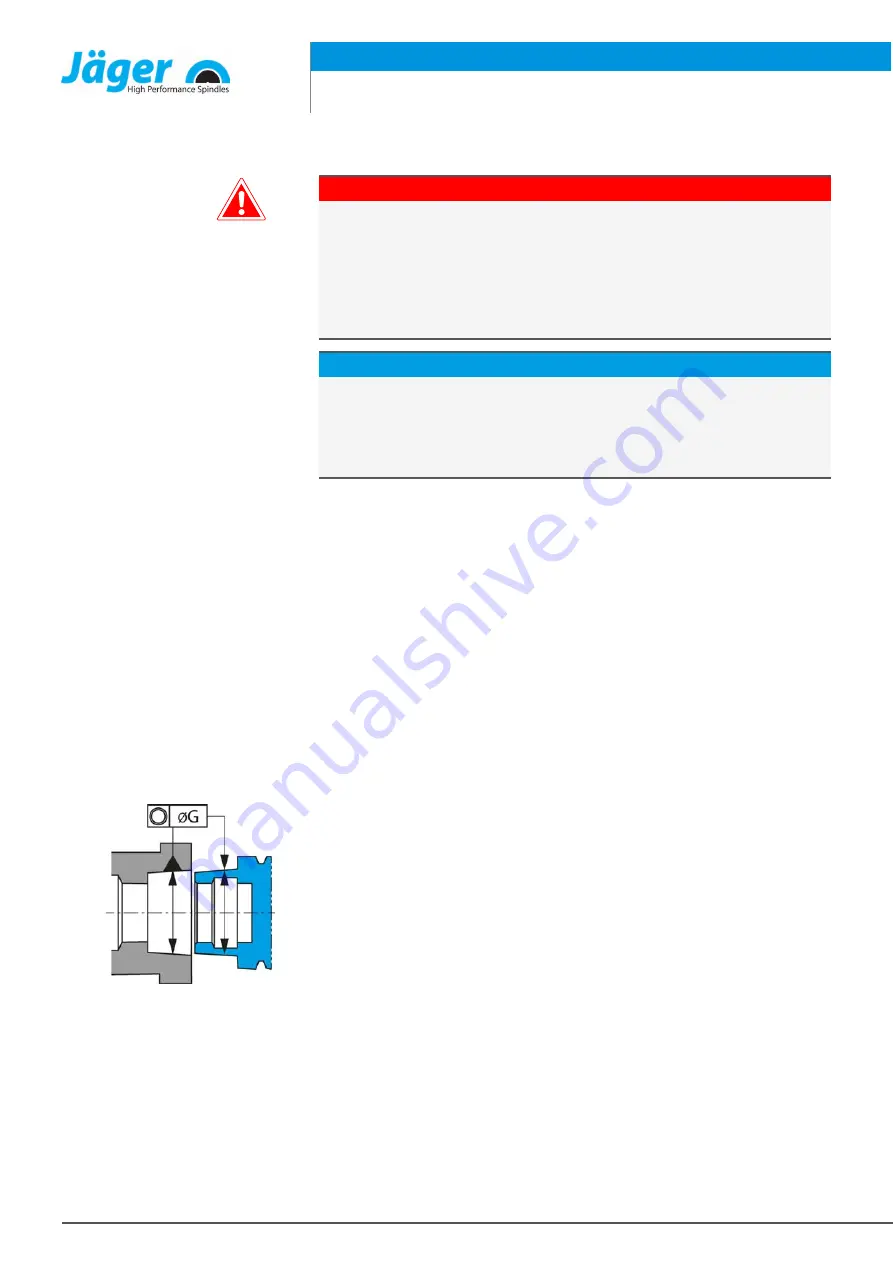
Tool change
Item no. 10405064, Revision 09
36 ( 48 )
10.2
hydraulic taper change
DANGER: Due to flying parts.
The taper cleaning could build up air pressure in the hollow shank taper dur-
ing the tool taper change. This air pressure flings out the hollow shank taper
in the case of sudden release.
u
Only use tool tapers with a centric through-hole.
u
Always switch off the taper cleaning when the hollow shank taper is ap-
prox. 1-2 mm away from the contact surface.
Tip: Ensure concentric run-out quality.
u
Keep collet, clamping nut, contact surface, shaft, tool taper, and tool
mount clean at all times.
u
Check the tool taper mount.
It must be free of damage and clean when switching to the HF spindle.
Ü
Make sure that the shaft of the HF spindle has come to an absolute stand-
still.
Ü
Switch on the hydraulics for “cylinder forward”.
Ü
Remove the tool.
Ü
Clean the inner taper of the tool mount and the inner taper of the shaft
with the felt cleaning taper.
Ü
Insert the tool.
Ä
Insert the tool up to the contact surface of the clamping taper.
Ü
Switch on the hydraulics for “cylinder back”.
Ü
Wait for 1-2 seconds after the tool change.
Ü
Start the HF spindle.
10.2.1
Automatic hollow shank taper tool clamp
Coaxiality tolerance
We recommend the following values:
Ü
Coaxiality tolerance when changing the tool.
Ä
Coaxiality (ØG): 0,7 mm
Ü
Contact force on clamping taper.
Ä
Maximum: 140 N