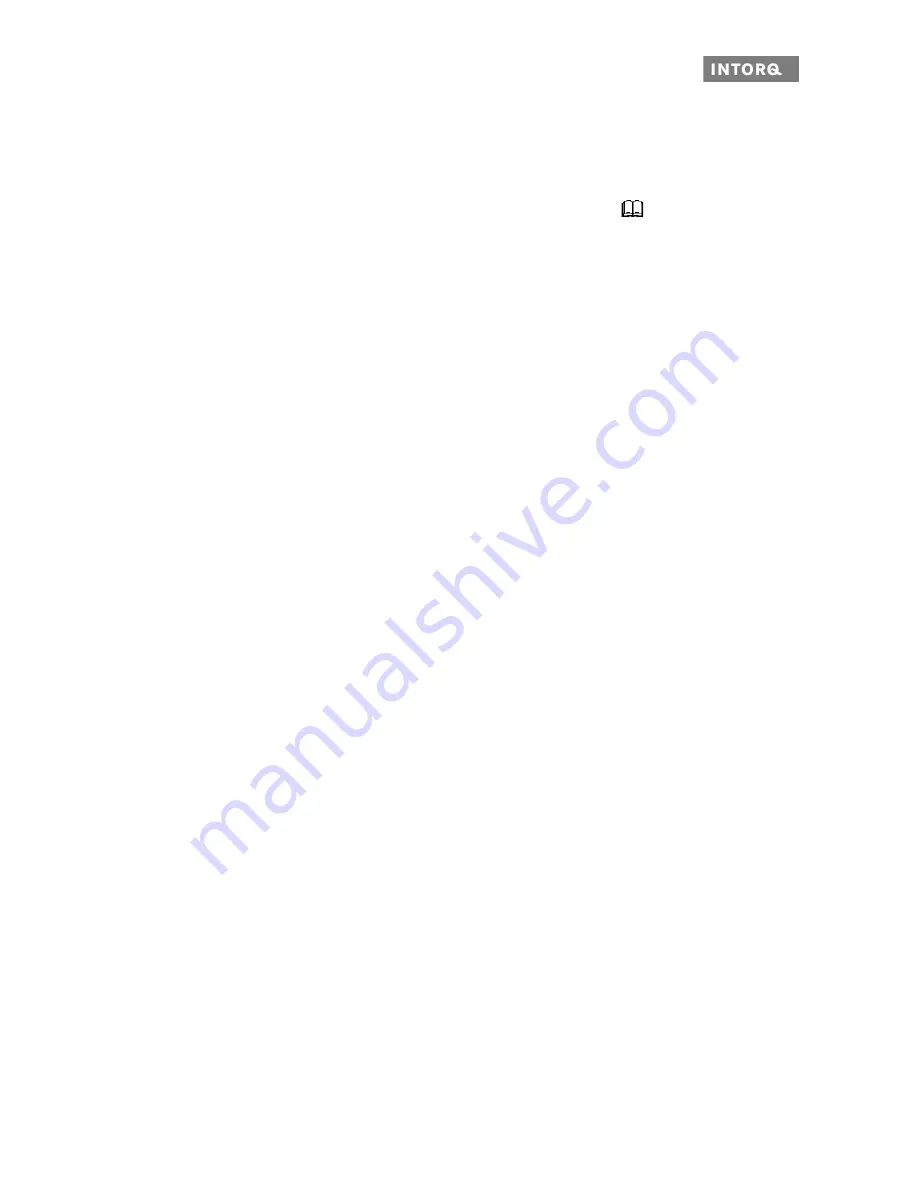
Product description
INTORQ | BA 14.0168 | 09/2015
15
3.3
Optional configuration
3.3.1
Manual release (optional)
To temporarily release the brake when there is no electricity available, a manual release function is available
as an option. The manual release can be retrofitted (for installation refer to
41).
3.3.2
Optional microswitch
The micro-switch is used for the release check or for wear monitoring. The user is responsible for arranging
the electrical connection for this optional microswitch.
❚
Usage for the (air) release check: The motor will start only after the brake has been released. This ena-
bles the microswitch to monitor for errors (e.g. when the motor does not start because of a defective
rectifier, if there are broken connecting cables, defective coils, or an excessive air gap).
❚
Usage for monitoring wear: The brake and motor are supplied with no power when the air gap is too
large.
3.3.3
Optional encapsulated design
This design not only prevents the penetration of spray water and dust, but also the spreading of abrasion
particles outside the brake. This is achieved by the following encapsulation:
❚
A cover ring over the armature plate and rotor.
❚
Cover plate
❚
Shaft seal (can be supplied for continuous shaft).
3.3.4
Optional CCV
The Cold Climate Version (CCV) allows the brake to be operated at lower ambient temperatures.
Содержание BFK458-06***25
Страница 66: ...Notes INTORQ BA 14 0168 09 2015 66 Notes ...
Страница 67: ......