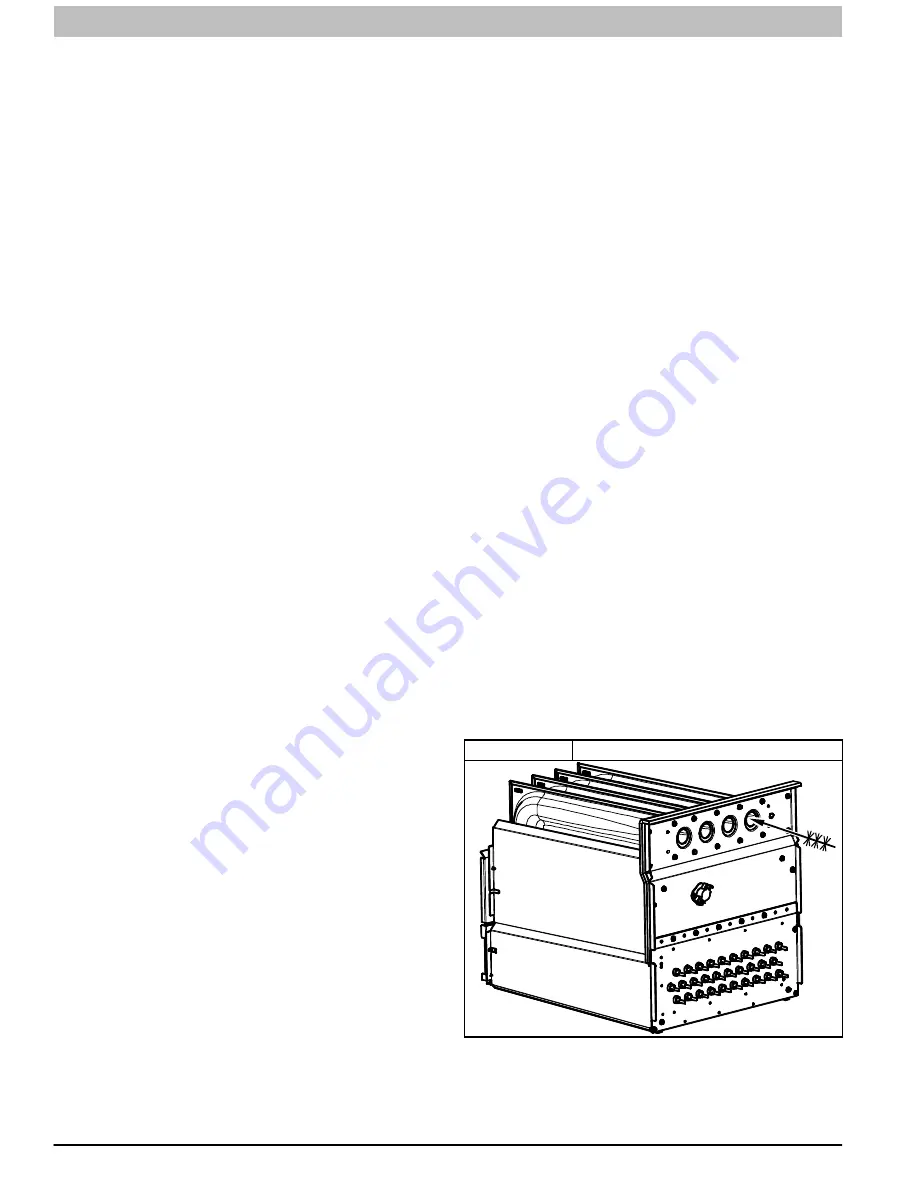
SERVICE AND TECHNICAL SUPPORT MANUAL
Gas Furnace: (F/G)9MXE
Specifications subject to change without notice.
20
440 04 4311 08
NOTE
: Do
NOT
blow into tube with tube connected to the
pressure switch.
9. Clean pressure switch port on collect box with a small
wire. Shake any water out of pressure switch tube.
10. Reconnect tube to pressure switch and pressure switch
port.
11. Remove the relief tube from the port on the collector box
and the trap.
12. Clean the relief port on collect box and the trap with a
small wire. Shake any water out of the tube.
