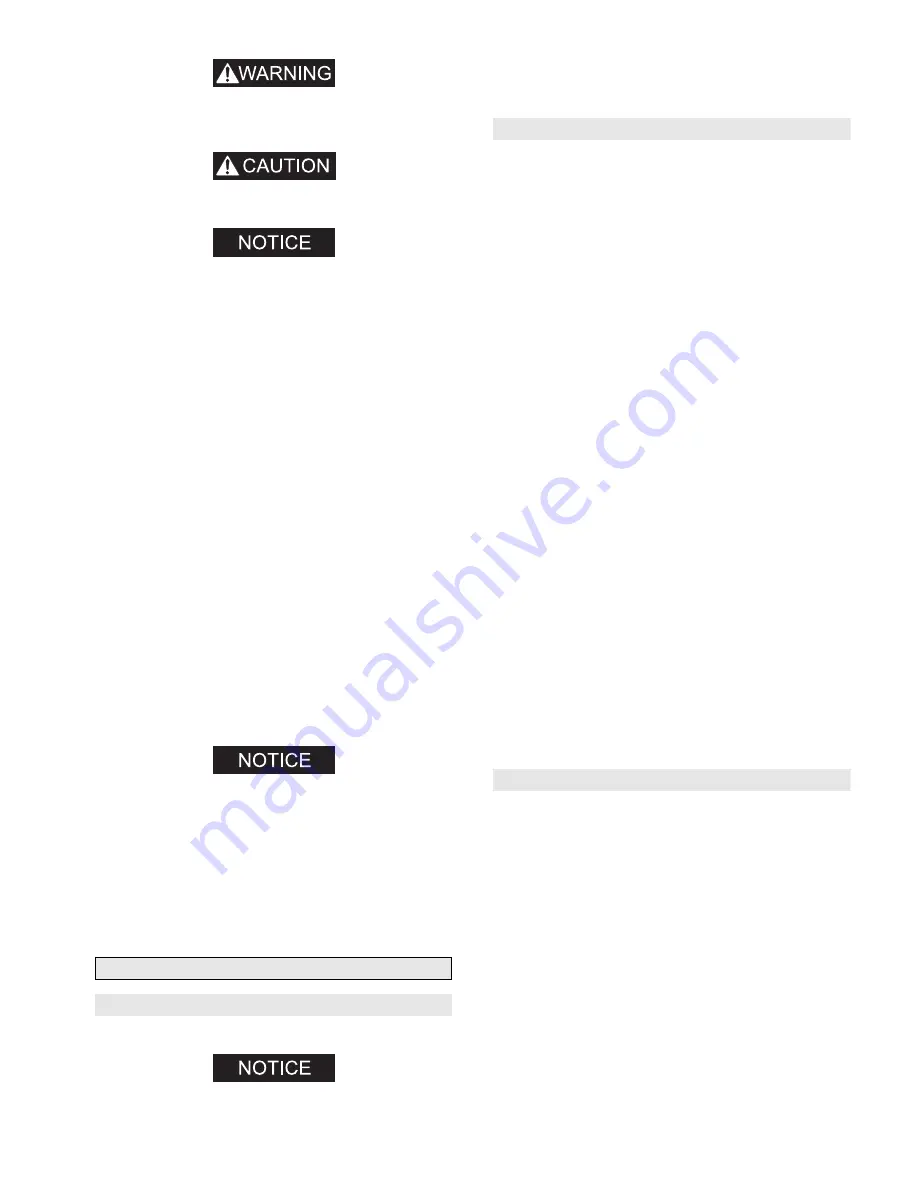
MHD56208 - Edition 3
15
• The air motor weighs approximately 134 lbs (61 kg).
Adequately support air motor before removing motor
mounting capscrews.
• Motor eyebolt is ONLY for lifting motor. Do NOT use to lift
entire motor and attached components.
• Internal components of the motor are machined to very close
tolerances. Ensure that work area and parts are kept very
clean to prevent damage or contamination of components.
• Motor capscrews are 13 mm (wrench size for M8 capscrews).
1.
Use a suitable hoist to support the motor assembly.
2.
Place motor on a suitable clean bench with rotary housing
assembly (9) facing up.
3.
Remove capscrews (2) and washers (3) from rotary housing
cover (4). Remove cover and gasket (5). Discard gasket.
4.
Remove capscrews (2) and washers (3). Lift rotary housing
assembly (9) up off motor housing (28). Remove and discard
gasket (13).
5.
Remove retainer (6) and press rotary valve (15) out of
housing.
