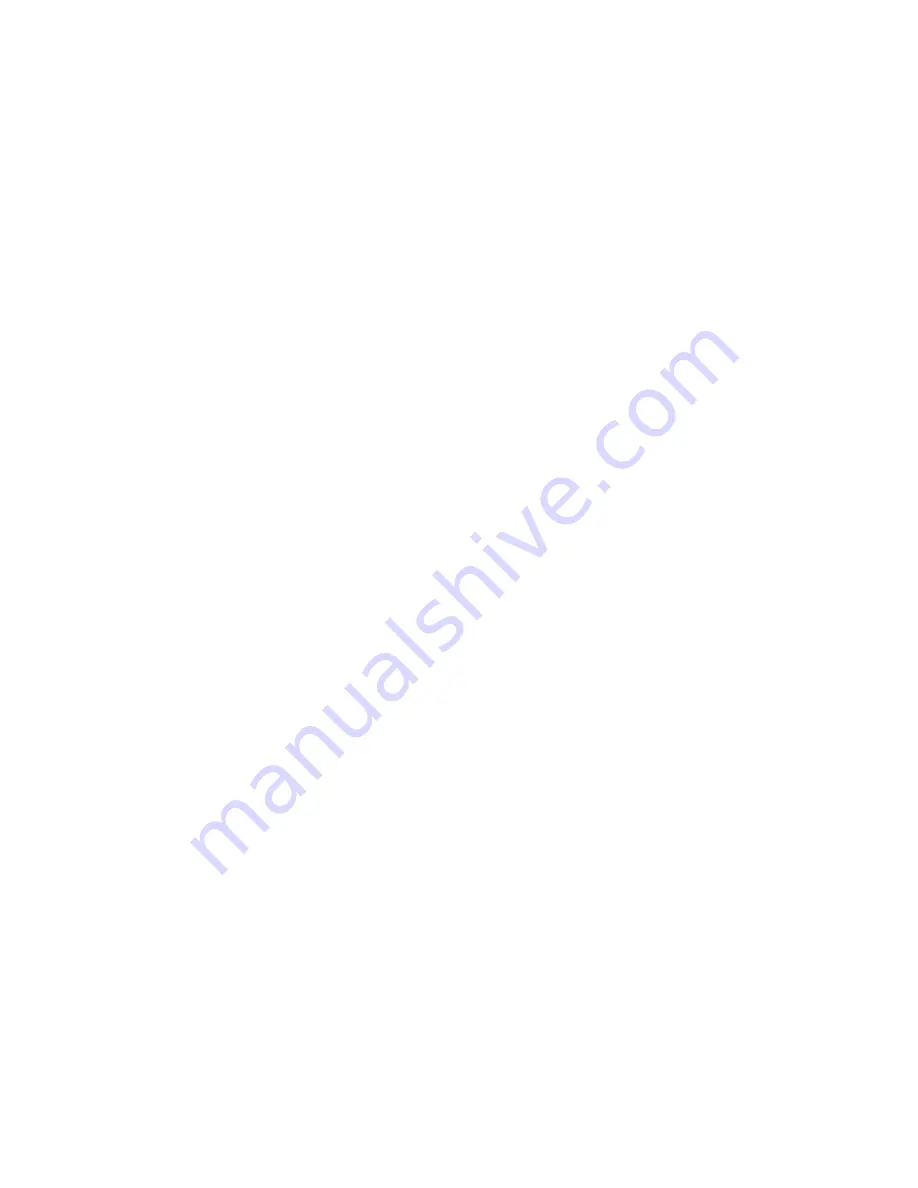
The burning grate adjuster plates (18) are used to increase or degrease the active burning
area. They are fitted into 45° angle against the burning chamber walls.
Reducing the burning area will reduce the power output of the boiler and the consumption
of logs. With these plates the boiler output can be adjusted between 20 - 40kW.
Secondary air adjuster plate (17) regulates the air flow on top of the burning chamber.
The flame diverter plate (16) can be pulled forwards when adding logs. This will reduce the
amount of smoke coming into the room through the open filling hatch. Once the logs have
been added, push the plate back against the boiler rear wall.
The boiler can be used with this plate removed without damaging the boiler but as the use of it
increases the boiler efficiency, we recommend that it is kept in place.
The chain from the thermostatic air adjuster (4) is connected to the extended arm of the primary
air hatch (8). Please follow the fitting instructions supplied with the valve.
Before lighting the boiler for the first time, make sure;
• The flue has been smoke tested
• The boiler is full of water and the pressure is between 0.5 - 1.3bar
• The heat transfer pump is working and all the isolating valves are open
• There are no leaks and the pressure relief valves are operational
When all the above has been verified, place a small amount of paper onto the cast iron
burning grate followed by kindligs and a small amount (2-4 pcs) of larger diameter dry logs.
Light the paper and make sure the primary air hatch (8) is open.
Once the larger logs are properly burning (10-15 minutes), add more logs as required.
This is perfectly normal and does not damage the boiler.
If however the boiler condensates throughout the burning, then the returning water is too cold.
A heat loading unit shown on the page 5 is designed to prevent this happening. If despite the
return thermostat and change to the correct one if needed. We recommend a 60 - 80°C return
temperature for the YPV 40 boiler.
3. BOILER COMISSIONING
7
On the first burning, the boiler can smell oily as the manufacturing and preserving oil burns off.
The boiler can also condensate a short while before it reaches the running temperature.
heat loading unit being installed, the boiler still condensates, then check the functioning of the