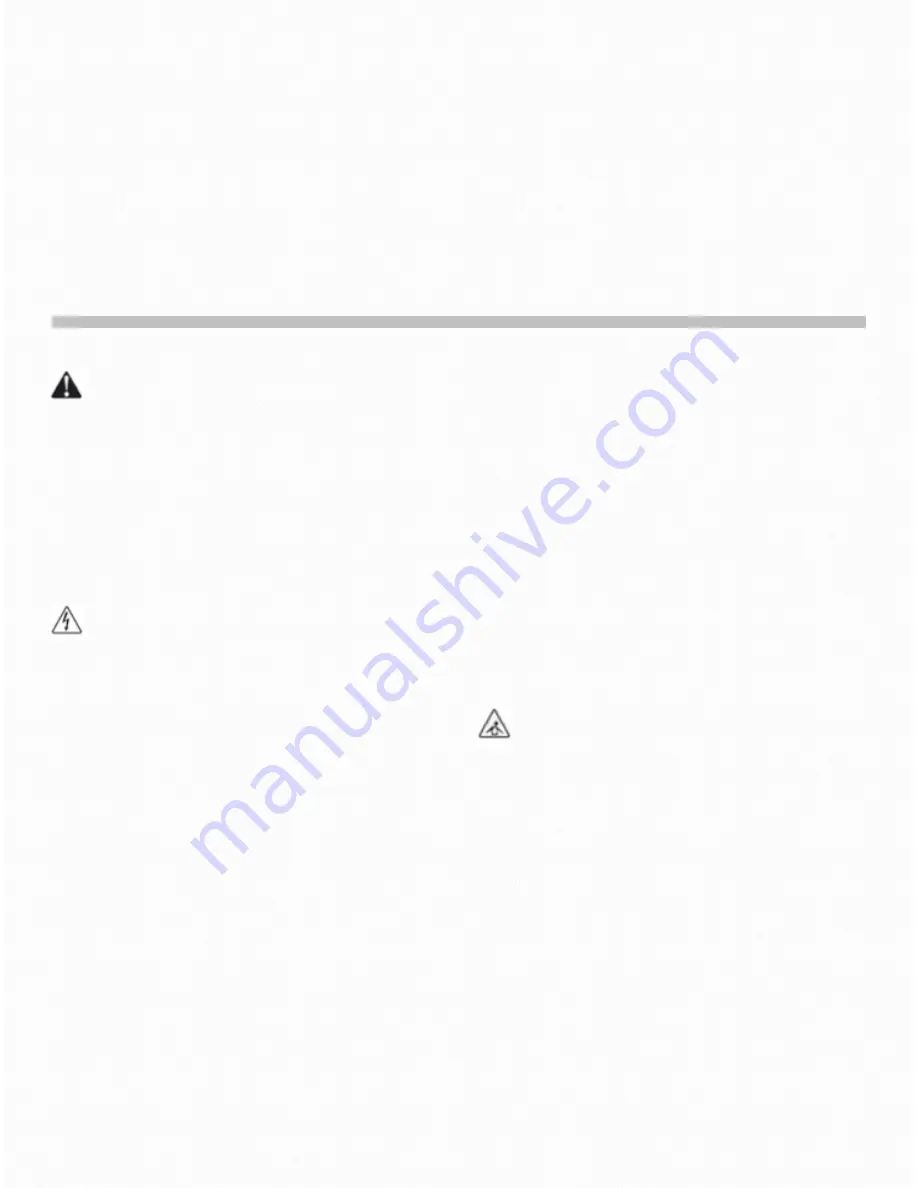
Safety Precautions
1
These general safety norms cover both arc welding
machines and plasma cutting machines unless
otherwise noted.
The equipment must only be used for the purpose it was
designed for. Using it in any other way could result in
damage or injury and in breach of the safety rules.
Only suitably trained and competent persons should use the
equipment. Operators should respect the safety of other
persons.
Prevention against electric shock
The equipment should be installed by a qualified person and
in accordance with current standards in operation.It is the
users responsibility to ensure that the equipment is
connected to a suitable power supply. Consult with your
utility supplier if required
If earth grounding of the work piece is required, ground it
directly with a separate cable.
Do not use the equipment with the covers removed.
Do not touch live electrical parts or parts which are
electrically charged.
Turn o
ff
all equipment when not in use.
Cables (both primary supply and welding) should be
regularly checked for damage and overheating. Do not use
worn, damaged, under sized, or poorly jointed cables.
Ensure that you wear the correct protective clothing, gloves,
head and eye protection.
Insulate yourself from work and ground using dry insulating
mats or covers big enough to prevent any physical contact
with the work ground.
Never touch the electrode if you are in contact with the work
ground, or another electrode from a di
ff
erent machine.
Do not wrap cables over your body.
Ensure that you take additional safety precautions when you
are welding in electrically hazardous conditions such as
damp environments, wearing wet clothing, and metal
structures. Try to avoid welding in cramped or restricted
positions.
Ensure that the equipment is well maintained. Repair or
replace damaged or defective parts immediately. Carry out
any regular maintenance in accordance with the
manufacturers instructions.
Safety against fumes and welding gases
Locate the equipment in a well-ventilated position.
Keep your head out of the fumes. Do not breathe the fumes.
Ensure the welding zone is in a well-ventilated area. If this is
not possible provision should be made for suitable fume
extraction.
If ventilation is poor, wear an approved respirator.
Read and understand the Material Safety Data Sheets
(MSDS’s) and the manufacturer’s instructions for metals,
consumable, coatings, cleaners, and de-greasers.
Do not weld in locations near any de-greasing, cleaning, or
spraying operations. Be aware that heat and rays of the arc
can react with vapours to form highly toxic and irritating
gases.
2
Содержание JT-200D
Страница 26: ...Electrical schematic 7 25 ...
Страница 27: ...Parts list 8 JT 200D 26 ...
Страница 29: ...JT 315D 28 ...