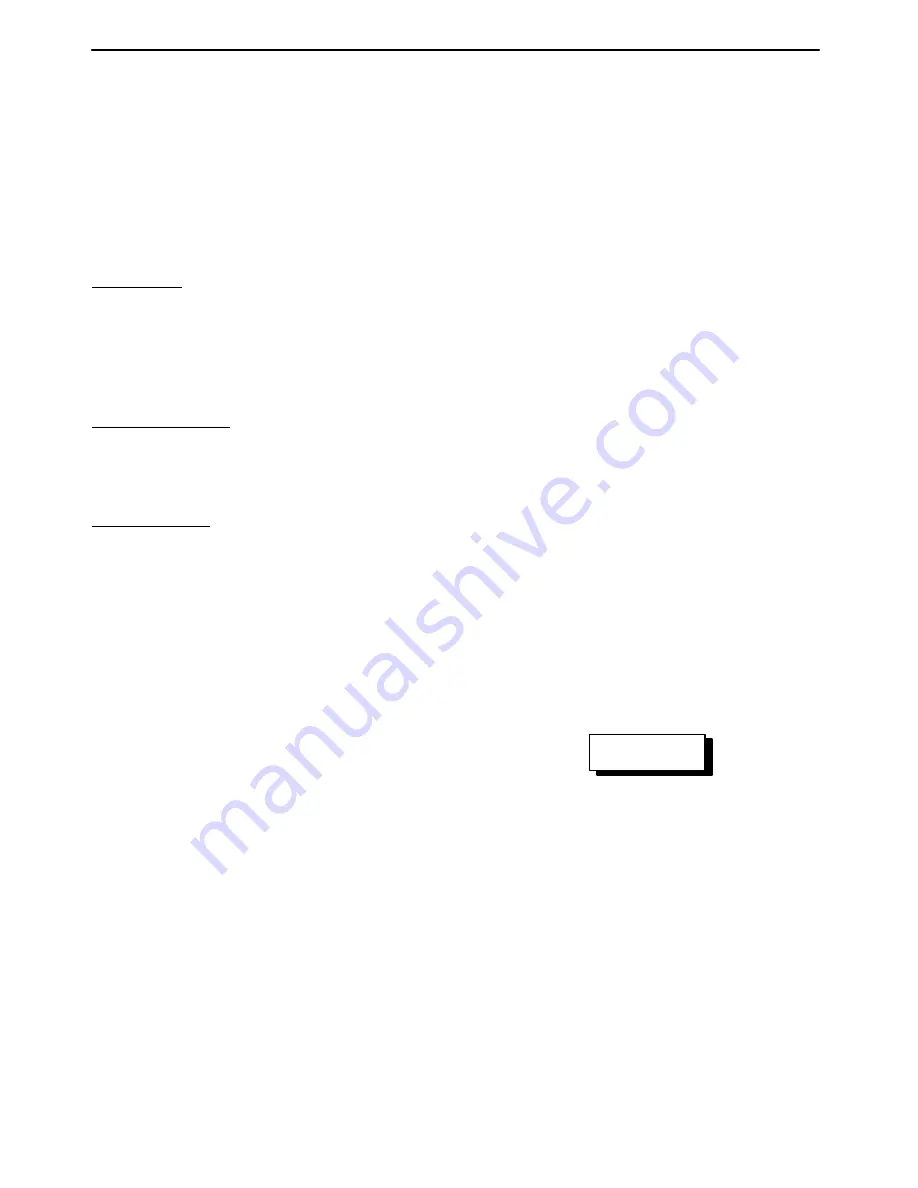
39
( )
Book: 22305593 (8/03)
4. Lubricate the new filter gasket with the same oil
being used in the machine.
5. Install new filter by turning element clockwise until
gasket makes initial contact. Tighten an additional 1/2
to 3/4 turn.
6. Start unit and allow to build up to rated pressure.
Check for leaks before placing unit back into service.
