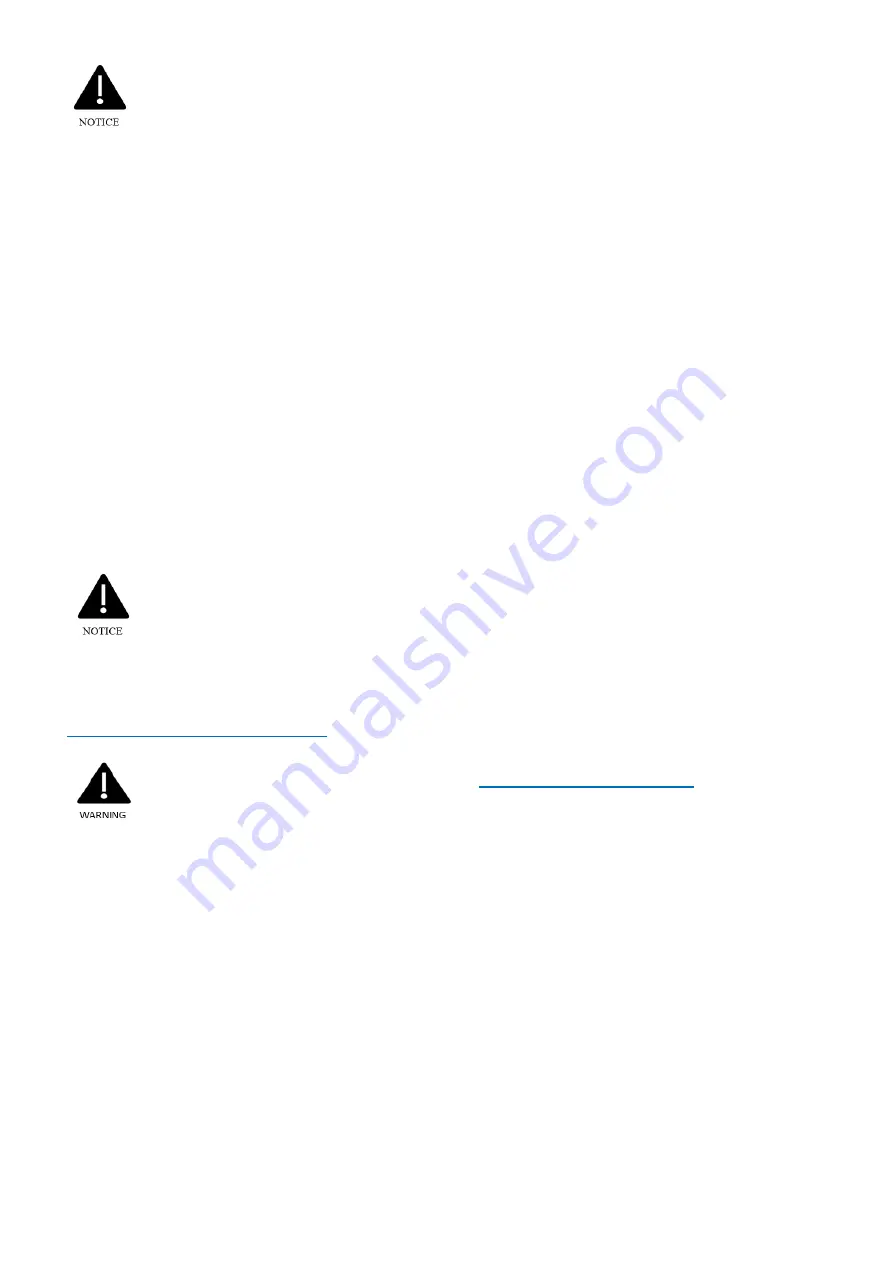
Issue: 01.06.2023
Page 10
Before starting the system, ensure that all
electrical connections are correctly made and
tight, service ports are in the correct position
and all covers and guards are fitted.
Unit startup
•
Switch on the power at the mains isolator and then
switch on the rocker switch on the front of the indoor
unit.
•
Set the required cold room temperature on the
electronic controller and check the system parameters
in the controller as required (the controllers are pre-
programmed in the factory to suggested settings).
•
Run the system to the required temperature and check
system pressures, gas charge and running currents of
motors to ensure correct operation.
