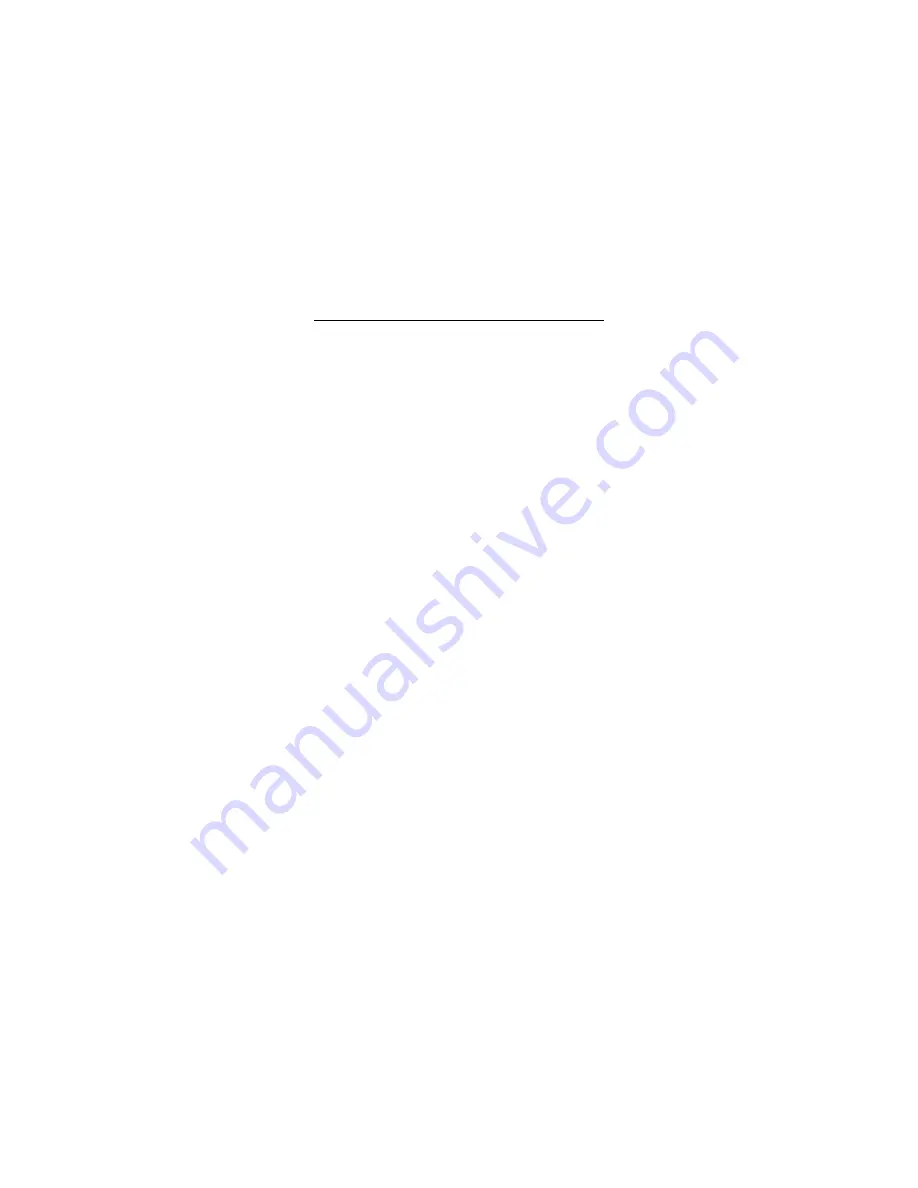
Page 3 of 6
HP400-IOM Rev. 0 7/20
THIS INFORMATION IS SUBJECT TO THE CONTROLS OF THE EXPORT ADMINISTRATION REGULATIONS (EAR). THIS INFORMATION SHALL NOT BE PROVIDED TO
NON-US PERSONS OR TRANSFERRED BY ANY MEANS TO ANY LOCATION OUTSIDE THE UNITED STATES CONTRARY TO THE REQUIREMENTS OF THE EAR.
diameter facing out of the bore. Move the piston sensor in the
bore and make sure the piston sensor is free to move with only
light resistance and the main valve plug and the plug spring will
push the piston sensor back up.
7. Install the retaining ring in the groove in the piston sensor
bore using internal snap ring pliers.
8 Place the range spring backup plate, the range spring, and
the spring button on the piston sensor. Lubricate the center of
the spring button and the large internal threads and chamfer of
the bonnet with Krytox.
9. Screw the bonnet onto the body and tighten it to 50 ft.lbs.
10. Lubricate and install the handwheel assembly onto the
bonnet. The handwheel assembly consists of the handwheel,
the hole plug, the adjusting screw, and the jam nut.
11. Install a filter screen in the inlet port of the body.
Prior to re-installation, the regulator should be connected to a
pressure source with a media compatible with use of the
regulator and pressurized to check for internal and external
leakage and operating characteristics.
Regulator Model Breakdown (CED Code)
Control Engineering Data is intended to provide a single source from which one can determine, in detail, the full scope of the
product line. In addition to the materials of construction, diaphragm and elastomer selection, it also provides all necessary
data regarding adjustment option and range selections. Control Engineering Data also provides a means of communicating
by way of a code number which is fully descriptive in product selection. All catalog numbers received must contain fifteen
(15) characters.
1 through 5
HP400
Pressure Reducing Regulator, Piston Type (Low Flow)
Body / Bonnet / Trim
6
B
Brass / Brass / 300 Stainless Steel
Main Valve Seat(s) / Backup Rings / O-Ring(s)
7 through 8
11
Kel-F / Teflon / Buna-N
12
Vespel / Teflon / Buna-N (See Note 1)
13
Kel-F
/
Buna-N
/
Buna-N
14
Vespel / Buna-N / Buna-N (See Note 1)
17
Vespel / Teflon / Viton (See Note 1)
18
Kel-F / Teflon / Viton (Standard)
9
R
Non-Relieving,
Captured
Bonnet
10 through 11
81
1/4” NPT Connections (See Note 2)
12
P
Panel
Mounting
(2-nut)
(Optional)
S
Plain
bonnet
(No
threads)
(Standard)
13
A
Regulator is cleaned to ITT Conoflow Specification ES8A 01 294
B
Oxygen
Cleaning:
Specification
of
materials in regulators used for oxygen service
is the user’s responsibility. Cleaning for oxygen service to 3500 PSIG
(24.20 MPa) is supplied by ITT Conoflow at no additional cost.
C
Customer
Specified
Cleaning:
Customer to specify the desired level of
cleanliness. ITT Conoflow will advise cost prior to performing cleaning operation.
Specification of materials is the USER’S RESPONSIBILITY.
14
B
Handwheel
(Large)
K
Wrench
knob
with
locking
device
(Optional)
T
“T”
bar
handle
(Optional)
15
J
20-2500
PSI
(0.14-17.25
MPa)
NOTES:
1. The use of the Vespel valve seat increases the inlet pressure rating to 6000 psig
2. Gauge port connections are 1/4” NPT.