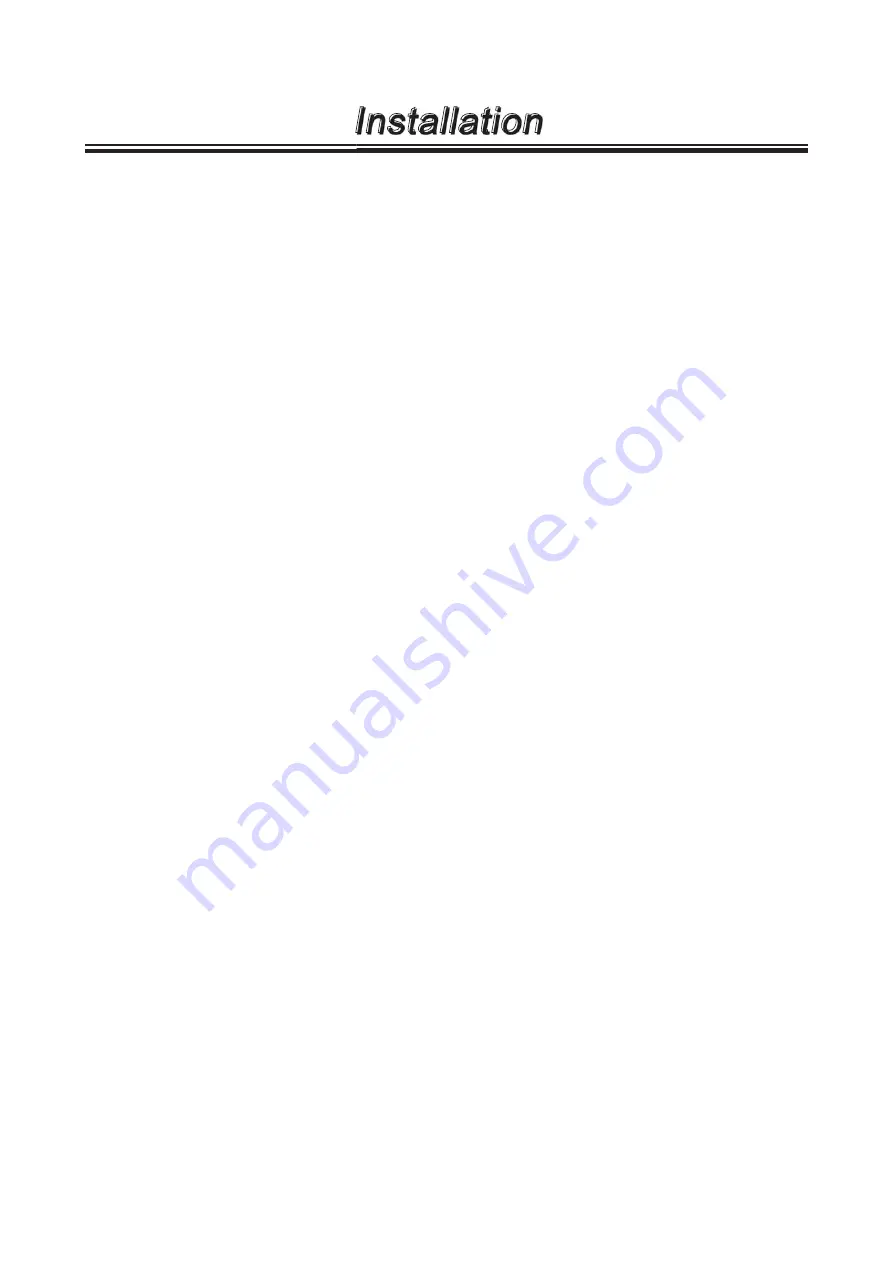
- 18 -
4. Protection equipment
It is recommended to install the following monitoring devices in order to protect the pump.
1. Current sensor/ Power sensor
The sensors monitor the motor load and stop the pump on the detection
of load change, giving an alarm.
2. Pressure sensor
The sensor monitors the starting pressure and stops the pump on the
detection of pressure change, giving an alarm.
3. Flow sensor
The sensor monitors the discharge flow and stops the pump on the
detection of flow change, giving an alarm.
4. Level sensor
The sensor monitors the liquid level in the tank and stops the pump
when it falls below the specified level, giving an alarm.
It is recommended to install two or more monitoring devices. The more monitoring devices, the more pos-
sibility of protecting the pump.
The DR series dry running protector (electric current sensing type) is also available as an option. Contact us
for detail.
Installation
Содержание MXM Series
Страница 6: ...4 Outline 1 Unpacking Inspection 5 2 Model codes 6 3 Operating conditions 7 4 Part names 8...
Страница 15: ...13 Installation 1 Before installation 14 2 Pipework 15 3 Wiring 17 4 Protection equipment 18...
Страница 21: ...19 OPERATION 1 Before operation 20 2 Operation 21 3 Shutdown 22...
Страница 25: ...23 Maintenance 1 Troubleshooting 24 2 Maintenance Inspection 26 3 Disassembly Assembly 29 4 Spare Wear parts 36...
Страница 41: ...39 Maintenance...
Страница 42: ...40...
Страница 43: ...41...