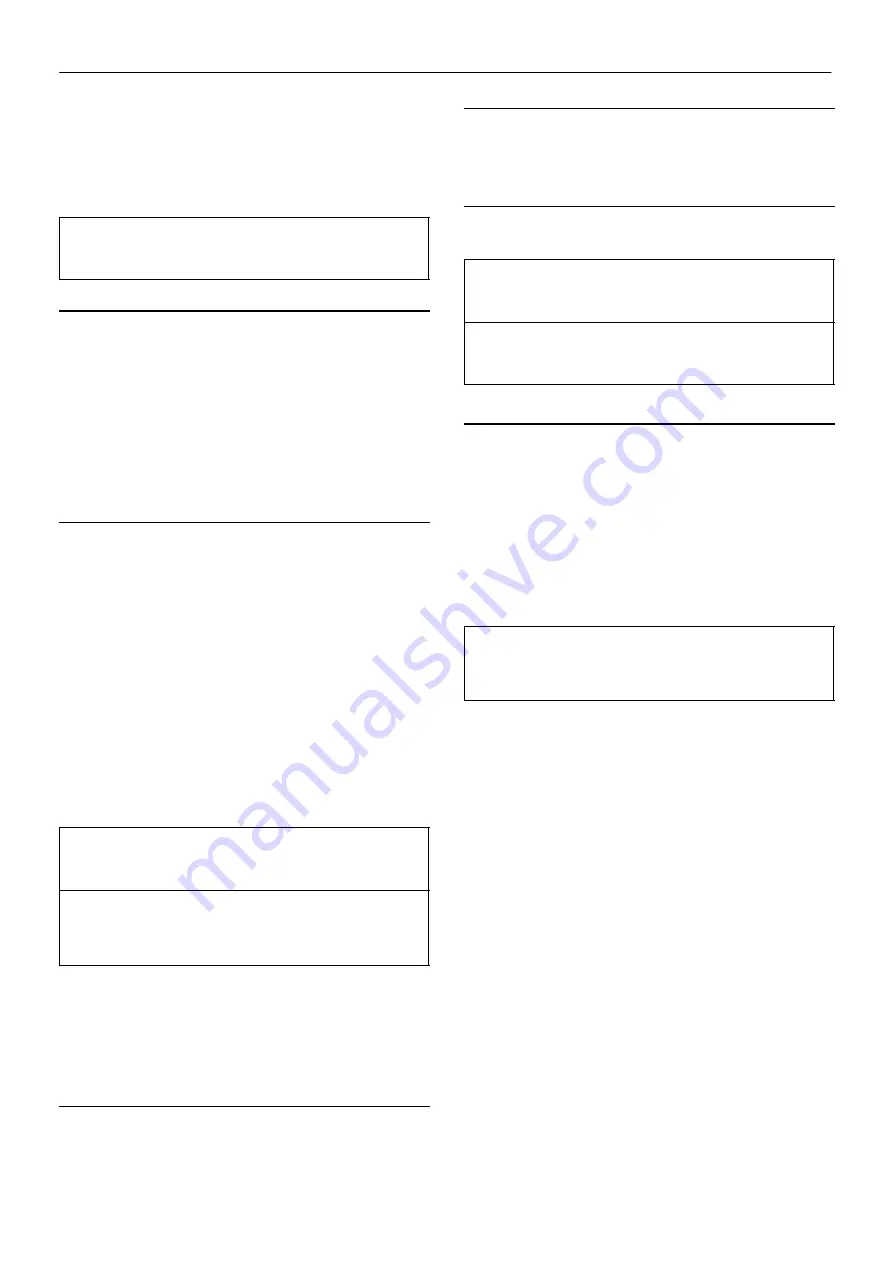
MAINTENANCE
35
M200–LV M250–LV
.
Start the compressor and check for leaks.
.
Check the coolant level, refilling if necessary.
.
Dispose of waste coolant in accordance with local and
governmental regulations.
NOTE
Shorter coolant drain intervals may be necessary if the compressor
is operated in adverse conditions.
AIR FILTER CHANGE PROCEDURE
Removal
WARNING: Do not remove the filter(s) without first making sure
that the machine is stopped and the system has been completely
relieved of all air pressure. (Refer to STOPPING THE MACHINE in
the OPERATING INSTRUCTIONS section of this manual).
Remove the wing-nuts securing the filter cover and remove the
housing lid.
Fit the new element(s) and re–assemble the components in reverse
order.
SEPARATOR ELEMENT CHANGE PROCEDURE
Remove the roof panel to gain access to the top of the separator
tank.
.Disconnect the scavenge tube from the airend and loosen the fitting
that secures the scavenge tube to the separator tank cover and then
remove the scavenge tube.
Disconnect the blowdown system hose assembly and the minimum
pressure valve.
.
Remove the setscrews securing the cover to the tank and remove
the complete cover assembly.
.
Withdraw the used element, place it in a sealed bag and dispose of
it safely.
.
Clean the gasket surface on both the tank and the cover.
CAUTION
Do not use any form of sealant on either the separator tank or the
separator tank cover faces.
WARNING
Do not remove the staple from the anti–static gasket on the
separator element since it serves to ground any possible static
build–up.
.
Install the replacement element.
.
Re–assemble the components in reverse order.
.
Start the compressor and check for leaks.
AIREND BEARINGS
Airend bearings are lubricated by the compressor coolant and
require no maintenance.
MOTOR BEARINGS
Clean the area around the grease nipple and remove the protective
cover. Add the correct amount of grease (refer to the
SERVICE/MAINTENANCE CHART earlier in this section). Replace
the protective cover and clean the area of surplus grease.
MOTOR BEARING LUBRICANT SPECIFICATION
Use ESSO UNIREX N3 grease or equivalent.
CAUTION:
Do not over pack the motor bearings with grease as this may lead
to motor failure.
CAUTION:
Ensure dirt and/or other contaminants are not introduced into the
bearing during the greasing process.
H.A.T. SENSOR CHECKING PROCEDURE
It is recommended that the discharge temperature sensor is
checked regularly as follows:
AIr cooled machines
Stop the cooling fan by opening the fan motor circuit breaker.
Water cooled machines
Shut off the cooling water.
The machine should trip at 109
_
C standard.
CAUTION:
Under no circumstances should these discharge temperatures be
exceeded. If the machine fails to trip A FAULT EXISTS. Investigate
immediately.
The temperature at which the machine stops should be recorded for
comparison with future results.