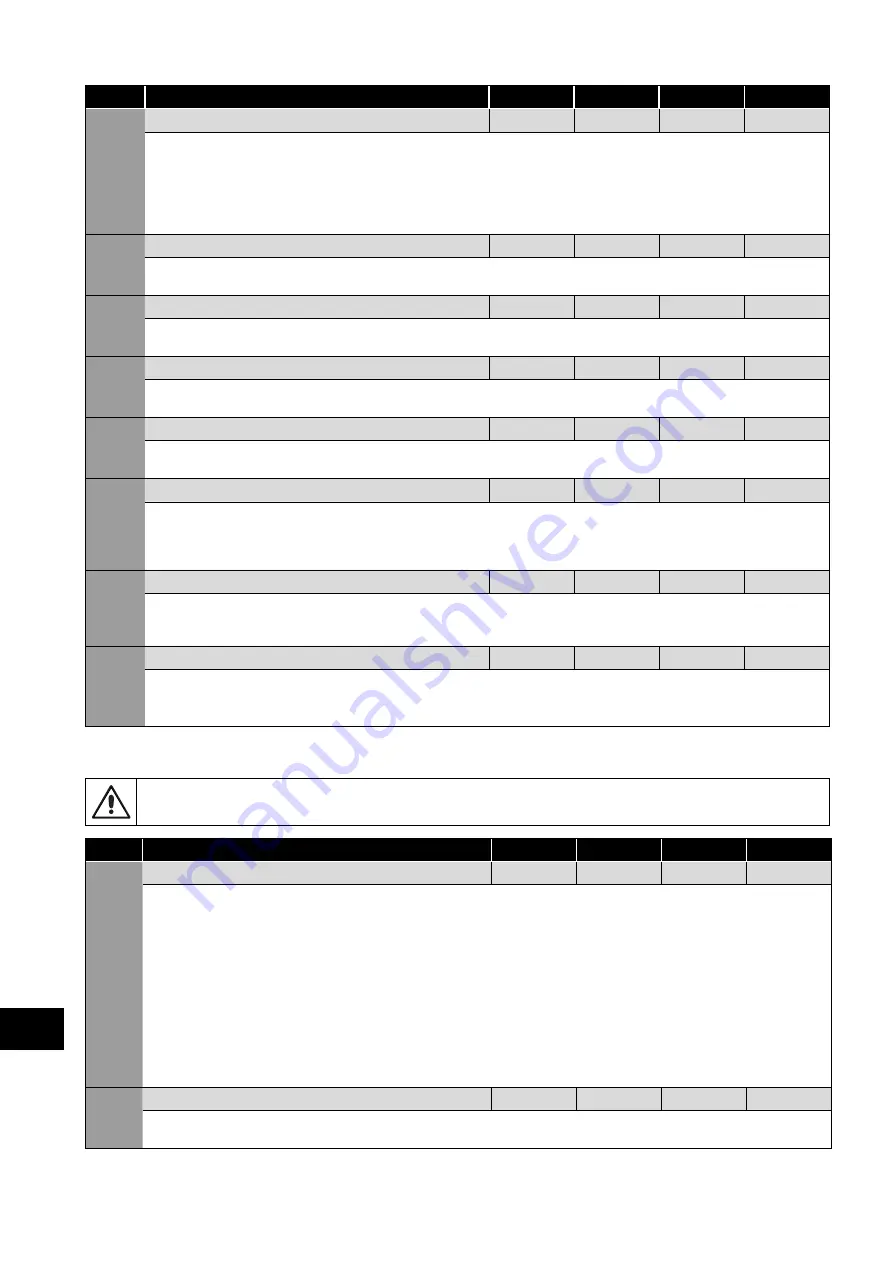
46
| Optidrive Eco User Guide |
Version 3.05
www.invertekdrives.com
Par
Parameter Name
Minimum
Maximum
Default
Units
P3-11
PID Error to Enable Ramp
0.0
25.0
0.0
%
Defines a threshold PID error level, whereby if the difference between the set-point and feedback value is less than the set threshold,
the internal ramp times of the drive are disabled to allow the drive to react quickly to small errors. Where a greater PID error exists, the
ramp times are enabled to limit the rate of change of motor speed.
