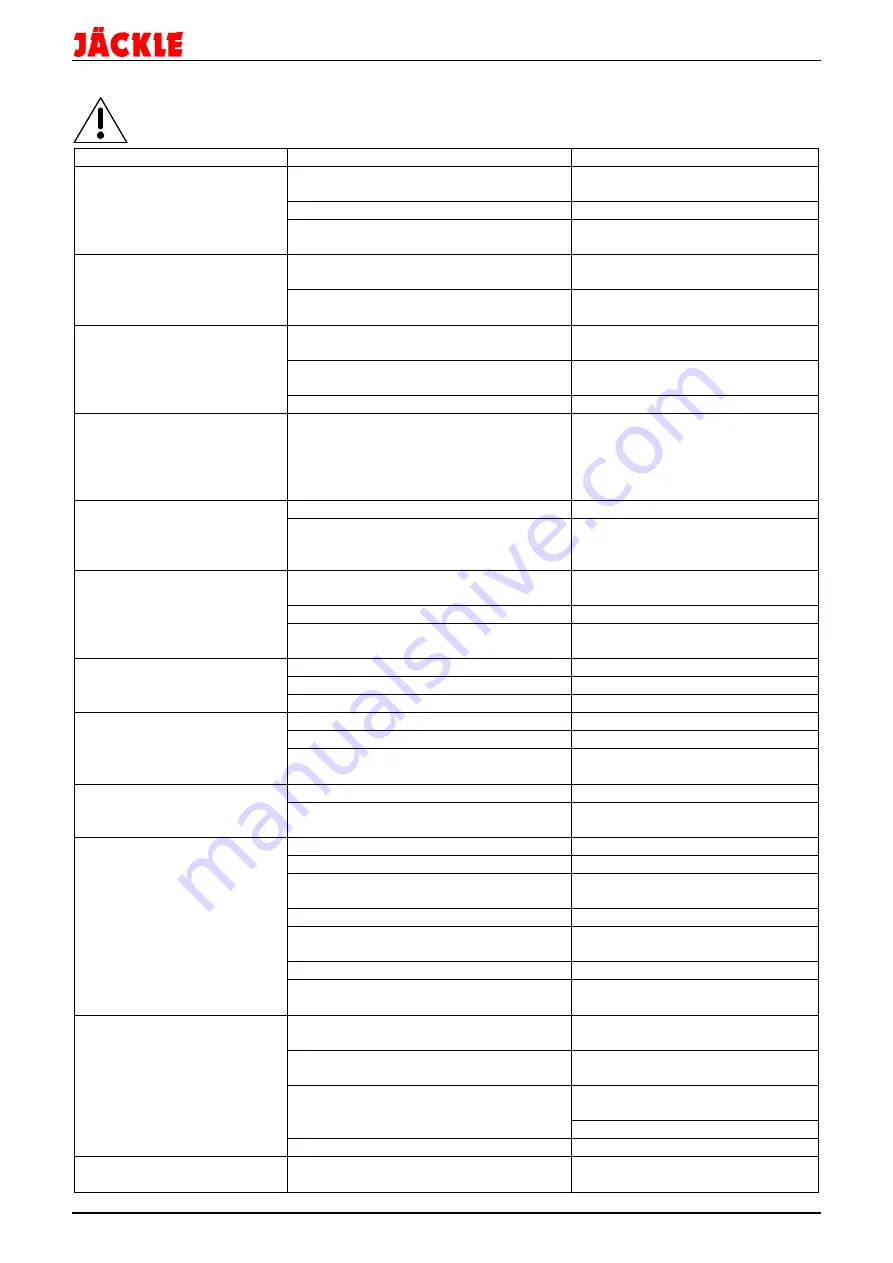
conMIG 400/445/545
Operating manual
Page 48
40. Trouble - shooting
Any remedial action to defective electrical equipment must be carried out by a qualified electrician!
Malfunction/error
Cause
Remedy
Display
T°C – 01/02/03 – hot
Machine overheated
(See Point 33)
Machine to cool down with a
running fan
Thermal sensor line interrupted
Look for and eliminate interruption
Wrong type of machine in the control
box set
Contact service partner
Display
T°C – int – e.g. +56
(See Point 20)
Ambient temperature below -10 ° C or
above +40 ° C
Bring Machine into normal
temperature range
Thermocouple defect in the control box
Change control box
Sensor repaired
Display (continuously)
Err H2o ---
(To clear switch machine off
and on)
Water tank empty
Fill in cooling water with alcohol in
the ratio 4:1
Water flow below 0.25 l / min
Check water flow
Torch / pipe
Flow meter is defective
Flow meter exchange
Display (continuously)
Err CAn
Communication between wire feed case
(control box MC) and machine is
disconnected
Intermediate hose pack - cable
broken, plug defective
controlbox MC or control pcb
inside the welding machine
defective
Main switch ON
1 or 2 green Indicator lights
on the front plate are not lit
(see control elements)
Failed one or more system phases
Check main supply and fuses
Fuse in the front plate defective
Change fuse 2A slow
Main switch ON
Green control lamps are light
Control box MC without
function
Secondary fuse on auxiliary transformer
defective
Change fuse 6,3A slow
Fuse in control box MC defective
Change fuse 6,3A slow
Cable in torch hose pack defective /
broken
Check 5 pole cable
No function after pressing
torch trigger key
Torch trigger defective
Change torch trigger
Torch control line interrupted
Check torch control line
Control box MC defective
Change control box
Fire feed motor out of service Control box MC defective
Change control box
Fire feed motor defective
Change wire feed motor
Wiring between control box and Motor
interrupted
Check wiring
Wire buckling between wire
feed rollers and guide tube
Pressure of the wire feed rolls to big
See chapter 32
Distance from wire feed rollers to guide
tube too far
Check distance / realign wire
guide tube
Irregular wire feed
Bad uncoiling of wire
Check / refit wire coil
Wire-holding arbour runs heavily
Check wire- holding arbour
Wrong wire feed roller
Use the right wire feed roller
See chapter 32
Dirty / defective wire guide tube or spiral See chapter 32
Cogged / defective current contact tip
Clean / exchange current contact
tip
Dirty/ rusty welding wire
Exchange welding wire
Wire guide tube misaligned with wire
feed roller groove
See chapter 32
Porous weld seam
Work piece surface polluted(paint, rust,
oil, grease)
Clean surface
No shielding gas(solenoid valve not
opening)
Check / exchange solenoid valve
or gas tube
Insufficient shielding gas
Check shielding gas at pressure
reducer
Check gas line for leakage
Gas nozzle polluted
Clean gas nozzle
Wire burns back into current
contact tip at start of process
Deficient wire feed, feed rollers idling
See chapter 32
Содержание conMIG 400
Страница 2: ......
Страница 28: ...conMIG 400 445 545 Operating manual Page 25...
Страница 52: ...conMIG 400 445 545 Operating manual Page 49 41 Ersatzteile spare parts Frontansicht front view Oben top view...
Страница 54: ...conMIG 400 445 545 Operating manual Page 51 Seitenansicht links sideview left...
Страница 56: ...conMIG 400 445 545 Operating manual Page 53 Seitenansicht rechts sideview right...
Страница 58: ...conMIG 400 445 545 Operating manual Page 55 Koffer wire feed case DVK 3 2010...
Страница 61: ...conMIG 400 445 545 Operating manual Page 58 Koffer wire feed case DVK 4 2010...
Страница 71: ......