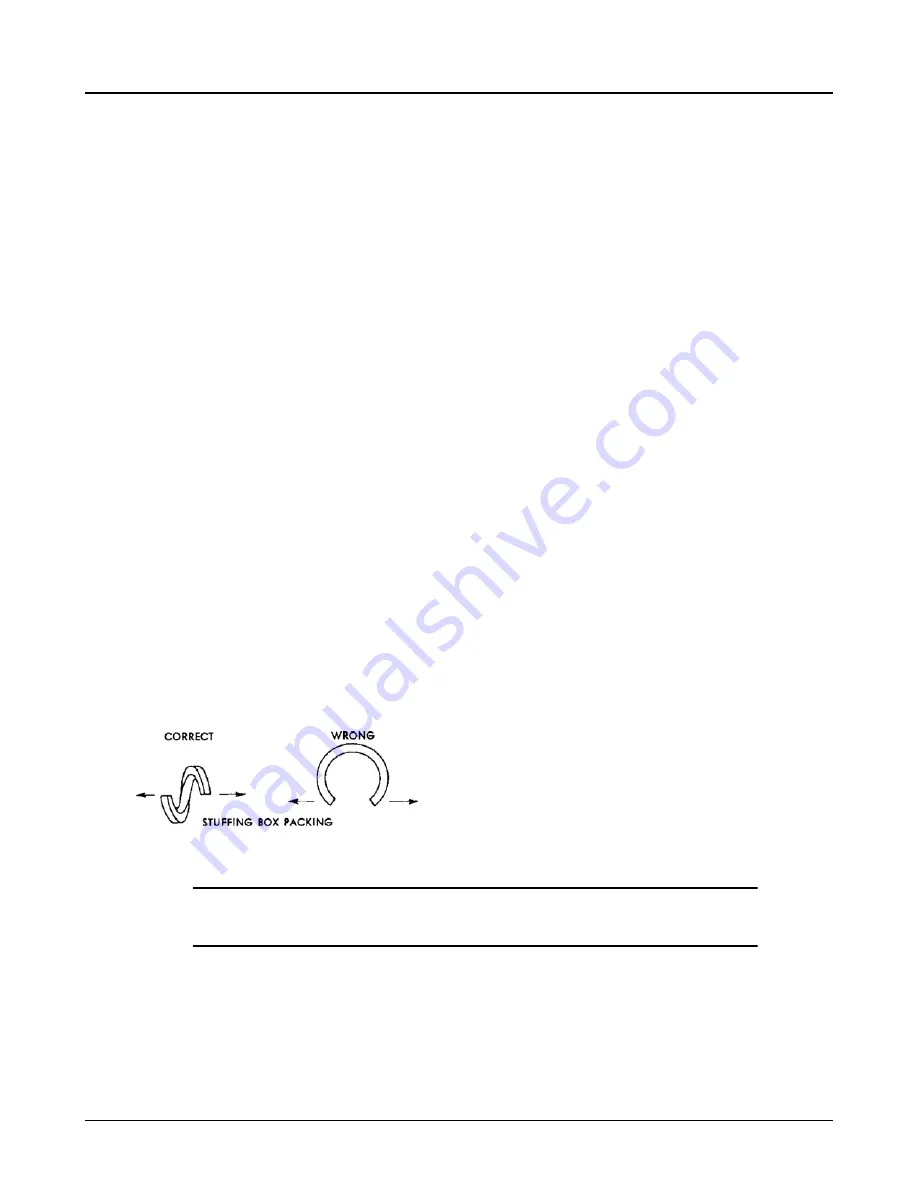
Vertical pump bearings
The bearing above the pump support plate is a ball bearing and is grease lubricated. Follow previous
instructions for grease lubrication.
The pump steady bearings (below the pump support plate) are sleeve type and made of various materi-
als depending upon the application of the pump. Refer to
Close-coupled pumps
Close-coupled pumps contain no pump bearings. The only bearings in the unit are contained within the
motor. Make sure that the motor bearings are properly lubricated. Refer to the motor manufacturer for
instructions.
3.1.1 Driver bearings and coupling
Check to be sure that the driver bearings are properly lubricated. Contact the motor manufacturer for lu-
brication instructions. Refer to coupling instructions supplied separately for coupling lubrication.
3.1.2 Stuffing boxes
Packing
Before packing the stuffing box, make sure box is clean and contains no foreign material. If unit has a
metal lantern ring, assembled with the pump, make sure ring is outside stuffing box.
Stuffing box packing is furnished in the box of fittings which accompanies the pump. When packing the
stuffing box, refer to
10.1 Sectional View and Parts List on page 55
for the arrangement of packing rings
and lantern ring. Depending upon the particular pump and/or application, the lantern ring may be in the
middle or bottom of the stuffing box, incorporated in another part or not used at all.
Some packing rings are die-formed and special care must be taken during installation. To install, twist the
ring sideways just enough to get it around the shaft or sleeve. Do not attempt to pull rings straight out.
See
. Another form of packing ring is tie bulk-type packing which is cut to the proper length.
Each piece should be placed around the shaft or sleeve and the ends of the packing should just meet to
form a smooth, perfect ring. If necessary, the ends should be trimmed to obtain this fit.
There are two basic types of lantern rings, PTFE and metal. Two-piece PTFE lantern rings are supplied
in most units. Install as shown in
.
NOTICE:
Two pieces make one ring. Notches must face one another but need not be aligned.
3.1 Pump Bearings
Model 3415 Installation, Operation, and Maintenance Manual
23