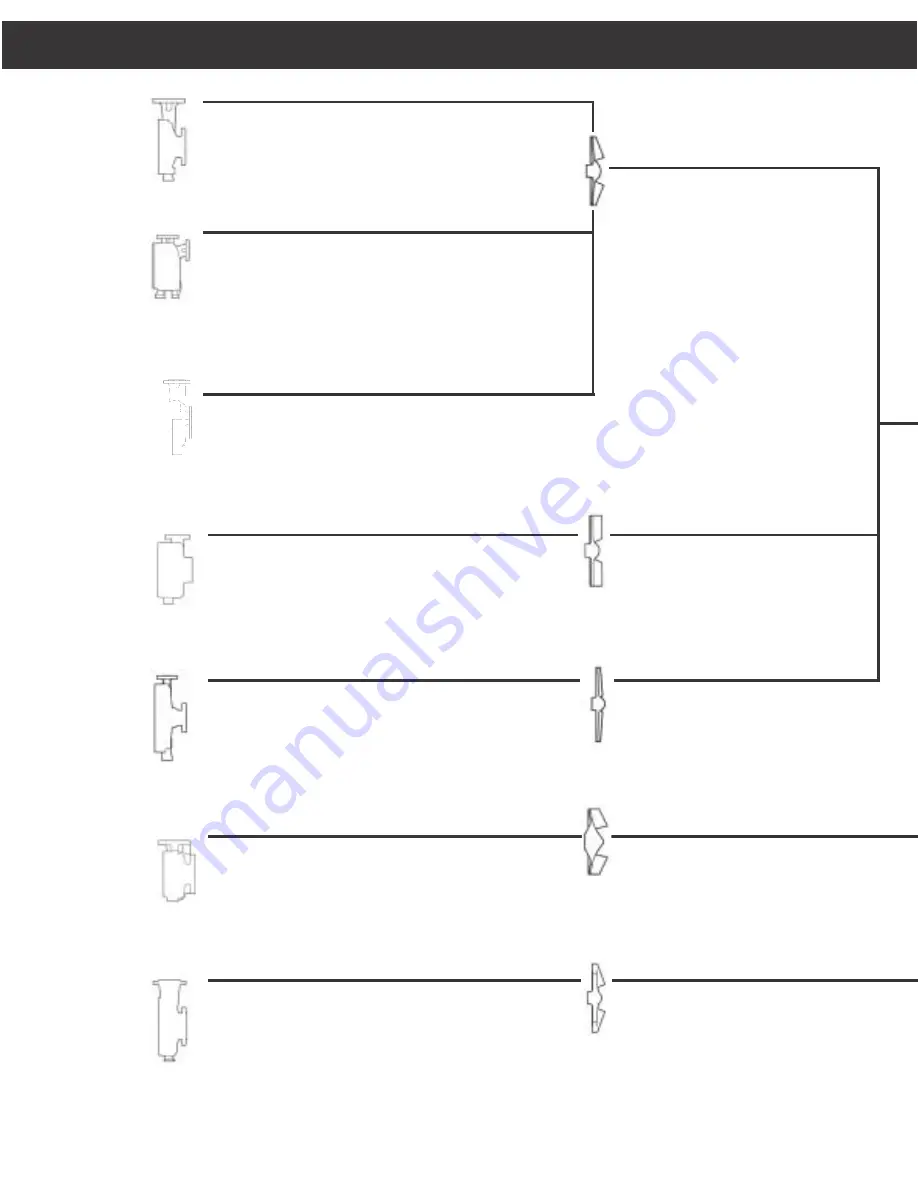
14
ANSIFAM IO
M - 12/03
Model
Casing
Impeller
The casing is top centerline discharge and self-venting.
The gasket is fully confined. An integral foot support is
used for maximum resistance to misalignment and
distortion from piping loads. ANSI flat faced serrated
flanges are standard. ANSI class 150 raised face
serrated, ANSI class 300 flat face serrated, and ANSI
class 300 raised face serrated are available.
The impeller is fully open and threaded to
the shaft. The threads are sealed from
the pumpage by a Teflon
®
O-ring for the
3196 and 3796. The HT 3196 uses a
Graphite O-ring.
3196
The casing is top centerline discharge and self-venting.
It has an integrally cast priming chamber that allows the
pump to evacuate air to prime itself. The gasket is fully
confined. An integral foot support is used for maximum
resistance to misalignment and distortion from piping
loads. ANSI class 150 raised face serrated flanges are
available as an option. The casing comes with a
provision to accept an immersion heater to keep the
liquid in the priming chamber from freezing in outdoor
applications.
3796
The casing is top centerline discharge, self-venting,
and centerline mounted. The casing support is used
for maximum resistance to misalignment and distortion
from thermal piping loads. The centerline mounted
casing maintains vertical alignment at elevated
temperatures. ANSI class 300 raised face serrated
flanges are standard.
HT 3196
The impeller is fully open and recessed
from the casing. It has curved vanes and
is threaded to the shaft. The threads are
sealed from the pumpage by a Teflon
®
O-ring.
CV 3196
The casing is tangential discharge and available with
optional connections for venting, flushing, and solids
cleanout. The gasket is fully confined. An integral foot
support is used for maximum resistance to misalign-
ment and distortion from piping loads. ANSI class 150
flat face serrated flanges are standard on all sizes.
The casing is top centerline discharge and self-venting.
The gasket is fully confined An integral foot support is
used for maximum resistance to misalignment and
distortion from piping loads. ANSI class 150 rasied
face serrated flanges are stanard on 4, 8, and 10”
sizes. ANSI class 300 raised face serrated flange are
standard on the 13” size and optional on 4, 8, and 10”
sizes.
The impeller is fully open with radial
vanes and balance holes. The impeller
is threaded to the shaft and sealed from
the pumpage by a Teflon
®
O-ring.
LF 3196
The casing is top centerline discharge and self-venting.
It is constructed from a fiber reinforced vinylester that is
ribbed for strength. It is sealed using a Viton
®
O-ring
as standard. An integral foot support is used for
maximum resistance to misalignment and distortion
from piping loads. ANSI class 150 flat face flanges are
standard.
The casing is top centerline discharge and self-venting.
The ductile iron casing is lined with PFA Teflon
®
for
corrosion resistance and is offered with ANSI class 150
raised face flanges. The casing gasket is a Teflon
®
envelope with a compressible filler that provides a
positive seal with low bolt torque.
The impeller is fully open and threaded
to the shaft. It is a fiber reinforced
vinylester over a Hastelloy C insert that
provides support and rigidity to the
impeller while securing it to the shaft.
The threads are sealed from the
pumpage by a Teflon
®
O-ring.
The impeller is fully open and threaded to
the shaft. It is constructed of a PFA Teflon
®
covered steel insert. The insert provides
support and rigidity to the impeller while
securing it to the shaft. The threads are
sealed from the pumpage by a Teflon
®
O-ring.
3198
NM 3196
Содержание Goulds Pumps 3196
Страница 1: ...Installation Operation and Maintenance Instructions ANSI FAMILY ...
Страница 4: ...4 ANSIFAM IOM 12 03 ...
Страница 6: ...6 ANSIFAM IOM 12 03 ...
Страница 10: ...10 ANSIFAM IOM 12 03 ...
Страница 12: ...This Page Intentionally Left Blank 12 ANSIFAM IOM 12 03 ...
Страница 28: ...BASEPLATE LEVELING WORKSHEET 28 ANSIFAM IOM 12 03 ...
Страница 44: ...44 ANSIFAM IOM 12 03 ...