6.
Pull bearings (14) and (7) out of rotary housing.
7.
Press rotary valve bushing (12) out of rotary housing.
8.
Remove capscrews (2) and washers (3) from cylinder caps
(17). Remove caps and gaskets (18). Discard gaskets.
9.
Lift out cylinders (19). Piston rings (21) will fall free when
clear of cylinder. Remove and discard ‘O’ ring (22).
10. Carefully rotate crankshaft (25) until piston assembly (23) is
centered in motor housing (28). Lift piston assembly straight
up. Repeat for remaining piston assembly.
11. Remove capscrews (2) and washers (3).
12. Remove plate (45) and discard gasket (44).
13. Remove retainer (42) and discard seal (43).
14. Remove retainer ring (31) and press crankshaft (25) out of
motor housing (28).
15. Remove retainer ring (26) and press out bearing (27).
• For Fenner style motors follow disassembly instructions 1
through 10 and 16 through 17.
16. Remove capscrews (10), retainer ring (8) and bearing (7)
from plate (45).
17. Remove plate (45) and discard gasket (44).
18. Remove retainer ring (31) and press crankshaft (25) from
motor housing (28) taking care not to lose key (20) from
crankshaft.
19. Remove retainer ring (26) and press out bearing (27).
Cleaning, Inspection and Repair
Cleaning
Clean all motor component parts in solvent.
• Do not clean any motor bearings with solvent.
The use of a stiff bristle brush will facilitate removal of
accumulated dirt and sediments on housing. Dry each part using
low pressure, filtered compressed air.
Inspection
All disassembled parts should be inspected to determine their
fitness for continued use. Pay particular attention to the following:
Inspect
bushing
for
• wear, scoring or galling. If evident, replace.
Inspect
shafts
for
• ridges caused by wear. If evident, replace.
• scoring or galling.
Inspect
all threaded items
for
• damaged threads. If evident, replace.
Inspect
motor cylinder bores
for
• wear. Cylinders can be lightly honed. For any large scratches
or wear patterns, replace cylinder assembly.
Inspect
motor rotary valve (15) and rotary bushing
for
• clearance between valve and bushing. Nominal gap is
0.00125-0.00225 inch (0.0318-0.0572 mm) per side for a
total of 0.0025-0.0045 inch (0.0635-0.1143 mm). If gap is
greater than 0.0025 inch (0.064 mm) per side, or greater than
0.005 inch (0.127 mm) total replace rotary bushing.
• rotary valve and bushing should not come into contact. If
contacting, bushing may be honed to eliminate the
interference. Bearings on end of rotary valve may be cause of
contact; check bearings (7) and (14) for excessive play and
proper press fit. Replace bearings if required.
• any time bushing or valve is replaced, replace bearings.
Inspect
piston/connecting rod assembly
for
• wear, scoring. Replace if either condition exists.
• connecting rod should operate smoothly without binding and
without excessive side to side play.
Inspect
bearings
for
• all motor bearings are factory lubricated and sealed. Inspect
for loss of grease and evidence of grit, dirt or other
contaminants. If dry or contaminated, replace the bearing.
• Inspect crankshaft roller bearings (needle). At any indication
of damage, or contamination replace bearings.
Inspect
crank pin bushing
, located in rotary valve, for
• wear, scoring or damage. Replace if either condition exists.
• if bushing is not flush with outside face of rotary valve or is
damaged it should be removed and replaced.
Repair
Actual repairs are limited to the removal of small burrs and other
minor surface imperfections from shafts, housings and machined
surfaces. Use a fine stone or emery cloth for this work.
1.
Worn or damaged parts must be replaced. Refer to applicable
parts listing for specific replacement parts information.
2.
Inspect all remaining parts for evidence of damage. Replace
or repair any part which is in questionable condition. The
cost of the part is often minor in comparison with the cost of
redoing the job.
3.
Smooth out all nicks, burrs, or galled spots on shafts, bores,
pins, or bushings.
4.
Polish edges of all shaft shoulders to remove small nicks
which may have been caused during handling.
5.
Remove all nicks and burrs caused by lockwashers.
6.
Examine crankshaft spline carefully, and remove nicks or
burrs.
Содержание MMP150
Страница 5: ...MHD56208 Edition 3 5 Dwg MHP2004...
Страница 23: ...MHD56208 Edition 3 23 SERVICE NOTES...
Страница 26: ...26 MHD56208 Edition 3 SERVICE NOTES...
Страница 36: ...www irtools com...