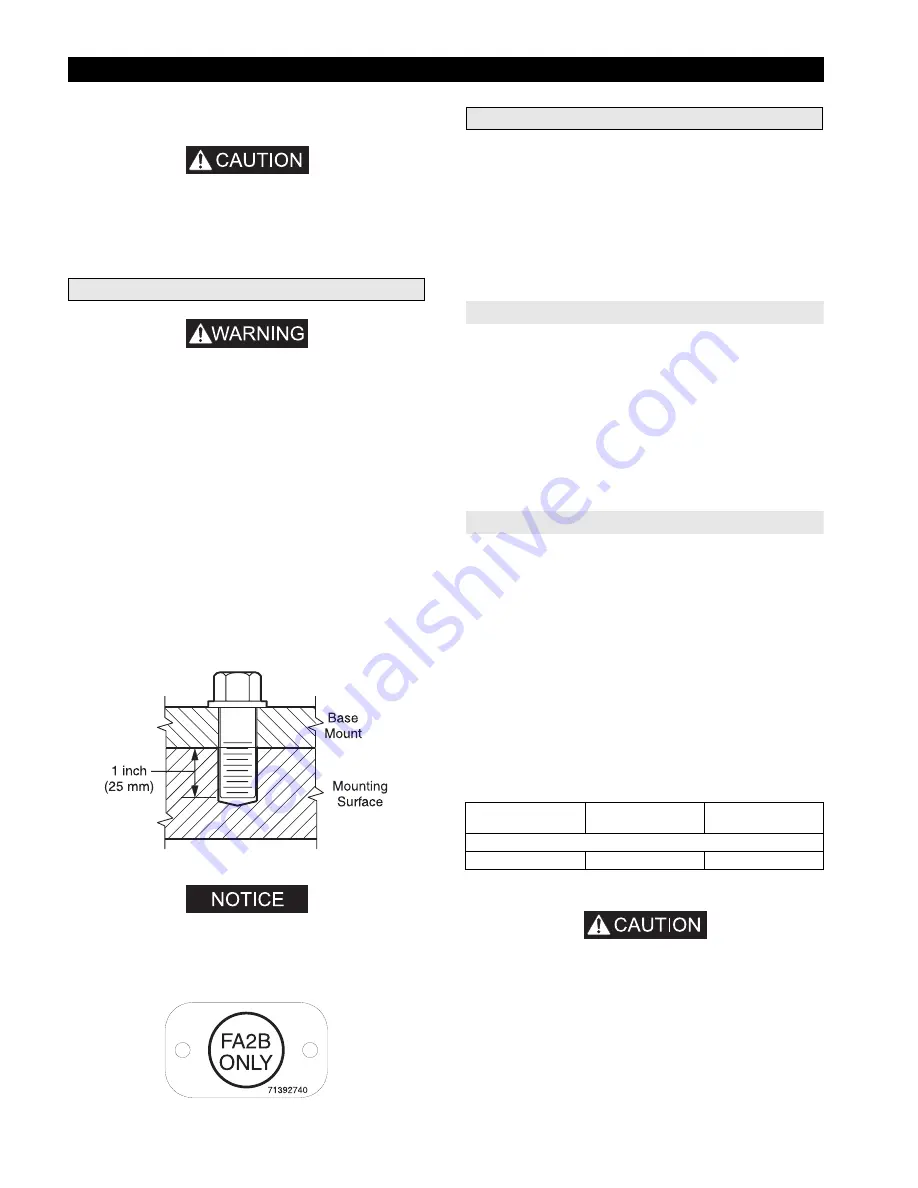
6
MHD56208 - Edition 3
INSTALLATION
Prior to installing the motor, carefully inspect it for possible
shipping damage.
• Owners and users are advised to examine specific, local or
other regulations, including American National Standards
Institute and/or OSHA Regulations which may apply to a
particular type of use of this product before installing or
putting motor to use.
Mounting
• Use motor eyebolt only when lifting motor. Motor eyebolt is
designed to hold only weight of motor.
The
MMP150
air motor may be mounted in any orientation. The
lubrication free design removes any consideration for maintaining
an oil sump or vent cap orientation. However; if using a motor
mounted control valve operator safety and ease of operation
should be considered.
Base Mounted Installation:
1.
Surface must be flat and of sufficient strength to handle the
motor and any components attached or connected to it.
2.
Mounting bolts must be 3/4 inch (18 mm) Grade 8 or better.
If mounting surface is threaded the minimum depth of thread
engagement should be 1 inch (25 mm). Refer to Dwg.
MHP2019 on page 6. For mounting into drilled holes, use
self-locking nuts and lockwashers to secure fasteners.
3.
Refer to Dwg. MHP2004 on page 5 for bolt hole location
dimensions.
(Dwg. MHP2019)
• Control valves supplied with motors will have label 71392740
attached. Label is only applicable if motor is used in an
Ingersoll Rand winch application. Refer to Dwg. MHP2335 on
page 6.
(Dwg. MHP2335)
Air Supply
The air supply should be clean and filtered to ensure optimum
motor performance and minimize wear. Foreign particles are the
primary cause of motor wear and breakdown. Using an air filter
will improve overall motor performance and reduce unscheduled
downtime.
Maximum air consumption is 425 scfm (12 cu. m/min) at rated
operating pressure of 90 psig (6.3 bar/630 kPa) at the motor inlet.
If air supply varies from recommended, motor performance will
change. Refer to ‘Performance Graphs’ on page 4.
Air Lines
The inside diameter of motor air supply lines must be at least
1-1/4 inch (32 mm) to achieve maximum performance. Use of
smaller diameter lines will result in reduced performance (lower
speeds). Before making final connections, all air supply lines
should be purged with clean, moisture-free air or nitrogen before
connecting to motor inlet. Supply lines should be as short and
straight as installation conditions permit. Long transmission lines
and excessive use of fittings, elbows, tees, globe valves etc. cause
a reduction in pressure due to restrictions and surface friction in
the lines.
Air Line Lubricator
Refer to Dwg. MHP0191 on page 7.
An air line lubricator is not required with the
MMP150
air motor
when supplying air source is either a portable compressor or air
compressor system without an air dryer or coalescing filter located
between the compressor and motor. However, using an air line
lubricator will extend piston ring life.
The lubricator must have an inlet and outlet at least as large as the
inlet on the motor directional control valve. Install air line
lubricator as close to air inlet on motor as possible.
Air Spring Operation
Air motors are often used as ‘Air Springs’. This refers to operating
the motor against normal motor rotation. When used for this
purpose an ‘Air Line Lubricator’ is required.
Lubricator Settings
• Shut off air supply before filling air line lubricator, if
equipped.
If equipped, the airline lubricator should be replenished daily with
ISO VG 32 (10W SAE) oil. Refer to “Lubricator Settings” on
page 6.
For optimum performance and maximum parts durability, provide
a lubricated air supply. The air motor should be installed as near as
possible to the compressor or air receiver. Recommended
pressures and volumes are measured at the point of entry to the air
motor directional control valve.
Without
Lubricator
With
Lubricator
Air Spring
Operation
(drops per minute)
0
3-6
6-8
Do not exceed values stated.
Содержание MMP150
Страница 5: ...MHD56208 Edition 3 5 Dwg MHP2004...
Страница 23: ...MHD56208 Edition 3 23 SERVICE NOTES...
Страница 26: ...26 MHD56208 Edition 3 SERVICE NOTES...
Страница 36: ...www irtools com...