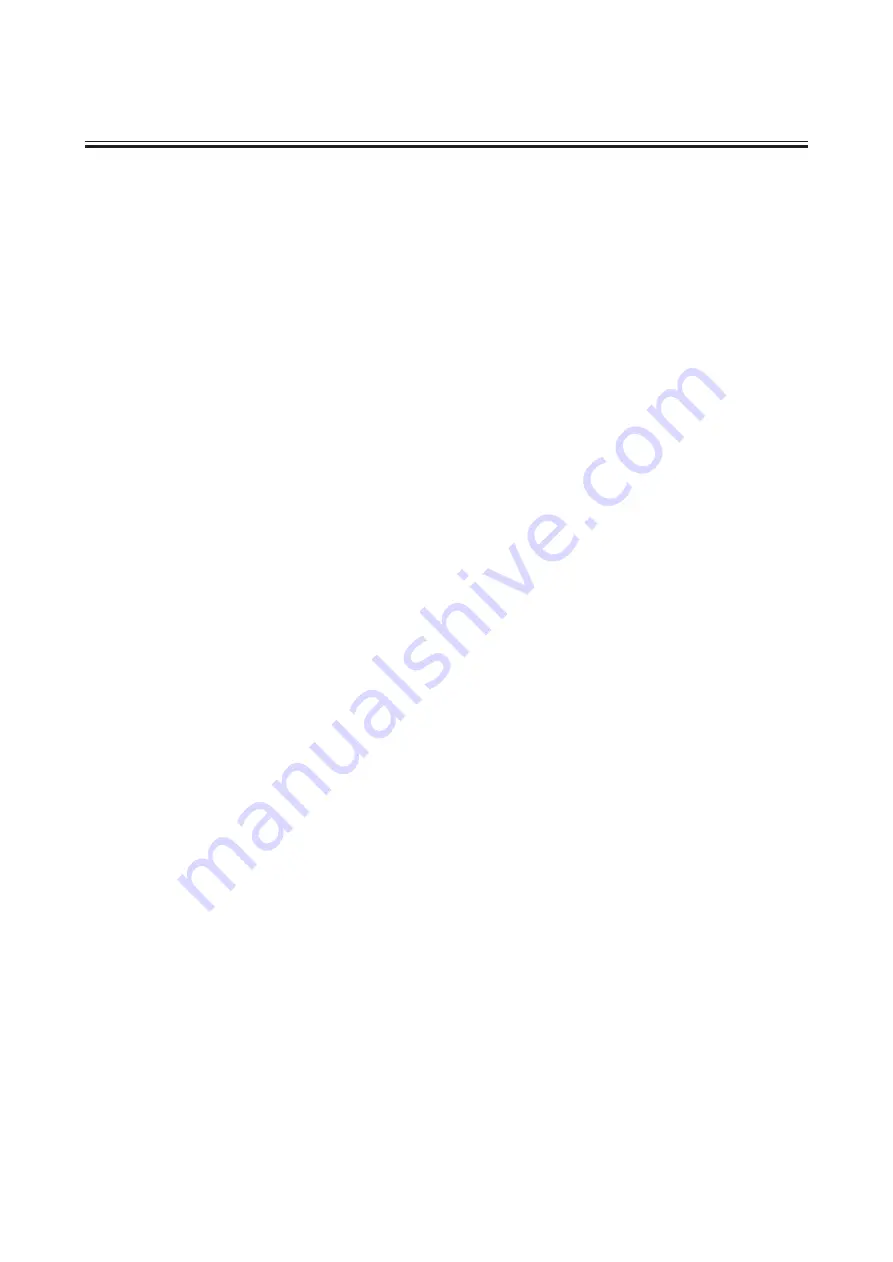
- 13 -
3. Suction piping
(1) Flooded suction
Flooded suction is recommended.
(2) Pipe diameter
Pipe diameter should be larger than pump inlet bore.
(3) Shortest piping
Employ less bends and shortest piping length.
(4) Straight piping
Employ straight pipe just before pump inlet port.
Pump inlet bore 50A or smaller : Straight pipe of 500 mm or longer
Pump inlet bore 65A or larger : Straight pipe of 8 times as larger than inlet port
For the easy pump dismantling and maintenance, install a removable short length pipe of 300mm or so in straight
piping.
(5) Air pocket in piping
Do not allow any projection in piping where air may be trapped along the suction pipe.
Suction pipe should have an ascending gradient of 1/100 toward the pump.
(6) Different diameter of pipes
If diameter of pump suction port is different from that of suction pipe, use the eccentric reducer pipe. Connect the
eccentric reducer pipe so that upper side is level. Residual air may not go out if it is mounted in reverse.
(7) Gate valve in suction side
In case of flooded suction, install gate valve in suction piping. It is needed when the pump is disassembled and
inspected.
(8) Piping for flushing
Install pump flushing piping in case that the dangerous liquid will be handled.
(9) End of suction piping
The end of suction pipe always should be located 500 mm or more below the liquid level. Take care so that air can
not be sucked in suction piping.
(10) In case of suction lift piping
•
The end of suction piping should be 1 to 1.5 times of pipe diameter or more away from the bottom of suction
tank.
•
Install foot valve or check valve in suction piping.
(11) Pipe support
Install the pipe support so that the weight of pipe can not be directly loaded to the pump.
(12) Pipe connection
Pipes must be connected securely so that the air can not be sucked in. If the sealing is not perfect, air is sucked in,
which causes pump damage.