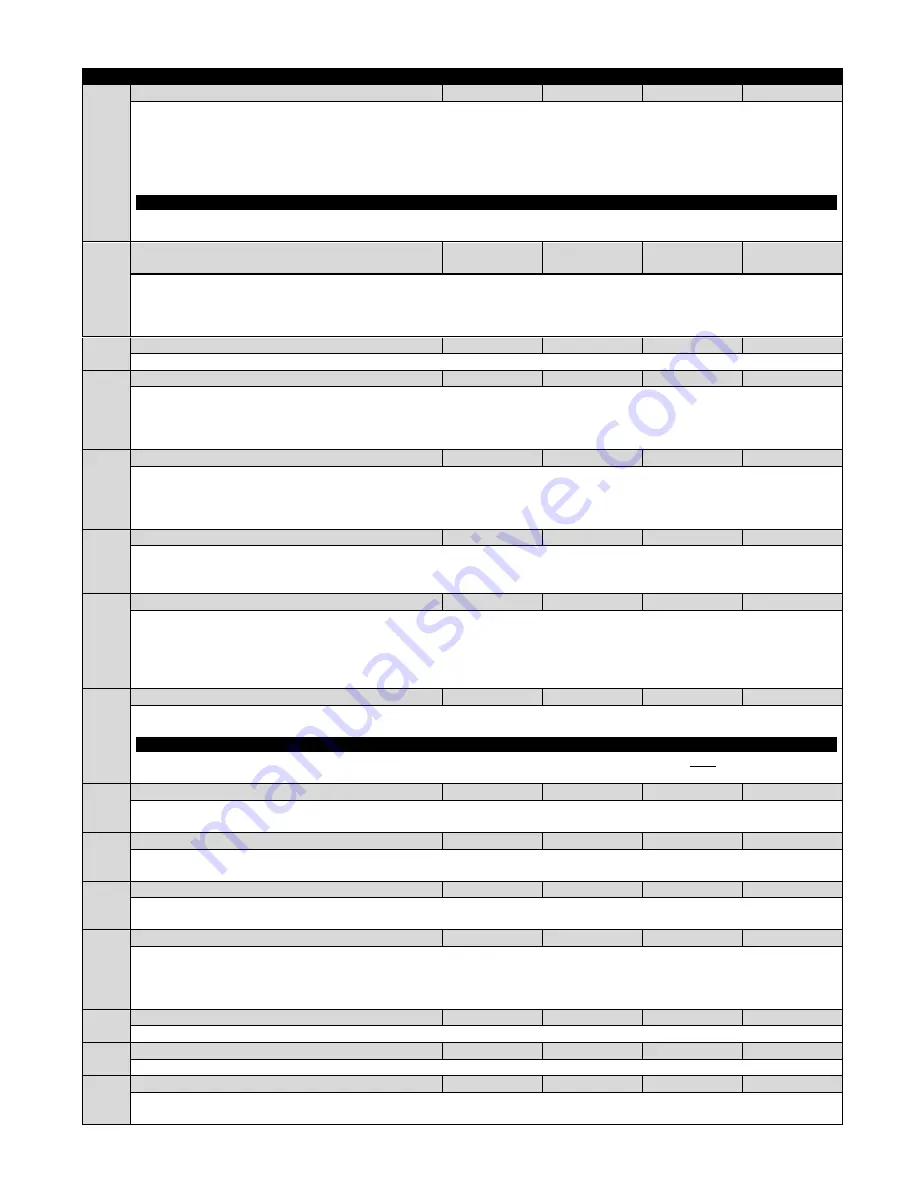
1.3.6.
Parameter Group 6 – Advanced Functions
Par.
Name
Minimum
Maximum
Default
Units
P6-01
Enable Firmware Upgrade
0
3
0
-
Enables the firmware upgrade mode, allowing the User Interface firmware and/or the Power Stage Control firmware to be upgraded.
Options are:
0 : Disabled
1 : Upgrade User Interface and Power Stage Control firmware
2 : Upgrade User Interface firmware only
3 : Upgrade Power Stage Control firmware only
NOTE
This parameter should not be adjusted by the User. The firmware upgrade process is carried out fully automatically using Optitools
Studio PC software.