•
Carry out a manual defrost (press the defrost button on
the controller for more than 2 seconds) to ensure the
defrost period is adequate to clear any frost build up
on the evaporator coil.
•
Carry out final leak test and ensure all covers are
fitted and securing screws are tightened.
•
Log all information along with system model and serial
numbers for future reference.
•
Ensure that the customer / responsible person is
provided with basic operating instructions and where
electrical isolators are situated in case of emergency.
An anti-short cycle timer is built into the
indoor controller to prevent the compressor
from stop/starting too quickly, which can
result in the compressor tripping on its
internal overload. If the overload trips,
please allow time for it to cool down and auto reset
before restarting.
Service & Maintenance
Warning!
–
Disconnect the mains electrical
supply before servicing or opening the units.
The units are designed to give long life
operation with minimum maintenance. However, it should be
routinely checked, and the following service schedule is
recommended under normal circumstances:
1. Indoor and Outdoor units
–
Inspect at regular intervals
•
Check for refrigerant leaks on all joints and
fittings.
•
Check mountings for tightness and wear.
•
Inspect pipework for any damage.
•
Check all electrical connections.
•
Ensure that no abnormal noise or vibration is
detected during the test run.
2. Condenser & Evaporator Fan Motors & Blades
–
Clean
and inspect at regular intervals
•
Check for abnormal noise, vibration, and fan
imbalance.
•
Ensure that the fan motors are clean and spin
freely.
•
Check that the fan blades are clean and free from
restriction and damage/imbalance.
•
Note:
The Fan Motors are pre-lubricated, and
factory sealed so no maintenance is necessary.
3. Condenser & Evaporator Coils
–
Clean and inspect at
regular intervals
•
Check and remove the dirt and debris between
the fins using a soft brush and/or a suitable
chemical coil cleaner then rinse with clean water.
•
Check and remove any obstacles that may hinder
the airflow through the coils.
•
Repair any damage to fins and ensure any guards
are fitted correctly.
•
DO NOT USE HIGH PRESSURE WASHERS ON
COILS
–
THEY DAMAGE THE FINS.
4. Controls
•
Check controller settings and operation.
•
Check calibration of temperature probe reading.
5. Power Supply
–
Inspect at regular intervals.
•
Check the running current and voltage for the units.
•
Check the electrical wiring and tighten the wires
onto the terminal blocks if necessary.
6. Refrigerant Charge
•
Check the refrigerant charge by ensuring that the
system is operating correctly, and the system
pressures are as expected.
•
Carry out a full leak test.
7. Unit decommissioning and disposal
•
At the end
of the system’s useful life, a suitably
qualified engineer should decommission it. The
refrigerant and compressor oil are classed as
hazardous waste and as such must be reclaimed
and disposed of in the correct manner, including
completion of waste transfer paperwork. The
system components must be disposed of or
recycled as appropriate in the correct manner.
F-Gas Requirement
The equipment covered in this Technical Manual relies on
fluorinated greenhouse gases R448A and R449A for their
functioning.
J & E Hall Cellar and Product Cooler is a non-hermetically
sealed system where the outdoor unit is designed to use
with R448A and R449A. The outdoor and indoor unit
models come from the factory pressurized with OFN
(Oxygen Free Nitrogen) only. The system had to be
charged with the recommended charge specified in
Table 2.
In F-Gas Regulation EU 517/2014, this type of system only
be able to be installed by engineers who hold an F Gas
qualification.
The requirement for leak testing is based on the charge size
in tonnes of CO
2
equivalent specified in below table.
Starting 1st January 2017, the requirement for leak
detection and maintaining system logs changes from 3kg
HFC to 5 tonnes CO2 equivalent.
Содержание JCC3
Страница 1: ...JCC3 CELLAR AND PRODUCT COOLERS ISSUE 01 06 2023 CELLAR COOLER RANGE TECHNICAL MANUAL R448A R449A...
Страница 20: ...Issue 01 06 2023 Page 20 Figure 18 Declaration of Incorporation Outdoor Unit...
Страница 21: ...Issue 01 06 2023 Page 21 Figure 19 Declaration of Incorporation Indoor Unit...
Страница 22: ...Issue 01 06 2023 Page 22 Figure 20 EU Declaration of Incorporation Outdoor Unit...
Страница 23: ...Issue 01 06 2023 Page 23 Figure 21 EU Declaration of Incorporation Indoor Unit...