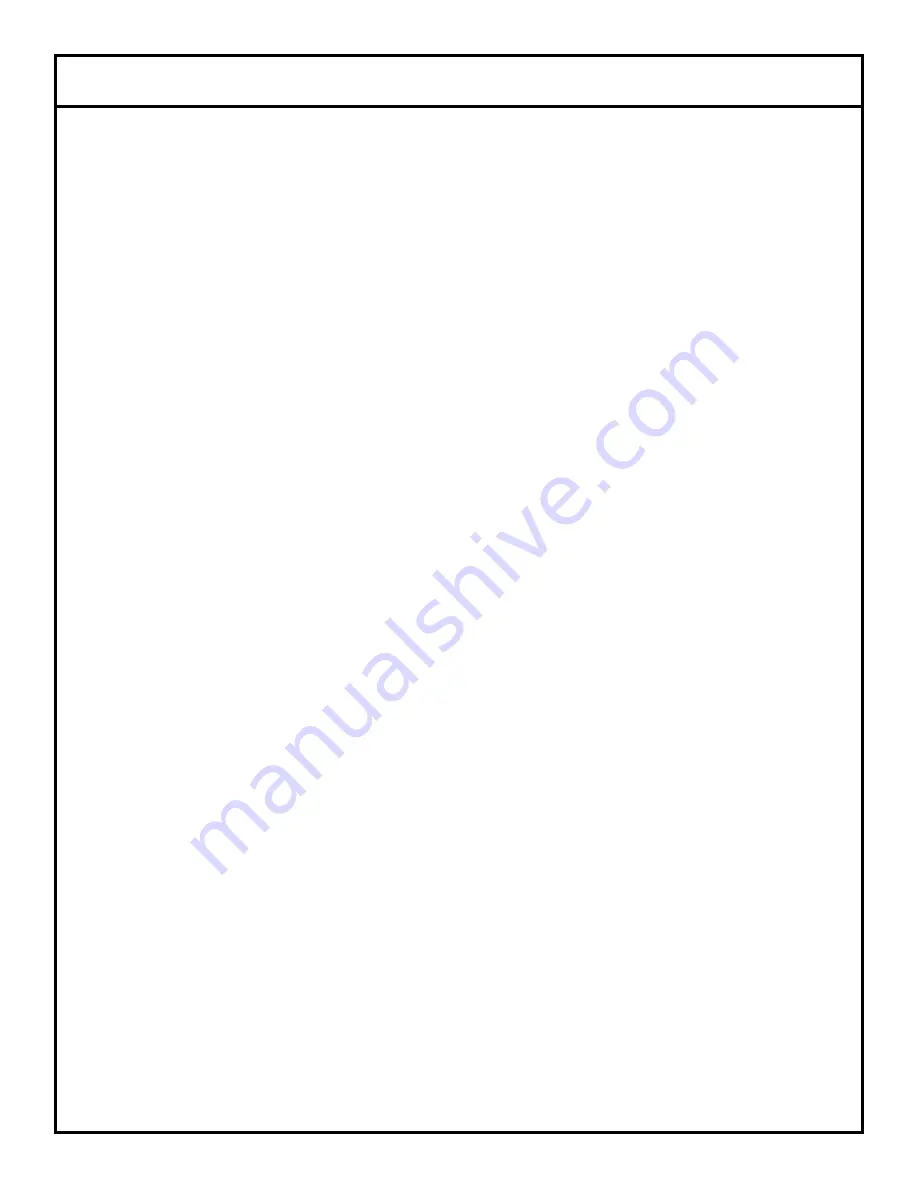
PREPARATION:
Before proceeding with the start-up of the unit,
verify the following:
1. The sump strainer is in place and is clean.
2. The drain stopper is installed.
3. That the wash and rinse arms are screwed securely
into place and that their endcaps are tight. The wash
and rinse arms should rotate freely.
POWER UP:
To energize the unit, turn on the power at the service
breaker. The voltage should have been previously verified as
being correct. If not, the voltage will have to be verified.
FILLING THE WASH TUB:
For the initial fill, close doors and
depress and hold the OFF/ON/FILL rocker switch in the FILL
position for approximately 8 - 10 seconds. Open the doors and
verify that the water level is correct. Hereafter, the water level is
controlled by the timer that has been preset at the factory. Verify
that the drain stopper is preventing the wash tub water from pour-
ing out excessively. There may be some slight leakage from the
drain hole. Verify that there are no other leaks on the unit before
proceeding any further. The wash tub must be completely filled
before operating the wash pump to prevent damage to the com-
ponent. Once the wash tub is filled, the unit is ready for operation.
