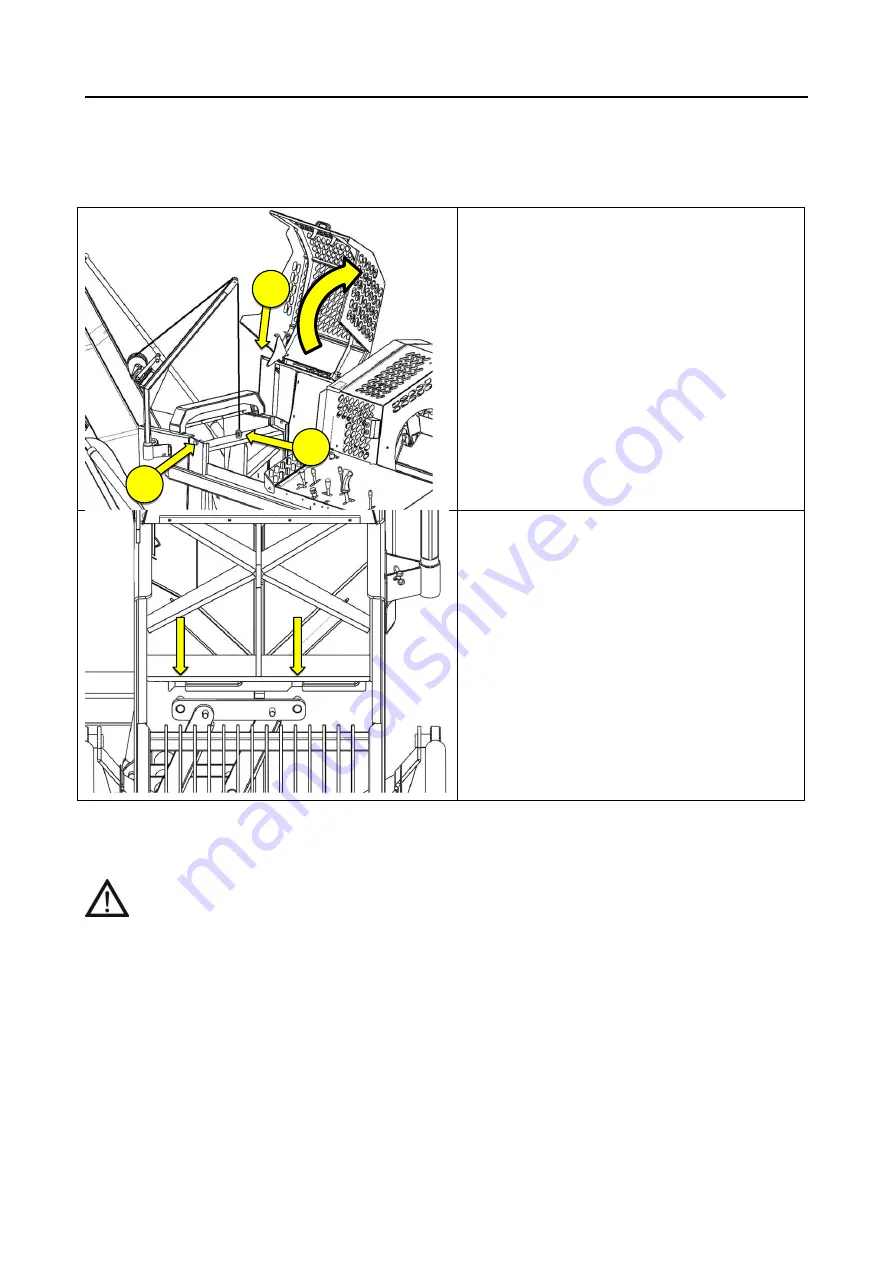
japa
485
User manual
Translation
20
485 1.0-2014
3.8 Replacing the splitting knife
Always use work gloves when handling the splitting knife.
A. Fully open the protective mesh of the splitting
area.
B. Remove the locking screw (1) of the splitting
knife rail.
C. Use the hydraulics to lift the knife to the upper
position.
D. Attach the eye screw (2) to the threaded
opening splitting knife, and fasten the winch wire
to the screw. The eye screw is stored in the tool
box behind the machine.
E. Use the winch to lift the splitting knife out of its
cradle, and lower it onto the ground on its side.
F. Lift the new knife up with the winch, and lower
it carefully into the knife cradle.
G. Lower the knife further and ensure that its
slots connect properly with the lifting mechanism.
H. Disconnect the eye screw (2) and winch wire
from the splitting knife.
B. Attach the locking screw (1) of the splitting
knife rail.
J. Release the hook (3) and close the protective
mesh of the splitting area.
DO NOT WALK UNDER A SPLITTING KNIFE SUSPENDED FROM THE WINCH!
1
2
3
Содержание 485
Страница 1: ...ENGLISH japa 485 User manual TR Tractor drive TRE Electricity and tractor drive 6 0t 8 0t ...
Страница 40: ...japa 485 User manual Translation 38 485 1 0 2014 8 1 Electric motor connection diagram TRE models ...
Страница 42: ...japa 485 User manual Translation 40 485 1 0 2014 8 2 Hydraulics diagram ...
Страница 43: ...japa 485 User manual Translation 41 485 1 0 2014 ...
Страница 44: ...japa 485 User manual Translation 42 485 1 0 2014 ...
Страница 45: ...Translation 43 485 1 0 2014 ...
Страница 46: ...Translation 44 485 1 0 2014 ...
Страница 47: ...Translation 45 485 1 0 2014 ...
Страница 48: ...Translation 46 485 1 0 2014 ...