P6-02
Automatic Thermal Management Minimum Switching
Frequency
10
Model
Dependent
10
kHz
This parameter defines the minimum effective switching frequency which the drive will use.
During operation, the drive measures the power module temperature and will switch automatically to a lower switching frequency if
the temperature reaches a pre-defined limit. This parameter determines the lowest frequency that can be used. In the event that the
power module temperature continues to increase, the drive will trip on over temperature.
P6-03
Auto Reset Time Delay
1
60
20
s
Sets the delay time which will elapse between consecutive drive reset attempts when Auto Reset is enabled in P2-36
P6-04
User Relay Output Hysteresis Control
0.0
25.0
0.3
-
This parameter works in conjunction with P2-11 and P2-13 = 2 or 3 to set a band around the target speed (P2-11 = 2) or zero speed
(P2-11 = 3). When the speed is within this band, the drive is considered to be at target speed or Zero speed. This function is used to
prevent “chatter” on the relay output if the operating speed coincides with the level at which the digital / relay output changes state.
e.g. if P2-13 = 3, P1-01 = 50Hz and P6-04 = 5%, the relay contacts close above 2.5Hz
P6-08
Maximum Speed Reference Frequency
0
20
0
kHz
When the motor speed reference is to be controlled by a frequency input signal (connected to Digital input 3), this parameter is used
to define the input frequency which corresponds to the maximum motor speed (set in P1-01). This maximum frequency that can be
set in this parameter must be in the range 5kHz to 20kHz.
When set to 0, this function is disabled.
P6-10
Enable Function Block Program Operation
0
1
0
-
0 : Function Block Program Disabled.
1 : Function Block Prgram Enabled. This parameter must be set to 1 to enable any Function Block Program loaded into the drive to
operate. When set to 0, the Function Block Program will be disabled.
P6-11
Speed Holding Time on Enable
0
250
0
s
Defines a time period for which the drive will run at Preset Speed 7 (P2-07) when the Enable signal is applied to the drive. The preset
speed can be any value from minimum to maximum frequency and in either direction. This function can be useful in applications
requiring controlled start-up behaviour regardless of the normal system operation, and allows the user to program the drive to always
start at the same frequency, with the same direction of rotation for a specified time period before returning to normal operation.
This function can be used with pumps to provide a reverse spin on start-up to clear any potential blockages.
P6-12
Speed Holding / DC Injection Time on Disable
0
250
0
s
When P6-18 = 0, defines a time period for which the drive will run at Preset Speed 8 (P2-08) following removal of the Enable signal,
before ramping to stop.
Note
Setting this parameter > 0 will result in the drive continuing to operate for the set time at the preset speed after the enable signal has
been removed. It is important to ensure this method of operation is safe prior to using this function.
P6-18
DC Injection Braking Current
0.0
100.0
0.0
%
Defines the DC current level as a percentage of motor rated current (P1-08) that is applied to the motor when a stop command is
received and the DC Injection function is activated.
P6-22
Cooling Fan Runtime Counter Reset
0
1
0
-
0 : No Function
1 : Reset. Setting to 1 resets the internal Fan run-time counter to zero (as displayed in Index 1 of P0-35).
P6-23
Energy Consumption (kWh) Meter Reset
0
1
0
-
0 : No Function
1 : Reset . Setting to 1 resets internal kWh meter to zero (as displayed in Index 1 of P0-26 and Index 1 of P0-27).
P6-24
Maintenance Time Interval
0
60000
0
Hours
Allows the user to define a maintenance interval period for the application. This defines the total number of run time hours which
must elapse before the service indicator is displayed. This may be viewed on the drive OLED display, may be programmed to a relay
output, and also sets a bit in the drive status word.
When P6-25 is set to 1, the internal service interval counter is set to this value
P6-25
Maintenance Time Reset
0
1
0
-
When this parameter is set to 1, the internal service interval counter is set to the value defined in P6-24
P6-26
Analog Output 1 Scaling
0.0
500.0
100.0
%
Defines the scaling factor as a % used for Analog Output 1
P6-27
Analog Output 1 Offset
-500.0
500.0
0.0
%
Defines the offset as a % used for Analog Output 1