Setting to 0.0 means that the drive ramps are always enabled. This parameter is intended to allow the user to disable the drive internal
ramps where a fast reaction to the PID control is required, however by only disabling the ramps when a small PID error exists, the risk of
possible over current or over voltage trips being generated are reduced.
P3-12
PID Feedback Display Scaling
0.000
50.000
0.000
-
Applies a scaling factor to the displayed PID feedback, allowing the user to display the actual signal level from a transducer,
e.g. 0 – 10 Bar etc.
P3-13
PID Error Wake Level
0.0
100.0
5.0
%
Sets a programmable PID Error Level whereby if the drive enters standby mode whilst operating under PID control, the difference
between the PID reference and PID feedback signals must exceed this error level to restart the PID controller.
P3-14
Standby Speed Threshold
0.0
P1-01
0.0
Hz / Rpm
Determines the level at which the drive will enter into standby mode. P2-27 must be set with a value (time) for standby function to be
active. Drive enters standby mode if motor speed remains below the level set in P3-14 for the time period set in P2-27.
P3-15
PID Reference 2 Value
0.0
100.0
0.0
%
When P3-05 = 0, and the 2nd digital reference is selected (see section
8.1. Digital Input Configuration Parameter P1-13
) this
parameter sets the preset digital reference (set-point) used for the PID Controller.
P3-16
Pump Prime Time
0
600
0
Seconds
A value other than zero in this parameter will automatically enable the burst pipe detection function. Each time the drive is enabled
whilst in PID control or is switched to PID control, the drive will monitor the PID feedback level for the time entered in P3-16. If the PID
feedback level does not exceed the threshold entered in P3-17 before the time in P3-16 expires then the drive will trip with "Pr-Lo"
(pressure low) trip.
P3-17
Burst Pipe Threshold
0.0
100.0
0.0
%
PID feedback threshold for the burst pipe detection. In direct PID mode, PID feedback should be equal to or greater than this threshold
before the pump prime time (P3-16) expires. In inverse PID mode, PID feedback should be less than or equal to the threshold before
the pump prime time (P3-16) expires.
P3-18
PID Reset Control
0
1
1
-
0 : Continuous Run.
PID loop will continue running as long as P gain (P3-01) is not zero.
1 : On drive Enable.
PID loop will only run when the drive is enabled. If the drive is not running, PID output will reset to 0 (Including
integral result).
9.3. Parameter Group 4 – High Performance Motor Control
Incorrect adjustment of parameters in menu group 4 can cause unexpected behaviour of the motor and any connected
machinery. It is recommended that these parameters are only adjusted by experienced users.
Par
Parameter Name
Minimum
Maximum
Default
Units
P4-01
Motor Control Mode
0
6
0
-
0 : ECO Vector Speed Control - Variable Torque.
Suitable for control of variable torque (centrifugal) fans and pumps with
standard (IM) motors.
1 : ECO Vector Speed Control - Constant Torque.
Constant Torque, suitable for constant torque loads, such as displacement
pumps with standard (IM) motors.
2 : IM Motor, Vector Speed Control.
Control mode for IM Motors.
3 : PM Motor, Vector Speed Control.
Control mode for AC Permanent Magnet Motors.
4 : BLDC Motor, Vector Speed Control.
Control mode for Brushless DC Motors.
5 : Sync RM Motor, Vector Speed Control.
Control mode for Synchronous Reluctance Motors.
6 : LSPM Motor, Vector Speed Control.
Control mode for Line Start Permanent Magnet Motors.
NOTE
Modes 0 and 1 do not require an autotune, although performance may be improved if one is carried out.
Modes 2 and above require an autotune to be completed after the motor parameters are entered.
P4-02 Auto-tune Enable
0
1
0
-
When set to 1, the drive immediately carries out a non-rotating auto-tune to measure the motor parameters for optimum control and
efficiency. Following completion of the auto-tune, the parameter automatically returns to 0.
9
Extended P
arameters