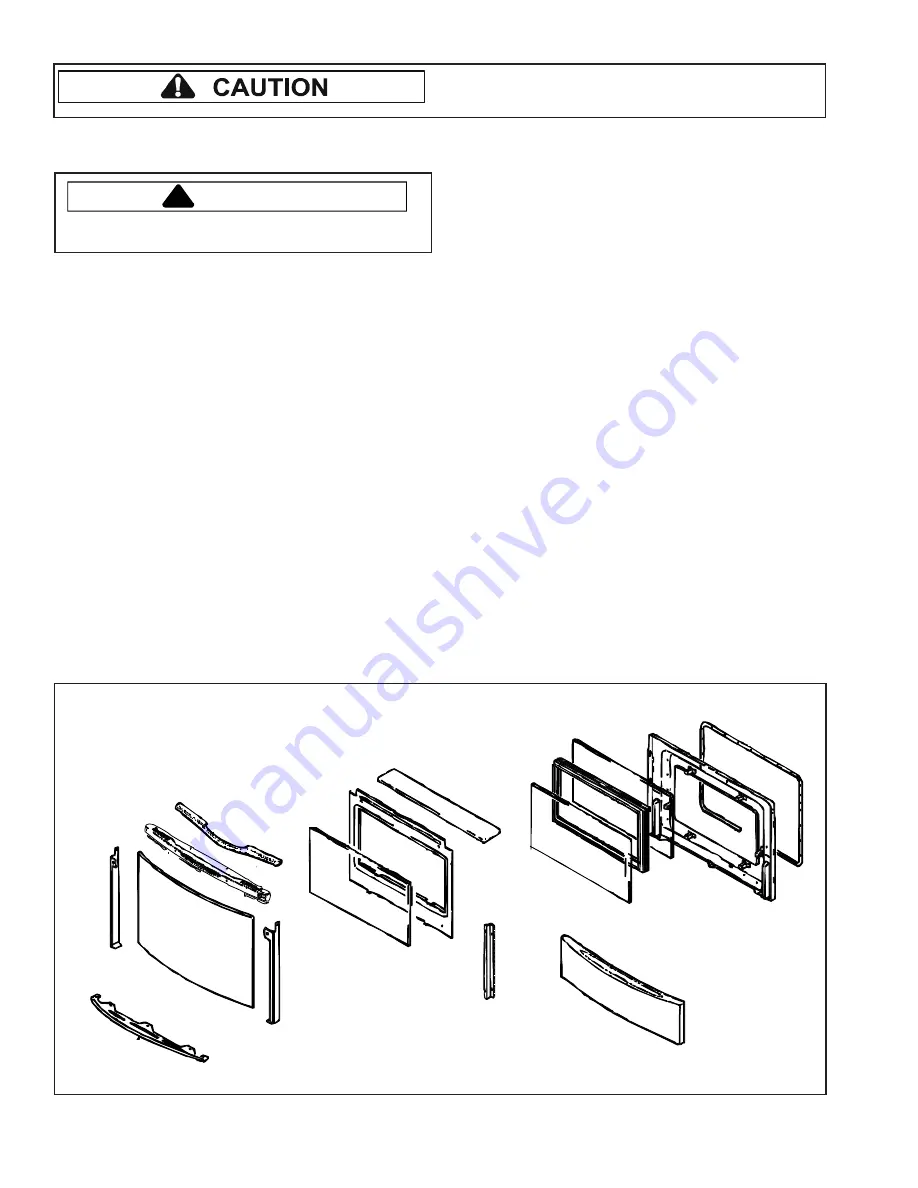
28
16026016
©2005 Maytag Services
Disassembly Procedures
To avoid risk of electrical shock, personal injury or
death; disconnect power to unit before servicing.
Access Panel
Glass
Retainer
Door
Trim
Door Trim
Door Gasket
Door Lining
Glass Frame
Inner Glass
Inner Glass
Oven Door Insulation
Glass Support
Door Trim
Door Handle
Door Baffle
Door Glass
Glass
Door
Oven Door Removal
WARNING
!
To avoid risk of personal injury or property damage, do
not lift oven door by the handle.
1. Open oven door and grasp door on both sides.
2. Lift up and off the hinge receivers.
3. Reverse procedure to reinstall oven door.
Oven Door Hinge
1. Remove power from unit.
2. Remove unit from installation position, see “Removing
and Replacing Range” procedure.
3. Remove oven door, see "Oven Door Removal"
procedure.
4. Remove front side trim, see "Front Side Trim"
procedure.
5. Remove the top and bottom screws securing hinge
receiver to the front frame.
6. Remove hinge receiver from oven chassis.
7. Reverse procedure to reinstall oven door hinge.
Door Disassembly
1. Remove oven door, see "Oven Door Removal"
procedure.
2. Place door on a protected surface.
3. Remove screws securing bottom trim to oven door.
4. Slide outer oven door glass and trim towards the
bottom of the oven door and remove.
5. Detach right and left trim pieces for outer door glass.
NOTE:
Proceed with the following steps for door handle
and inner door disassembly.
6. Remove screws securing top door handle trim to
oven door chassis.
7. Remove screws securing door handle brackets to
inner door panel.
8. Lift upward on the lower side of the door handle to
release side alignment screws and rotate towards the
top of the oven door to release and remove.
9. Remove screws securing door handle to door handle
brackets.
NOTE:
Proceed with the following steps for inner door
disassembly.
10. Remove screws securing lower door glass retainer to
door baffle and remove.
11 Slide inner door glass downward to release from
upper door glass retainers and remove.
12. Remove screws securing door baffle to door lining
and remove.
13. Remove insulation from oven door.
14. Lift inner glass and glass frame from oven door.
15. Reverse procedure to reassemble oven door.
Содержание JDS8850AAB
Страница 29: ... 2005 Maytag Services 16026016 A 1 Appendix A ...
Страница 45: ... 2005 Maytag Services 16026016 B 1 Appendix B ...
Страница 56: ...B 12 16026016 2005 Maytag Services Care Information CLEAN PAD CARE C LEANING NOTES ...
Страница 59: ... 2005 Maytag Services 16026016 C 1 Appendix C ...