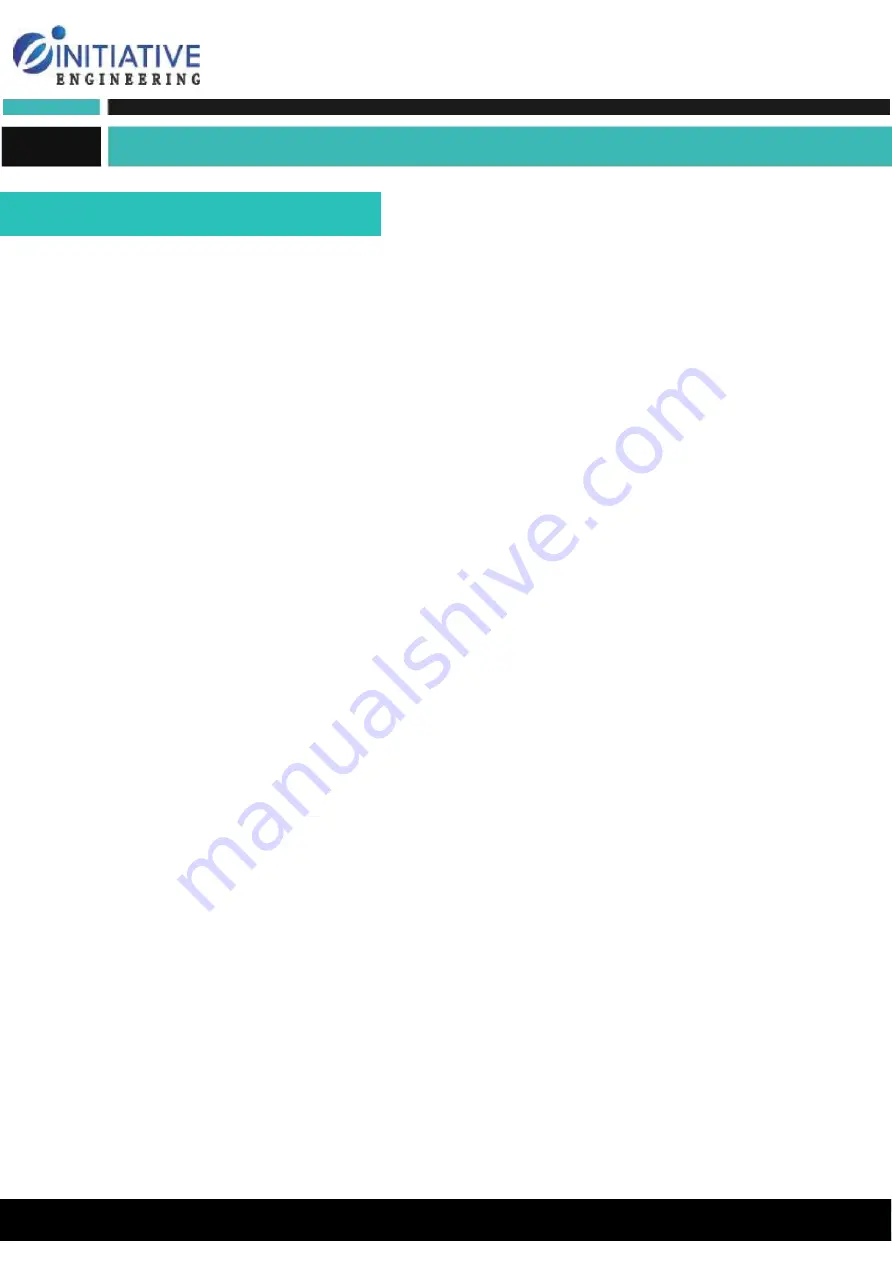
Essential Safety Requirement
Install the pump in any shaded place away from direct sunlight.
The pump can not be used fin sub-merged condition.
Before starting work on the pump, the pump must be disconnected from the power supply. The
system must be pressure less!
Make sure that any chemicals that are released from the pump or any damaged lines do not causes
damages to system parts.
Before switching on the main supply, the tubing cap (both suction and discharge valve assembly)
should be tightened to dosing head properly so that the metering liquid can not spray out from the
dosing head in working condition and put operator’s in risk. The dosing medium/liquid is pressurized
and can be harmful to health and the environment.
When working with chemicals, the accident pretension regulations applicable at the installation site
should be applied (e.g. wearing protection clothing's). Observe the chemical manufacturer's safety
data sheet and safety instructions when handling chemicals.
The dosing medium must be a liquid, Observe the freezing and boiling point of the dosing media.The
resistance of the parts which comes into contact with the dosing medium, such as the dosing head,
PTFE ball and washer, glass ball, ‘O’ ring, ball bush, pipe lines, ball seal and suction filter assembly,
NRV body etc. , depends on the medium, media temperature and operating pressure. Ensure that the
parts come contact with the dosing medium are resistance to the dosing medium under operating
temperature and pressure, see the data booklet.
Ensure voltage is within range specified for the pump i.e., 230±20% V
Electrical connection should be made between Live – Neutral and Not live-Ground
Avoid giving supply from the same line as heavy electrical equipment.
Do not operate the pump with a damage/break diaphragm. Operating with damaged diaphragm can
lead to dosing liquid entering pump housing. In case of diaphragm breakage immediately separate
the pump from the power supply. Make sure the pump cannot be put back into the operation by
accident. In case of diaphragm breakage use the following step to dismantle diaphragm (refer fig of
Edose and Edose Neo Dosing Head overview):
1.
Make the system pressure less
2.
Empty the dosing head before maintenance and flush it, if necessary
3.
Set the frequency knob to 0%.
4.
Switch off mains supply.
5.
Take suitable steps to ensure that the returning liquid is safely collected.
6.
Dismantle the suction and discharge tubing and check whether tubing is blocked, soiled or
damaged. Replace if necessary
7.
Dismantle NRV body in suction and discharge side.
8.
Remove the ball bush and o ring from NRV body. Check their safety for wear and damage. If
necessary, replace them.
9.
Unscrew the PCB housing and remove it.
10.
Remove the spring fitting washer and nut and PTFE washer.
11.
Loosen the screws on dosing head and remove the screws.
12.
Remove the diaphragm washer, plunger washer and diaphragm o ring from diaphragm-
plunger assembly.
13.
Dismantle the diaphragm-plunger assembly
14.
Check the diaphragm. If necessary, replace it.