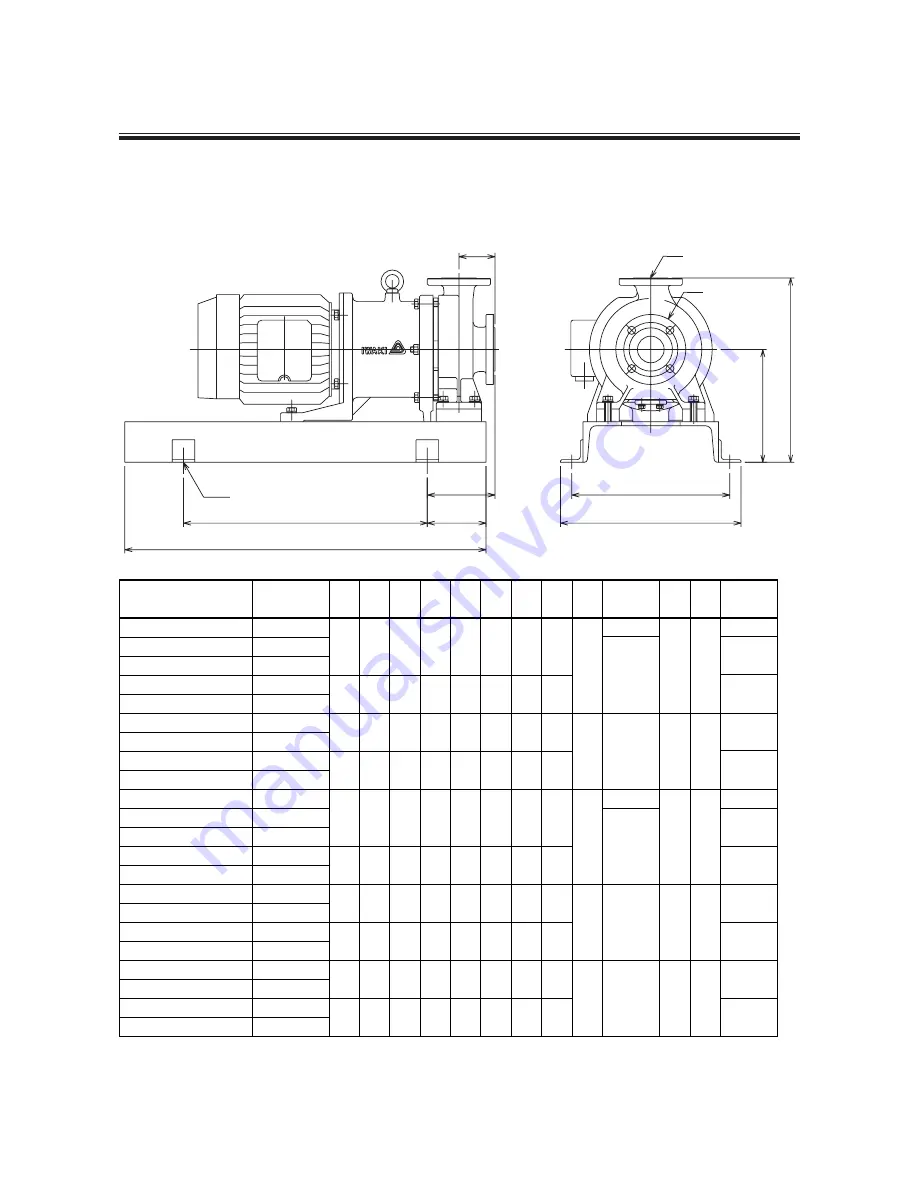
- 10 -
b
b
Outer dimensions in mm
Flange mounted motor type
Model
Motor
W
H
a
b
c
d
e
f
g
h
A
B
Mass
W/O Motor
(kg)
MDE32-160
MDE32-160
MDE32-160
MDE32-160
MDE32-160
MDE32-200
MDE32-200
MDE32-200
MDE32-200
MDE40-160
MDE40-160
MDE40-160
MDE40-160
MDE40-160
MDE40-200
MDE40-200
MDE40-200
MDE40-200
MDE50-160
MDE50-160
MDE50-160
MDE50-160
*1
*1
*1
*1
*1
*2
*2
*2
*2
*1
*1
*1
*1
*1
*2
*2
*2
*2
*1
*1
*1
*1
4.0kw
5.5kw
7.5kw
11kw
15kw
5.5kw
7.5kw
11kw
15kw
4.0kw
5.5kw
7.5kw
11kw
15kw
5.5kw
7.5kw
11kw
15kw
5.5kw
7.5kw
11kw
15kw
*1 Applicable to impellers with nominal diameters of 100, 110, 120, 130, 140, 150 and 160.
*2 Applicable to impellers with nominal diameters of 170, 180, 190 and 200.
400 410 350 150 540 800 130 250
480 480 430 170 600 900 150 320
400 430 350 150 540 800 130 250
480 500 430 170 600 900 150 320
400 410 350 150 540 800 130 250
480 480 430 100 600 900 150 320
400 430 350 100 540 800 130 250
480 500 430 120 600 900 150 320
400 430 350 100 540 800 130 250
480 500 430 120 600 900 150 320
80
80
80
100
100
4- 23
4- 23
4- 19
4- 23
4- 23
4- 23
4- 19
32A 50A
32A 50A
40A 65A
40A 65A
50A 80A
95
100
135
145
105
95
100
135
145
110
145
110
φ
φ
φ
φ
φ
φ
φ
B
A
W
a
H
f
h
g
(d)
(e)
c
b