FASTENERS
Visually check entire unit in regard to bolts, nuts and
screws being properly secured. Spot check several
capscrews and nuts for proper torque. If any are found
loose, a more thorough inspection must be made.
Take corrective action.
COMPRESSOR OIL
The lubricating and cooling oil must be replaced every
500 hours of operation or six (6) months, whichever
comes first.
RUNNING GEAR
Every month or 500 miles, tighten the wheel lug nuts to
85 -- 95 lbs.--ft. Every six months the wheel bearings,
grease seals and axle spindles should be inspected
for damage (corrosion, etc.) or excessive wear.
Replace any damaged or worn parts. Repack wheel
bearings. Use a wheel bearing grease conforming to
specification MIL--G--10924 and suitable for all
ambient temperatures.
Grease can be replaced in a wheel bearing using a
special fixture or by hand as follows.
Before installing bearing, place a light coat of grease
on the bearing cups which are pressed in the hub.
Place a spoonful of grease in the palm of one hand and
take the bearing in the other hand. Push a segment of
the wider end of the bearing down into the outer edge
of the grease pile closest to the thumb. Keep lifting and
pushing the bearing down into the edge of the grease
pile until grease oozes out both from the top and from
between the rollers. Then rotate the bearing to repeat
this operation on the next segment. Keep doing this
until you have the entire bearing completely filled with
grease.
Excessive grease in the hub or grease cap serves no
purpose due to the fact that there is no way to force the
grease into the bearing. The manufacturer’s standard
procedure is to thoroughly pack the inner and outer
bearing with grease and then to apply only a very small
amount of grease into the grease cap.
If bearing adjustment is required or the hub has been
removed for any reason, the following procedure must
be followed to ensure a correct bearing adjustment of
0.001 to .012 free play.
1.
While rotating hub slowly to seat the bearings,
tighten spindle nut to approximately 15 lbs.--ft.
Grasp the tire at the top and bottom and rock, in
and out. There should be no evidence of
looseness (free play) at the bearing.
2.
Loosen nut to remove preload torque. Do not
rotate hub.
3.
Finger tighten nut until just snug. Loosen nut
until the first nut castellation lines up with cotter
pin hole in spindle. Insert cotter pin.
4.
Ensure a definite but minimal amount of free
play by rocking the tire.
6.
Nut should be free to move with only restraint
being the cotter pin.
RECEIVER--SEPARATOR SYSTEMS
WARNING
High pressure air can cause severe injury or death
from hot oil and flying parts. Always relieve
pressure before removing caps, plugs, covers or
other parts from pressurized air system.
S
Open service valve at end of machine.
S
Ensure pressure is relieved, with BOTH:
-- Discharge air pressure gauge reads zero (0).
-- No air discharging from service valve.
S
When draining oil, remove plug from bottom of
separator tank.
S
When adding oil, remove and replace (make tight)
plug on side of separator tank.
Содержание P185WIR
Страница 69: ...SECTION 11 PARTS LIST...
Страница 70: ......
Страница 71: ......
Страница 72: ......
Страница 73: ......
Страница 74: ......
Страница 75: ......
Страница 76: ......
Страница 77: ......
Страница 78: ......
Страница 79: ......
Страница 80: ......
Страница 81: ......
Страница 82: ......
Страница 83: ......
Страница 84: ......
Страница 85: ......
Страница 86: ......
Страница 87: ......
Страница 88: ......
Страница 89: ......
Страница 90: ......
Страница 91: ......
Страница 92: ......
Страница 93: ......
Страница 94: ......
Страница 95: ......
Страница 96: ......
Страница 97: ......
Страница 98: ......
Страница 99: ......
Страница 100: ......
Страница 101: ......
Страница 102: ......
Страница 103: ......
Страница 104: ......
Страница 105: ......
Страница 106: ......
Страница 107: ......
Страница 108: ......
Страница 109: ......
Страница 110: ......
Страница 111: ......
Страница 112: ......
Страница 113: ......
Страница 114: ......
Страница 115: ......
Страница 116: ......
Страница 117: ......
Страница 118: ......
Страница 119: ......