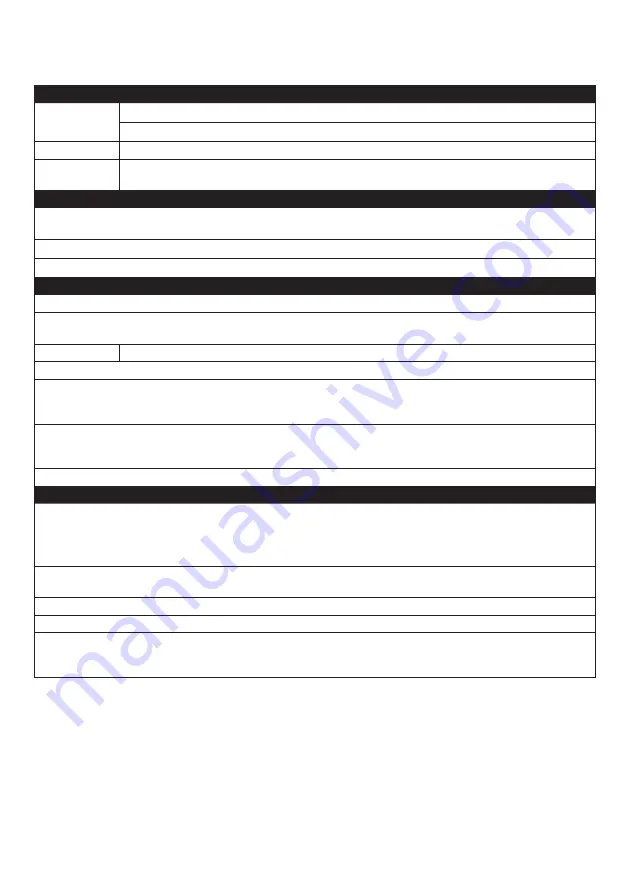
Information for UL Compliance
Optidrive E3 is designed to meet the UL requirements. For an up to date list of UL compliant products, please refer to UL listing
NMMS.E226333. In order to ensure full compliance, the following must be fully observed.
Input Power Supply Requirements
Supply Voltage
200 – 240 RMS Volts for 230 Volt rated units, + /- 10% variation allowed. 240 Volt RMS Maximum.
380 – 480 Volts for 400 Volt rated units, + / - 10% variation allowed, Maximum 500 Volts RMS.
Frequency
50 – 60Hz + / - 5% Variation
Short Circuit
Capacity
All drives are suitable for use on a circuit capable of delivering not more than 100kA maximum short-
circuit Amperes symmetrical with the specified maximum supply voltage when protected by Class J fuses.
Mechanical Installation Requirements
All Optidrive E3 units are intended for installation within controlled environments which meet the condition limits shown in the
Environment section of this Quick Start Guide.
The drive can be operated within an ambient temperature range as stated in the Environment section of this Quick Start Guide.
For IP66 (Nema 4X) units, installation in a pollution degree 2 environment is permissible.
Electrical Installation Requirements
Incoming power supply connection must be according to the Install the Wiring section of this Quick Start Guide.
Suitable power and motor cables should be selected according to the data shown in Rating Tables section of this Quick
Start Guide and the National Electrical Code or other applicable local codes.
Motor Cable
75°C Copper must be used.
Power cable connections and tightening torques are shown in the Mechanical Dimensions section of this Quick Start Guide.
Integral Solid Sate short circuit protection does not provide branch circuit protection. Branch circuit protection must be
provided in accordance with the national electrical code and any additional local codes. Ratings are shown in the Rating
Tables section of this Quick Start Guide.
For Canadian installations transient surge suppression must be installed on the line side of this equipment and shall be rated
480Volt (phase to ground), 480 Volt (phase to phase), suitable for over voltage category iii and shall provide protection for
a rated impulse withstand voltage peak of 2.5kV.
UL Listed ring terminals / lugs must be used for all bus bar and grounding connections.
General Requirements
Optidrive E3 provides motor overload protection, set at 150% of full load, in accordance with the National Electrical Code (US).
Where a motor thermistor is not fitted, or not utilised, Thermal Overload Memory Retention must be enabled by setting P-60 = 1.
Where a motor thermistor is fitted and connected to the drive, connection must be carried out according to the information
shown in the Motor Thermistor Connection section of the Quick Start Guide.
UL rated ingress protection (“Type” ) is only met when cables are installed using a UL recognized bushing or fitting for a
flexible conduit system which meets the required level of protection (“Type”).
For conduit installations the conduit entry holes require standard opening to the required sizes specified per the NEC.
Not intended for installation using rigid conduit system.
WARNING:
The opening of the branch-circuit protective device may be an indication that a fault has been interrupted. To reduce
the risk of fire or electric shock, current-carrying parts and other components of the controller should be examined and replaced if
damaged. If burnout of the current element of an overload relay occurs, the complete overload relay must be replaced.
Control Terminal Wiring
All analog signal cables should be suitably shielded.
Twisted pair cables are recommended.
Power and Control Signal cables should be routed
separately where possible, and must not be routed parallel
to each other.
Signal levels of different voltages e.g. 24 Volt DC and 110
Volt AC, should not be routed in the same cable.
Maximum control terminal tightening torque is 0.5Nm.
Control Cable entry conductor size: 0.05 – 2.5mm2 /
30 – 12 AWG.
Control Terminal Connections
Switched Units:
May use the built in control switch and
potentiometer, or external control signals connected to the
control terminals.
Non-Switched Units:
Require external control signals to
be connected to the control terminals.