The water level was set at the factory. If the water level is not at
the level noted above, it will require adjustment. Check to ensure
that the recommended water pressure is being supplied to the
machine (20 PSI). If the water pressure is correct then the fill
valve will need adjustment. Use the following steps to adjust the
cam. Turn power off at the machine circuit breaker. Open the
control box cover. Locate the timer fill valve cam (Cam 4 from the
timer motor). Locate the spanner wrench taped to the electrical
panel. The spanner wrench is used to adjust the cam.
To increase the water level, open the notch of the adjustable cam.
To decrease the water level, close the notch. Care must be taken
that the set point does not extend into the home position of the
timer. Do not move the side of the cam that starts the fill; this will
change the sequence of cycle operation. With the door closed
turn the power circuit breaker on. Open and close the door to run
a cycle, then check the water level. Adjust as necessary then
close the control box cover.
The machine runs a complete cycle to drain and fill. If the
machine is not allowed to drain, the water will build up inside the
tub. After the initial fill, the rinse water for the current cycle will
become the wash water for the next cycle.
WARE PREPARATION:
Proper preparation of ware will help
ensure good results and less re-washes. If not done properly,
ware may not come out clean and the efficiency of the dishma-
chine will be reduced. It is important to remember that a dishma-
chine is not a garbage disposal and that simply throwing
unscraped dishes into the machine simply defeats the purpose
altogether of washing the ware. Scraps should be removed from
ware prior to being loaded into a rack. Pre-rinsing and pre-soak-
ing are good ideas, especially for silverware and casserole dish-
es.
Place cups and glasses upside down in racks so that they do not
hold water during the cycle. The dishmachine is meant not only to
clean, but to sanitize as well, to destroy all of the bacteria that
could be harmful to human beings. In order to do this, ware must
be properly prepared prior to being placed in the machine.
DAILY MACHINE PREPARATION:
Refer to the section entitled
“PREPARATION” at the top of this page and follow the instructions
there. Afterwards, check that all of the chemical levels are correct
and/or that there is plenty of detergent available for the expected
workload.
WARM-UP CYCLES:
For a typical daily start-up, it is recom-
mended to run the machine through 3 cycles to ensure that all of
the cold water is out of the system and to verify that the unit is
operating correctly. To cycle the machine, ensure that the power
is on and that the tub has filled to the correct level. Lift the doors
and the cycle light will illuminate. When the light goes out, close
the doors, the unit will start, run through the cycle, and shut off
automatically. Repeat this two more times. The unit should now be
ready to proceed with the washing of ware.
WASHING A RACK OF WARE:
To wash a rack, open the doors
completely (being careful for hot water that may drip from the
doors) and slide the rack into the unit. Close the doors and the
unit will start automatically. Once the cycle is completed, open the
door (again watching for the dripping hot water) and remove the
rack of clean ware. Replace with a rack of soiled ware and close
the doors. The process will then repeat itself.
OPERATIONAL INSPECTION:
Based upon usage, the pan
strainer may become clogged with soil and debris as the workday
progresses. Operators should regularly inspect the pan strainer to
ensure it has not become clogged. If the strainer does, it will
reduce the washing capability of the machine. Instruct operators
to clean out the pan strainer at regular intervals or as required by
work load.
SHUTDOWN AND CLEANING:
At the end of the workday, close
the doors. When the unit completes the cycle, turn the power
switch to the OFF position and open the doors. Manually remove
the drain stopper from the tub and allow the tub to drain (NOTE:
the wash tank water will be hot so caution is advised). Once the
wash tub is drained, remove the pan strainer and the pump suc-
tion strainer. Remove soil and debris from the strainer and set to
the side. Unscrew the wash and rinse arms from their manifolds.
Remove the endcaps and flush the arms with water. Use a brush
to clean out the inside of the arms. If the nozzles appear to be
clogged, use a toothpick to remove the obstruction. Wipe the
inside of the unit out, removing all soil and scraps. Reassemble
the wash and rinse arms and replace them in the unit. The arms
only need to be hand tight, do not use tools to tighten them down.
Reinstall the strainers and close the doors.
OPERATION INSTRUCTIONS
4