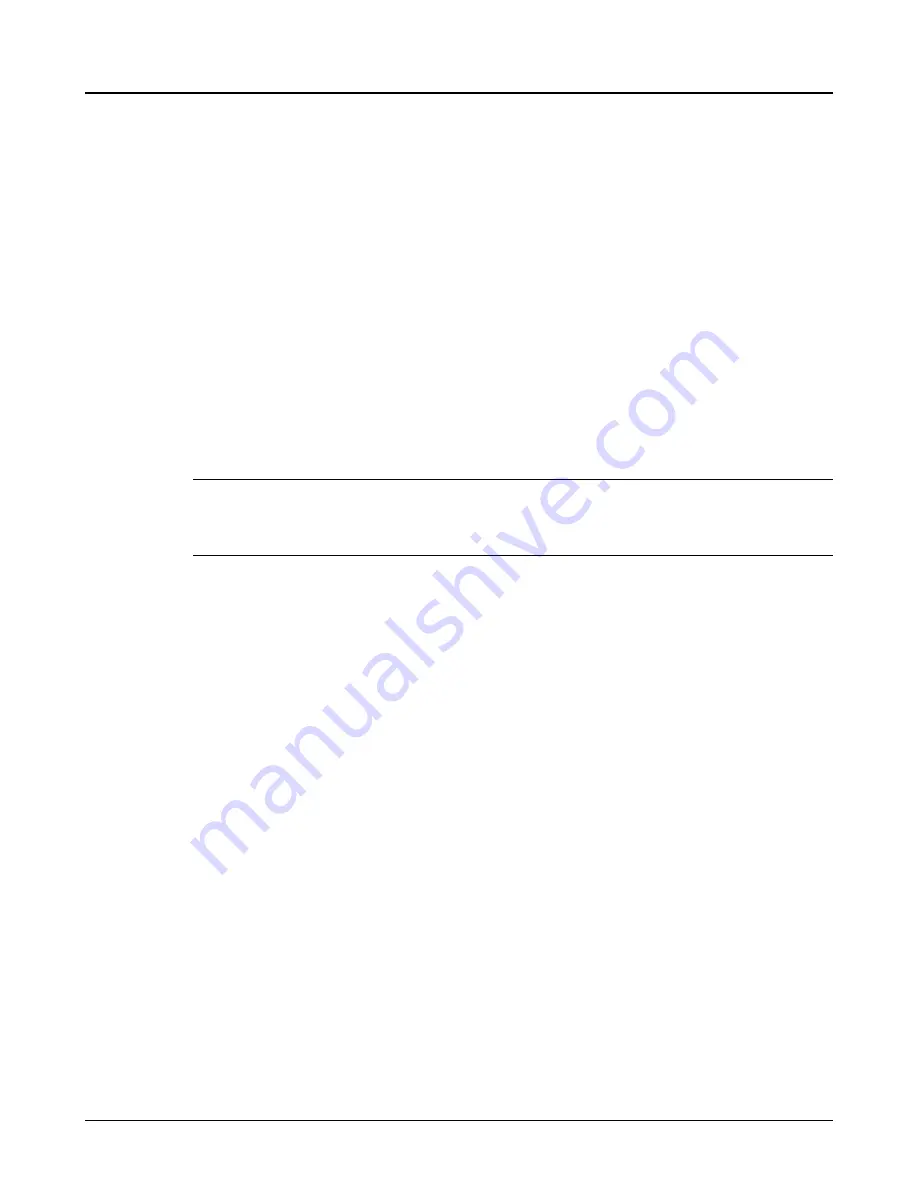
14. Continue adding diffusers and impellers. Shim each impeller to obtain the required front clearance.
15. Install spacer sleeves (157) after last impeller has been installed and its
Front Clearance
is set.
Check space between end of last spacer sleeve (157) and snap ring groove at end of shaft. Add
shims as necessary under the last spacer (157) until end of spacer covers approximately ½ of shaft
retaining ring groove. Enter the shaft retaining ring over the shaft and press it down until it snaps in
the groove.
16. Install O-rings (412K) on the discharge head (152) and diffusers with approximate spacing of every
16 stages for BP20 and every 8 stages for BP40 thru 200.
17.
Slide casing (100) over assembly and screw onto casing adapter (108). O-rings should be lubricat-
ed to aid in assembly.
18. Screw discharge head (152) into casing (100).
19. Replace pump foot (131). Tighten cap screw (371U) finger-tight. Tighten after start-up when pump
has reached operating temperature.
20. Lay pump in horizontal position. Place a heavy bar or pipe through the bearing frame to hold frame.
Do not allow bar to contact stub shaft. The discharge head must be tightened to the following mini-
mum torque values:
BP20
400 ft-lbs.
542 newton-metres
BP40, 70, 100, 200 series
600 ft-lbs.
813 newton-metres
NOTICE:
Operation of pump without proper torque on discharge head (152) can result in damage to the
pump.
21. Plug unused opening in seal housing. Openings are required only for special seals. Refer to seal
drawing for special seals and flushing or cooling requirements.
22. Bolt motor to frame (228 or 228A). For NEMA 444 TCS and 445 TCS motors, an adapter is sup-
plied.
23. Pump is now ready for reinstallation. Follow applicable installation, lubrication and start-up proce-
dures.
7.7 Bearing and seal replacement
1.
Bearing Replacement
a) Lock out power and remove motor from pump.
b) Support liquid end and remove the bearing frame assembly from the pump by removing cap
screws (371L).
c)
Follow instructions for the appropriate bearing frame for removal and replacement of bearings
(See
7.1 Disassembly of pump on page 18
and
7.3 Reassembly of power end on page 19
.
2.
Mechanical Seal Replacement
a) Lock out power and remove motor from pump. Remove bearing frame assembly from pump by
removing cap screws (371L).
b) Access to seal is obtained by removing seal housing (159) and the stationary seat mount (158).
Seal (383A) will then slide off shaft.
c)
Slide new rotary unit over splined end of pump shaft (122) and against retaining ring (361D).
Use care to avoid cutting rubber bellows on spline teeth. On BP20 pumps, the seal shoulders
against the step in the shaft. When reassembling unit, be sure O-rings (412L) are not cut and
that they are seated securely.
d) Refer to mechanical seal drawing for special seal arrangements.
7.7 Bearing and seal replacement
Model 3935 Installation, Operation and Maintenance Instructions
23
Содержание GOULDS PUMPS 3935
Страница 1: ...Installation Operation and Maintenance Instructions Model 3935 ...
Страница 2: ......