13. Reconnect relief tube to trap and collector box ports.
Cleaning Condensate Drain and Trap
NOTE
: If the condensate trap is removed, a new gasket
between the trap and collector box is required. Verify a
condensate trap gasket is included in the service kit or obtain
one from your local distributor.
1. Disconnect power at external disconnect, fuse or circuit
breaker.
2. Turn off gas at external shut-off or gas meter.
3. Remove control door and set aside.
4. Turn electric switch on gas valve to OFF.
5. Disconnect external drain from condensate drain elbow
or drain extension pipe inside the furnace and set aside.
6. Disconnect the condensate trap relief hose from collector
box port and condensate trap.
NOTE
: If condensate has a heat pad attached to the trap,
trace the wires for the pad back to the connection point and
disconnect the wires for the heat pad.
7. Remove the screw that secures the condensate trap to
the collector box, remove the trap and set aside.
8. Remove the trap gasket from the collector box if it did not
come off when the trap was removed.
9. Discard the old trap gasket.
10. Rinse condensate trap in warm water until trap is clean.
11. Flush condensate drain lines with warm water.
Remember to check and clean the relief port on the
collector box.
12. Shake trap dry.
13. Clean port on collector box with a small wire.
To re-install Condensate Drain and Trap:
1. Remove adhesive backing from condensate trap gasket
2. Install gasket on collector box
3. Align the condensate trap with the drain opening on the
collector box and secure the trap with the screw
4. Attach the relief hose to the relief port on the condensate
trap and collector box.
5. Secure tubing to prevent any sags or traps in the tubing.
6. Connect condensate drain elbow or drain extension
elbow to the condensate trap
7. Connect the leads of the condensate heat pad (if used)
8. Connect external drain piping to the condensate drain
elbow or drain extension pipe.
9. Turn gas on at electric switch on gas valve and at
external shut-off or meter
10. Turn power on at external disconnect, fuse or circuit
breaker.
11. Run the furnace through two complete heating cycles to
check for proper operation
12. Install control door when complete.
Checking Heat Pad Operation (If Applicable)
In applications where the ambient temperature around the
furnace is 32
_
F (0
_
C) or lower, freeze protection measures are
required. If this application is where heat tape has been
applied, check to ensure it will operate when low temperatures
are present.
NOTE
: The Heat Pad, when used, should be wrapped around
the condensate drain trap. There is no need to use heat tape
within the furnace casing. Most heat tapes are temperature
activated, and it is not practical to verify the actual heating of
the tape. Check the following:
1. Check for signs of physical damage to heat tape such as
nicks, cuts, abrasions, gnawing by animals, etc.
2. Check for discolored heat tape insulation. If any damage
or discolored insulation is evident, replace heat tape.
3. Check that heat tape power supply circuit is on.
Cleaning Heat Exchangers
The following items must be performed by a qualified service
technician.
Primary Heat Exchangers
If the heat exchangers get an accumulation of light dirt or dust
on the inside, they may be cleaned by the following procedure:
NOTE
: If the heat exchangers get a heavy accumulation of
soot and carbon, both the primary and secondary heat
exchangers should be replaced rather than trying to clean them
thoroughly due to their intricate design. A build
−
up of soot and
carbon indicates that a problem exists which needs to be
corrected, such as improper adjustment of manifold pressure,
insufficient or poor quality combustion air, improper vent
termination, incorrect size or damaged manifold orifice(s),
improper gas, or a restricted heat exchanger (primary or
secondary). Action must be taken to correct the problem.
1. Turn off gas and electrical supplies to furnace.
2. Remove control door.
3. Disconnect wires or connectors to flame rollout switch,
gas valve, igniter, and flame sensor.
4. Using backup wrench, disconnect gas supply pipe from
furnace gas control valve.
5. Remove two screws attaching top filler plate and rotate
upwards to gain access to screws attaching burner
assembly to cell panel.
6. Remove screws attaching burner assembly to cell panel.
(See
Figure 9
)
NOTE
: Burner cover, manifold, gas valve, and burner
assembly should be removed as one assembly.
7. Clean heat exchanger openings with a vacuum and a
soft brush. (See
Figure 12
)
Figure 12
Cleaning Heat Exchanger Cell
NOTE
: After cleaning, inspect the heat exchangers to ensure
they are free of all foreign objects that may restrict flow of
combustion products.