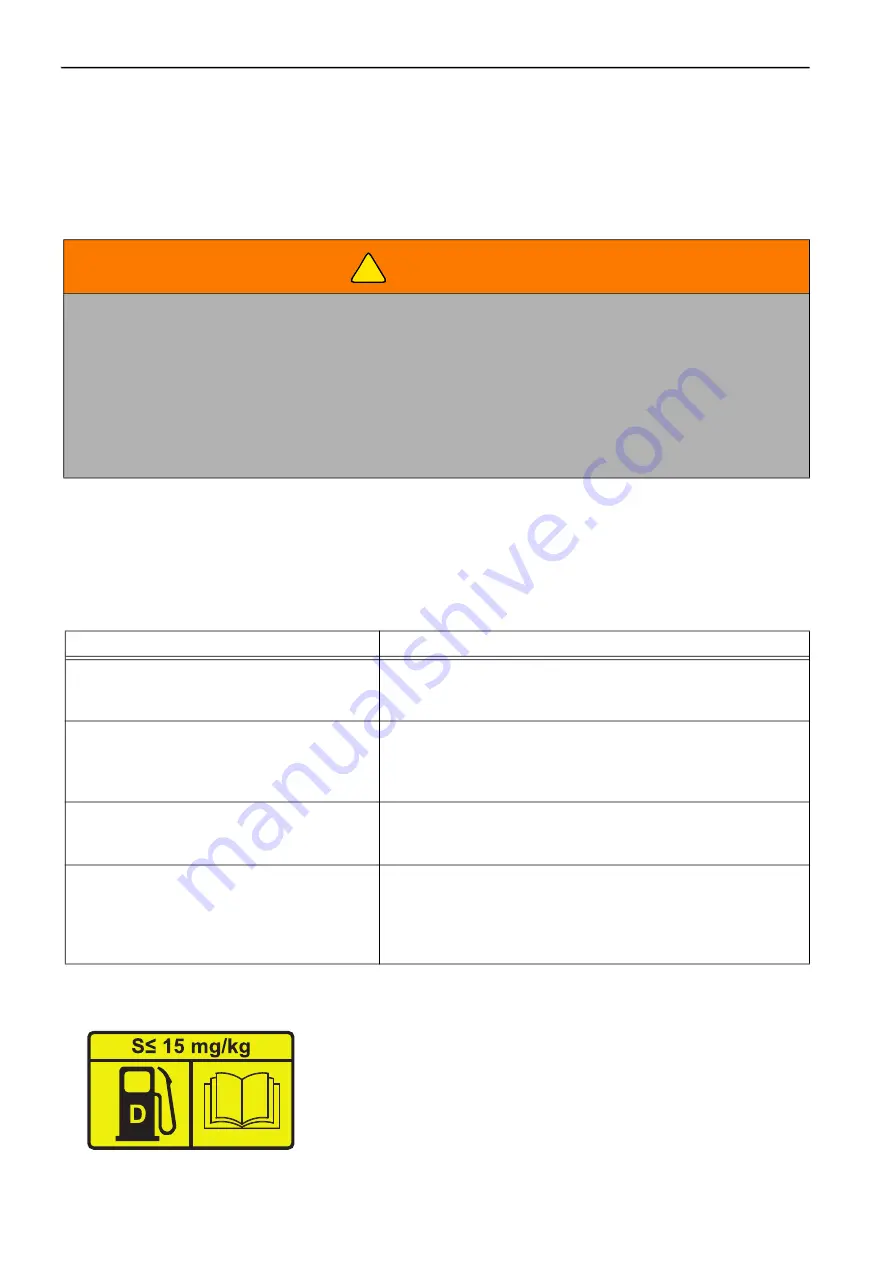
en-72
8 MAINTENANCE AND LUBRICATION
8.9 FUEL________________________________________________________________
Diesel fuel is flammable. Use caution when you add the fuel to the mower.
Only use an approved container.
The spout on the container must fit inside the fuel filler neck. Never use the containers that are not approved to
keep or transfer fuel.
Fill the fuel tank to less than 25 mm (1 inch) below the filler neck.
Use clean Ultra Low sulfur diesel fuel to the recommended specification. The use of diesel fuel additives is not
recommended. If fuel additives are used, the fuel additives must be approved for use in the engine type used in
your machine. Refer to the engine manual for additional information.
Check fuel hoses and clamps at service interval (see chart). Replace the fuel hoses and clamps at first indication
of wear or damage.
Keep the fuel according to your local, state or federal regulations. Below are some items you should be aware of.
8.10 FUEL SYSTEM ________________________________________________________
Use Diesel to B.S. EN590 or ASTM D975 (Ultra Low Sulfur)
WARNING
Refuel the mower before you start the engine. When the engine is in operation or while the engine is hot,
never remove the fuel cap or add fuel to the mower.
Refuel outdoors only and do not smoke when you add fuel.
If the fuel spills, do not try to start the engine, but move the mower away from the area. Until fuel vapors are
removed, do not allow the sparks, open flame or other types of ignition.
Never keep fuel containers near an open flame or any device that can cause the ignition of fuel
or fuel vapors.
Always tighten the fuel tank cap and container cap after you add fuel.
What you need to do
Reasons to do it
Ask your fuel supplier if there are records
showing the amount of water mixed in with
the Diesel fuel supplied.
Water in the fuel is harmful to the high-pressure injection
equipment. Kubota recommends that water content must not
be more than 0.05%
Ensure that Bio content to your Diesel fuel
does not exceed 7% as described in ASTM
D6751 or EN 14214
Higher Bio Diesel content has been proven to absorb more
moisture from the atmosphere. The moisture and Bio content
can result in the development of molds and bacteria. These
accelerate the blocking of fuel filters.
Ask your fuel supplier to verify that fuel
being delivered meets the lubricity level
required set in ASTM D6079
Low emission Diesel engines use higher pressure injection
equipment. The tolerances in the injection equipment require
the fuel to provide lubrication.
Ask your fuel supplier to verify that fuel
being delivered has less than 1milligram of
solid contaminant per litre of fuel.
Any particles in the fuel can damage parts within the fuel
injection system, reducing performance. The vehicle fuel sys
-
tem will provide protection, but the cleaner the fuel into the
vehicle, the lower the chance of a particle by passing the fil
-
tration system.
!
4324674